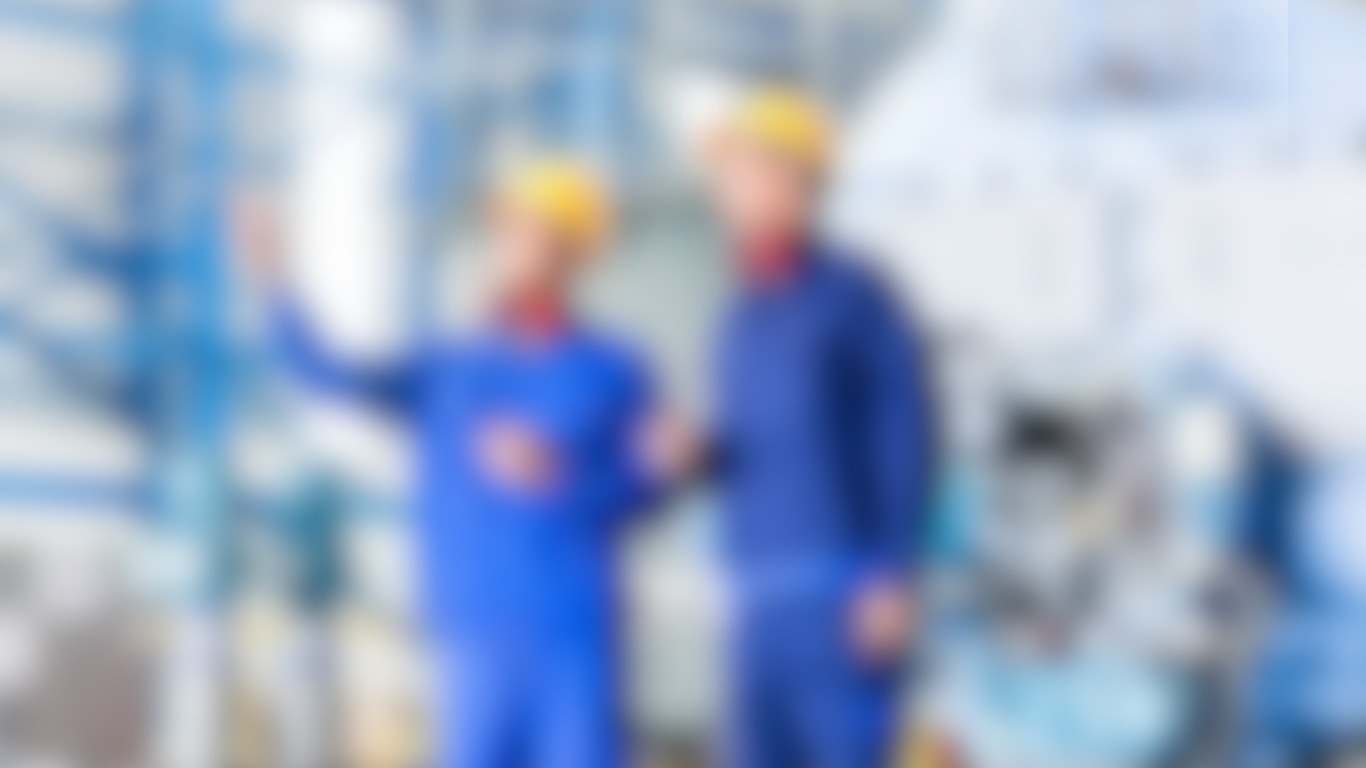
Planned Maintenance (PM)
Implementing the right Planned Maintenance (PM) strategy is essential for maximising asset reliability, reducing downtime, and optimising maintenance resources.
At MCP Consulting Group, we provide tailored consultancy services to help organisations understand, implement, and optimise different types of planned maintenance approaches, ensuring a structured and effective asset management strategy.
MAINTENANCE PLANS SUB-CATEGORIES
What is
Planned Maintenance (PM)
Planned Maintenance (PM) refers to scheduled maintenance activities designed to prevent asset failures, improve equipment reliability, and ensure operational efficiency. PM strategies can vary depending on asset criticality, failure risks, and operational demands, with organisations typically using a combination of preventive, predictive, and condition-based maintenance approaches.
At MCP, we support businesses in selecting and implementing the most suitable planned maintenance types, aligning them with business goals, industry standards, and technological capabilities.
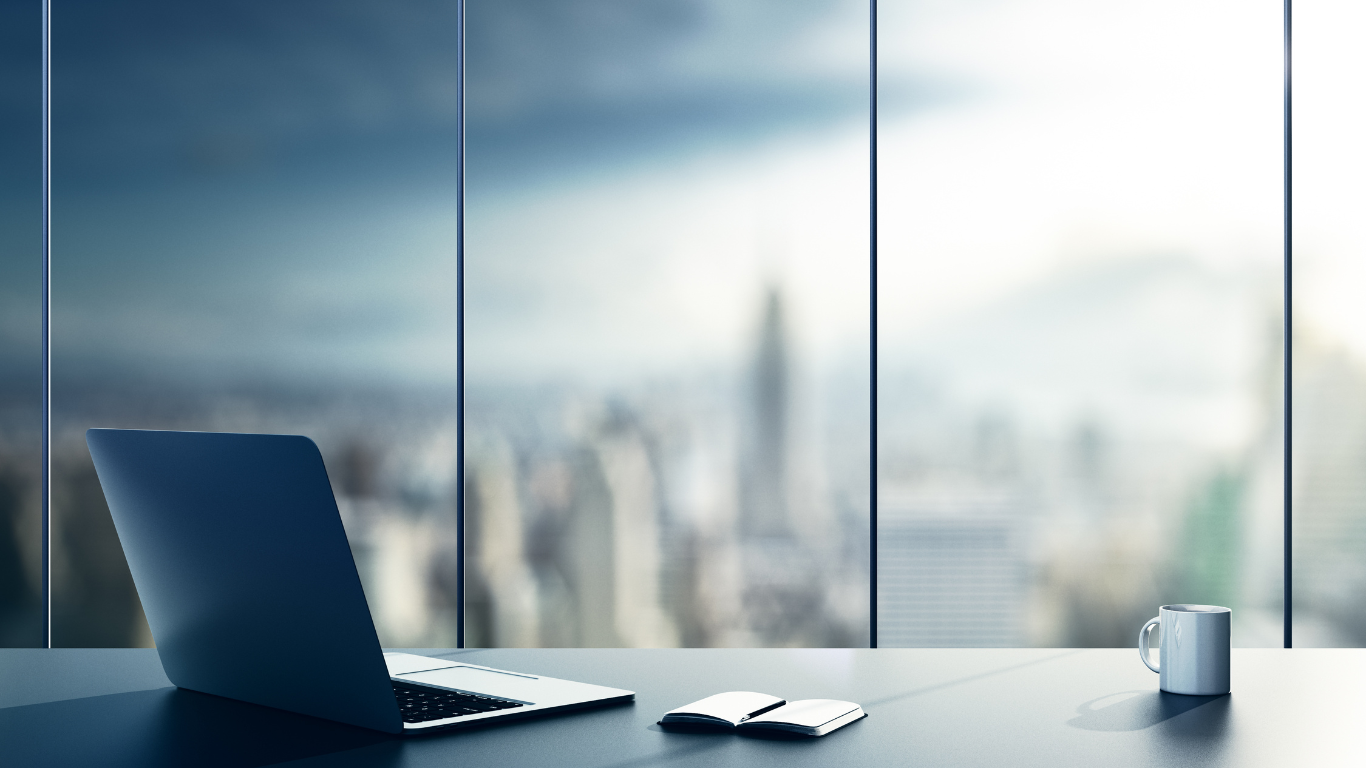
Key Objectives of
Planned Maintenance (PM)
Implement structured preventive and predictive maintenance approaches to minimise equipment breakdowns.
1
Reducing Unexpected Failures
Optimising Maintenance Intervals
2
Develop tailored maintenance schedules to balance reliability, cost, and operational efficiency.
Enhancing Asset Performance and Lifespan
3
Apply the right PM techniques to reduce wear and tear and extend asset life.
Reduce unnecessary interventions while ensuring that maintenance activities are efficient and cost-effective.
4
Minimising Maintenance Costs
Ensuring Compliance and Safety
5
Align planned maintenance activities with industry regulations and safety standards to minimise risks.
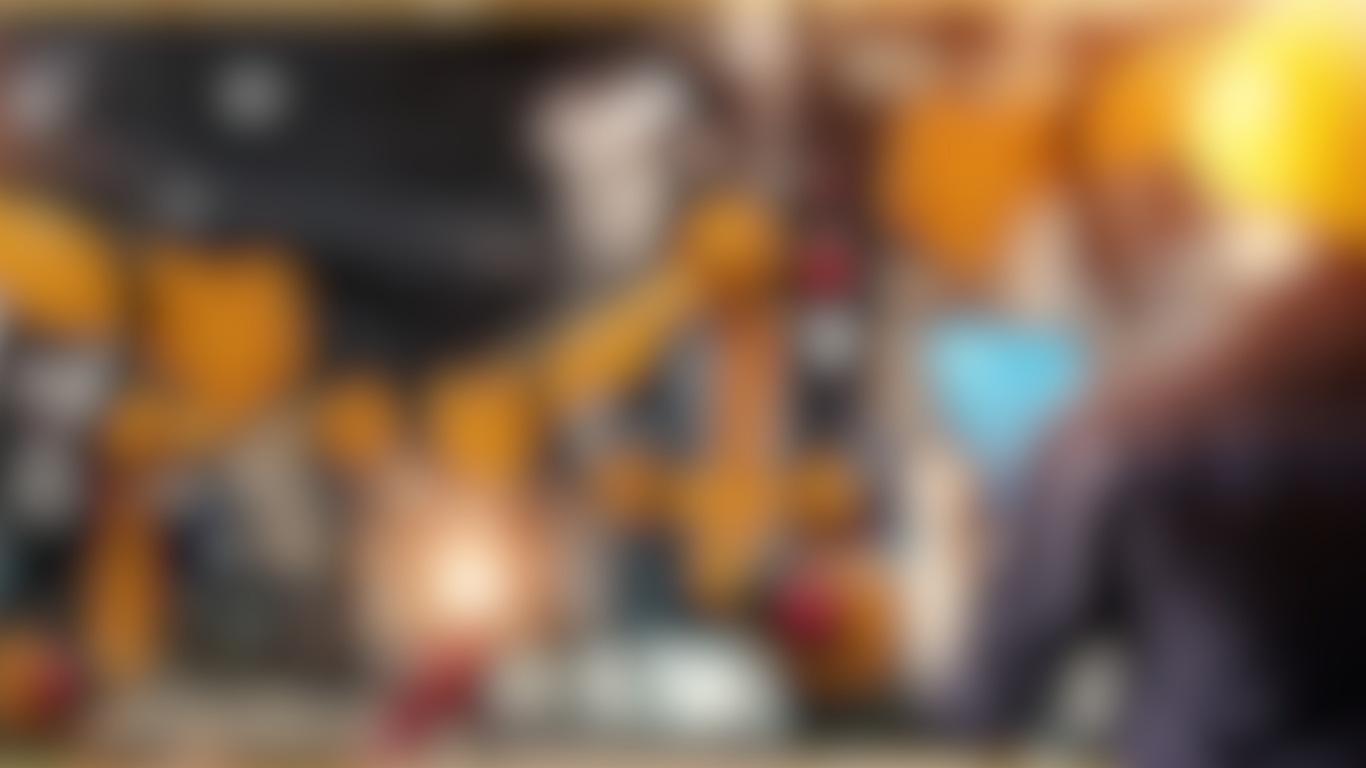
Types of
Planned Maintenance
Planned maintenance refers to scheduled maintenance activities designed to prevent unexpected failures and optimise asset performance. MCP helps organisations define the right mix of planned maintenance types to maximise efficiency and cost-effectiveness.
Maintenance tasks scheduled at regular intervals to reduce the risk of failure.
Based on time, usage, or manufacturer recommendations.
Examples: Lubrication, calibration, filter replacements, inspections.
Addressing minor issues before they escalate into major failures.
Often identified through inspections and condition monitoring.
Examples: Tightening loose connections, replacing worn parts.
Uses real-time data and analytics to determine optimal maintenance timing.
Monitors vibration, temperature, oil levels, and other key indicators.
Examples: Vibration analysis, infrared thermography, oil condition monitoring.
1
2
3
PREVENTATIVE MAINTENANCE (PM)
CORRECTIVE MAINTENANCE (CM)
PREDICTIVE MAINTENANCE (PdM)
4
CONDITION-BASED MAINTENANCE (CBM)
DESIGN-OUT MAINTENANCE
Maintenance performed only when an asset shows signs of deterioration.
Uses sensors and real-time monitoring to detect potential failures.
Examples: Pressure readings, fluid level checks, performance tracking.
5
Focuses on engineering improvements to eliminate the root causes of failures.
Examples: Upgrading materials, redesigning components, process modifications.
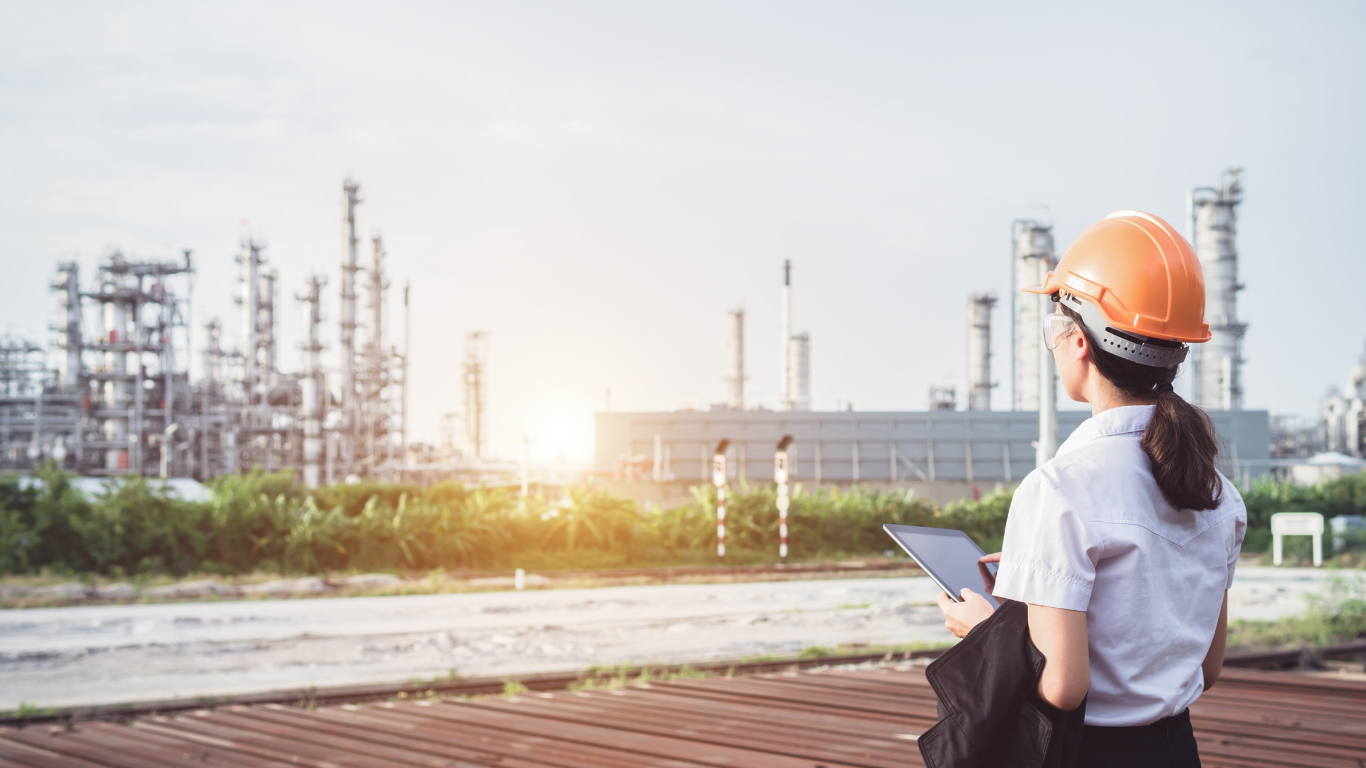
MCP Approach to
Planned Maintenance Implementation
Assessing Asset Needs and Operational Requirements
MCP works with organisations to evaluate asset performance, failure history, and criticality to determine the most suitable planned maintenance types.
Developing Customised Maintenance Strategies
We help businesses define and implement structured PM schedules, ensuring that maintenance interventions align with operational goals and risk levels.
Integration with CMMS and Digital Solutions
Our consultants assist in integrating PM strategies with Computerised Maintenance Management Systems (CMMS) and other digital asset management platforms.
Training and Change Management
MCP provides workforce training to ensure teams understand and effectively execute planned maintenance strategies.
Continuous Review and Optimisation
We support organisations in monitoring and refining PM programmes, ensuring continuous improvement and alignment with evolving business needs.
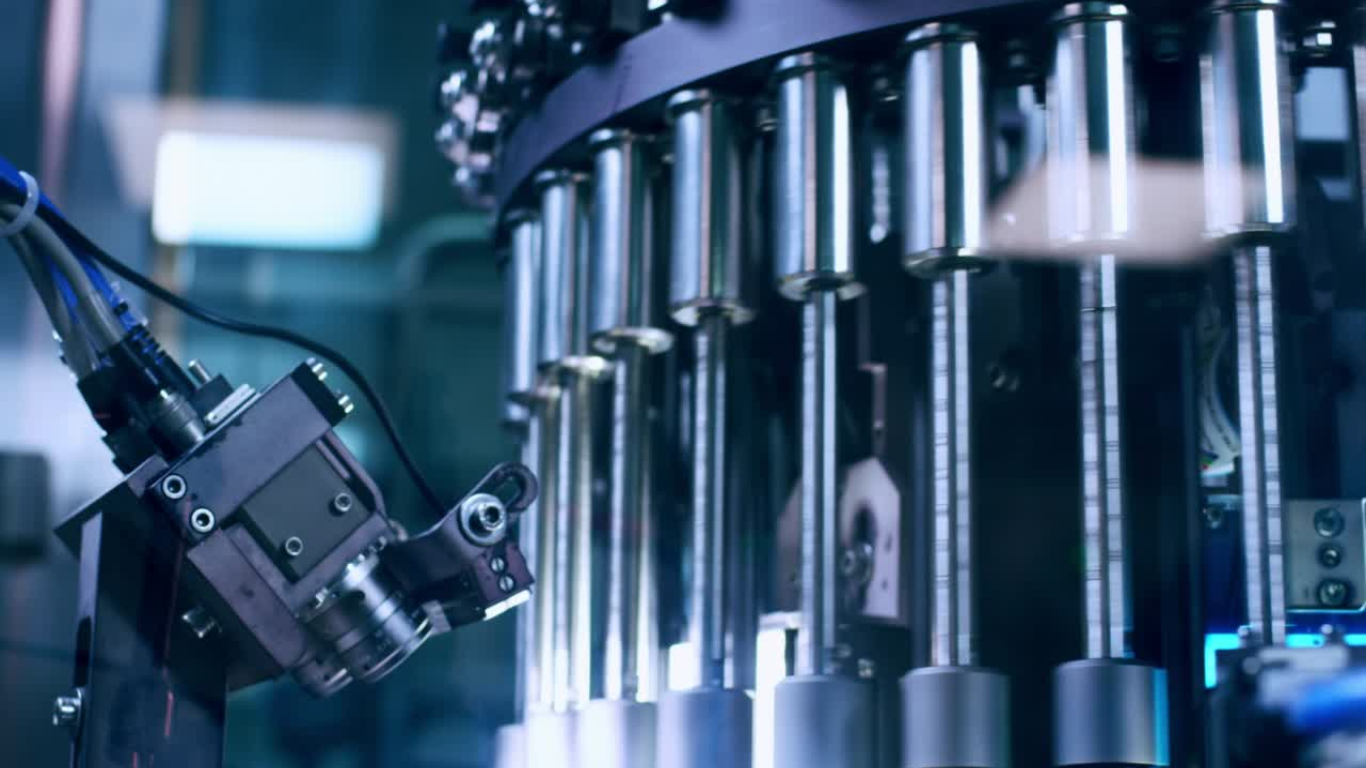
Maintenance Plans
Explore More
Speak to One of Our
Experienced Consultants
If you have any questions or would like to learn more about how MCP Consulting Group can support your organisation with Planned Maintenance Types and implementation, please get in touch with us.
Our team of consultants is ready to provide tailored solutions to optimise maintenance planning, improve resource allocation, and enhance asset performance. Contact us today to discuss your specific requirements.
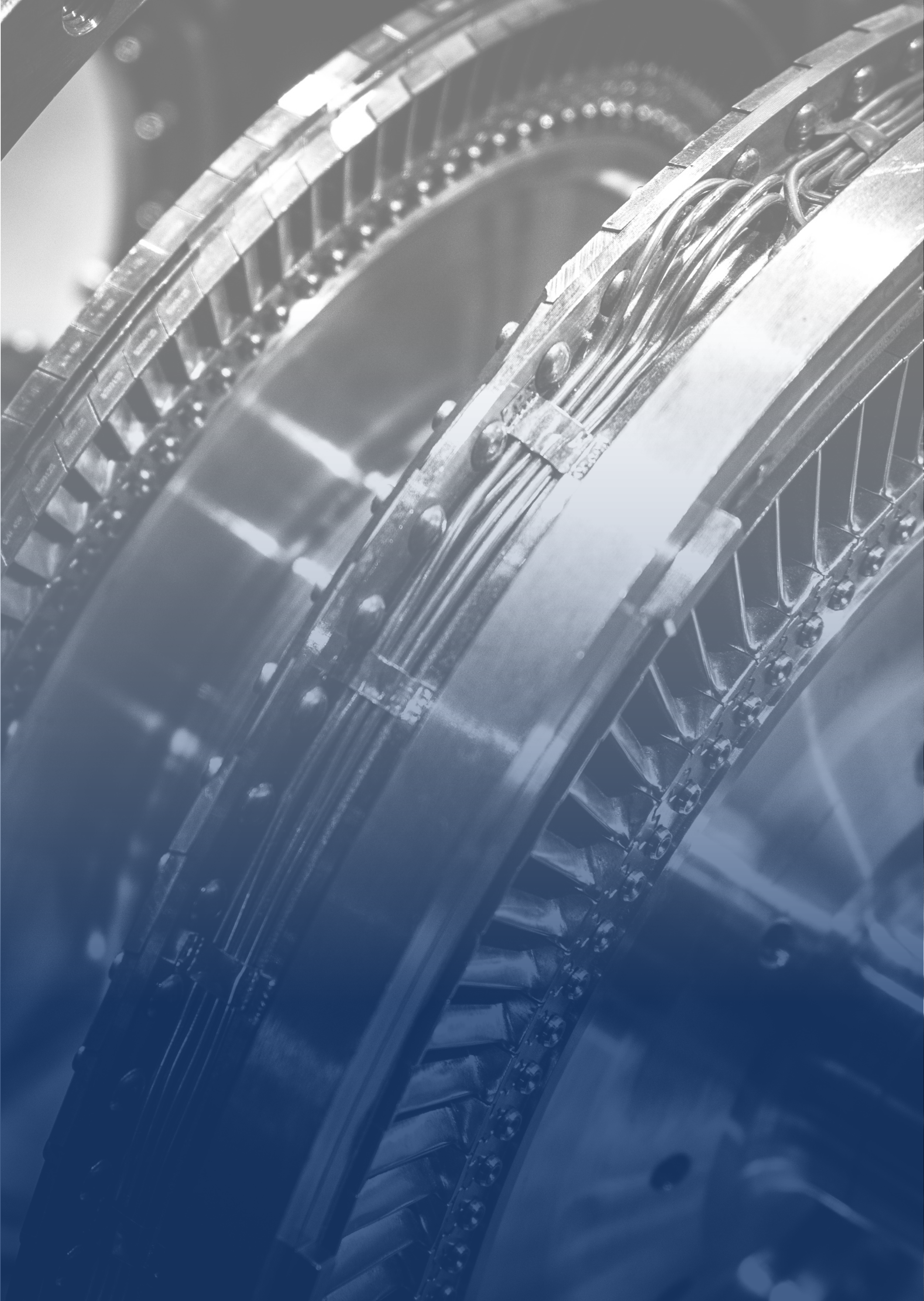
FAQs
-
Preventive maintenance follows a fixed schedule, while predictive maintenance uses real-time monitoring and analytics to determine the optimal time for interventions.
-
Planned maintenance is focussed on identifying and providing all the required resources to carry out a maintenance job whilst an unplanned job does not have the benefit of having the resources ready thus increasing cost and equipment downtime.
-
Planned maintenance reduces emergency repairs, extends asset life, and improves operational efficiency, leading to long-term cost savings.
-
Industries with asset-intensive operations, such as manufacturing, energy, healthcare, and transportation, benefit significantly from structured PM programmes.
-
A CMMS automates work order scheduling, tracks asset health, and optimises PM execution, ensuring maintenance activities are data-driven and efficient.
-
PM strategies should be reviewed annually or when significant changes occur in asset performance, operational demands, or regulatory requirements.