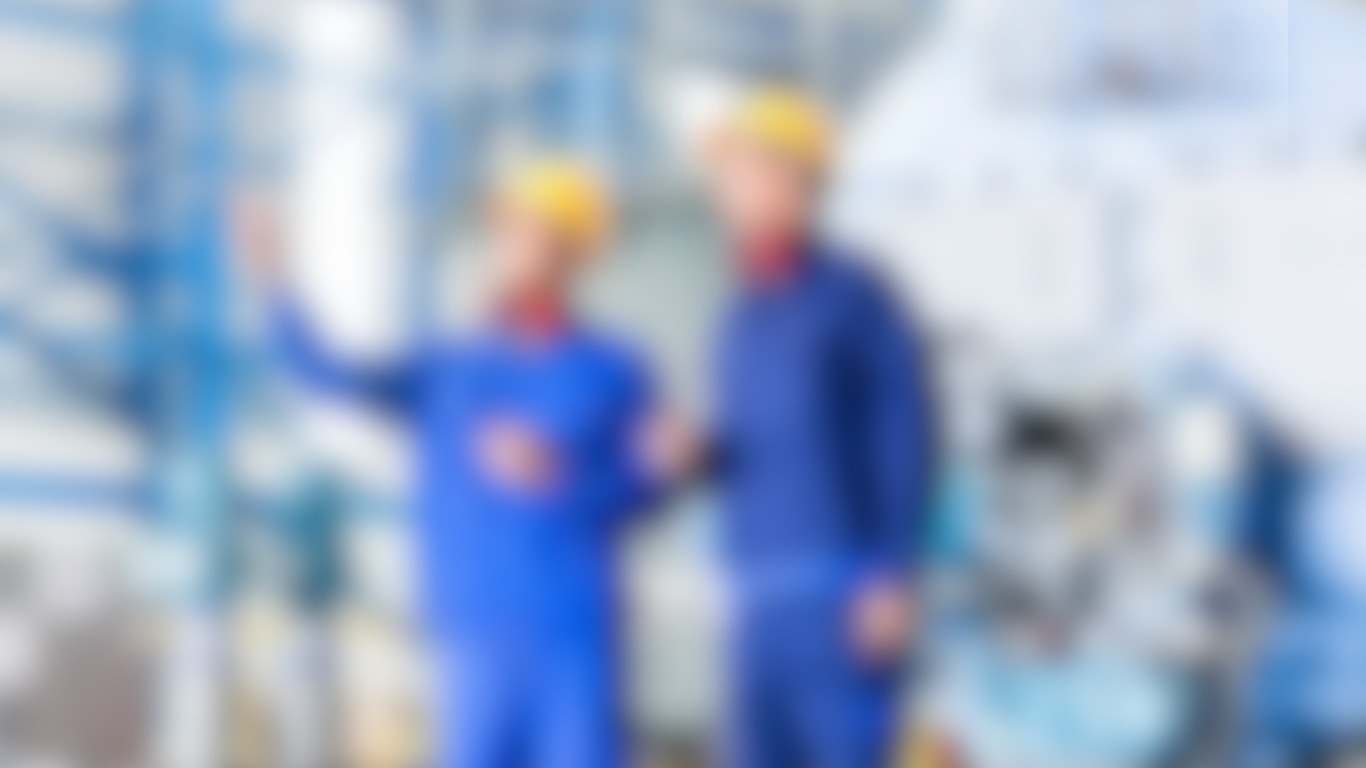
Equipment Criticality
Understanding equipment criticality is essential for prioritising maintenance efforts, optimising resource allocation, and mitigating operational risks.
At MCP Consulting Group, we provide tailored consultancy services to help organisations assess and classify assets based on their criticality, ensuring a structured and risk-based approach to maintenance planning.
MAINTENANCE PLANS SUB-CATEGORIES
What is
Equipment Criticality
Equipment Criticality Analysis is the process of evaluating assets based on failure impact, operational dependency, safety, risk and cost implications. Criticality determines the relative importance of each asset or asset system, based on the impact and probability of a failure. By determining which equipment is most critical to business continuity, organisations can prioritise maintenance resources, reduce downtime, and improve asset performance.
At MCP, we support organisations in developing risk-based maintenance strategies, ensuring that high-criticality assets receive the appropriate preventive, predictive, and condition-based maintenance interventions.
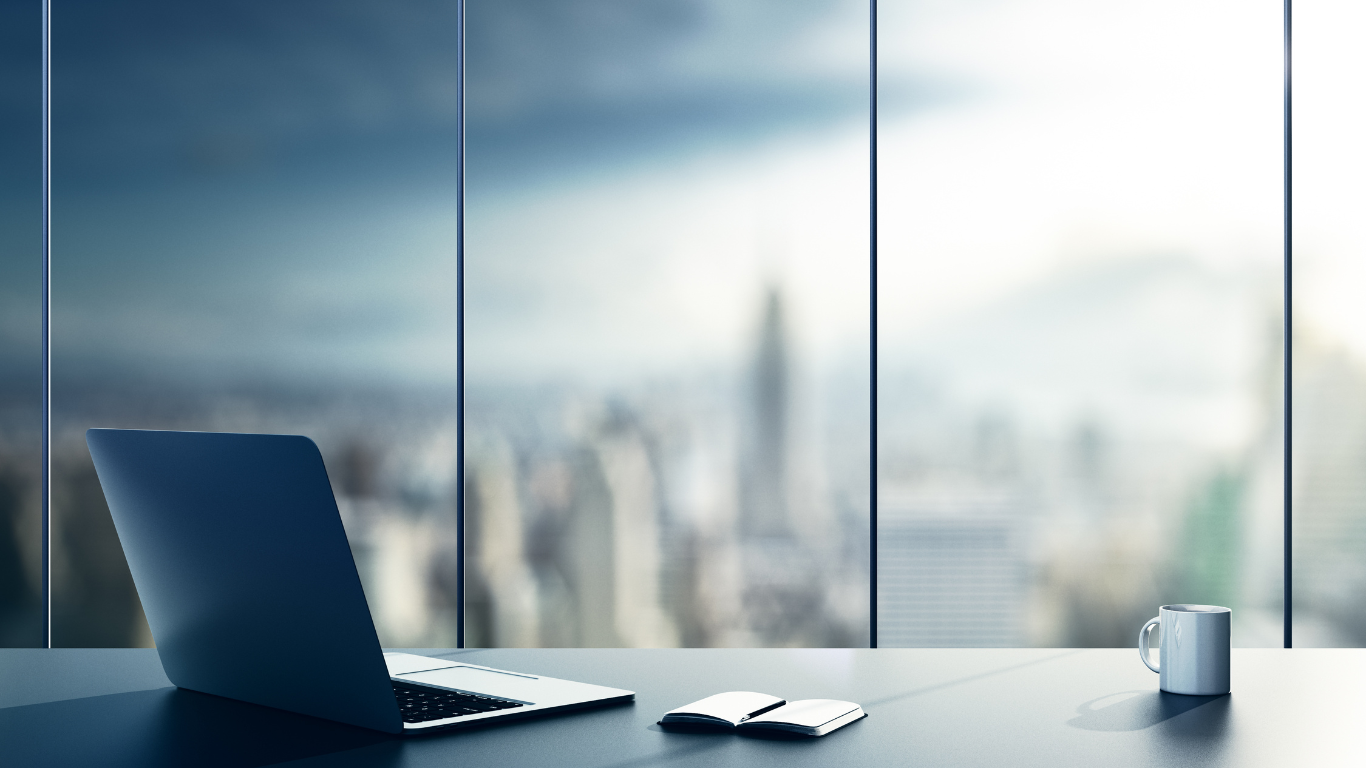
Key Objectives of
Equipment Criticality
Identify high-risk assets that require focused maintenance efforts to prevent failures.
1
Prioritising Maintenance Activities
Optimising Resource Allocation
2
Ensure that labour, materials, and budgets are directed towards the most critical equipment.
Reducing Operational Disruptions
3
Minimise downtime by targeting maintenance activities on equipment essential to business continuity.
Support proactive maintenance planning by ranking equipment based on failure likelihood and impact.
4
Enhancing Risk-Based Decision-Making
Aligning Maintenance Strategy with Business Goals
5
Integrate equipment criticality into CMMS, asset management strategies, and capital planning.
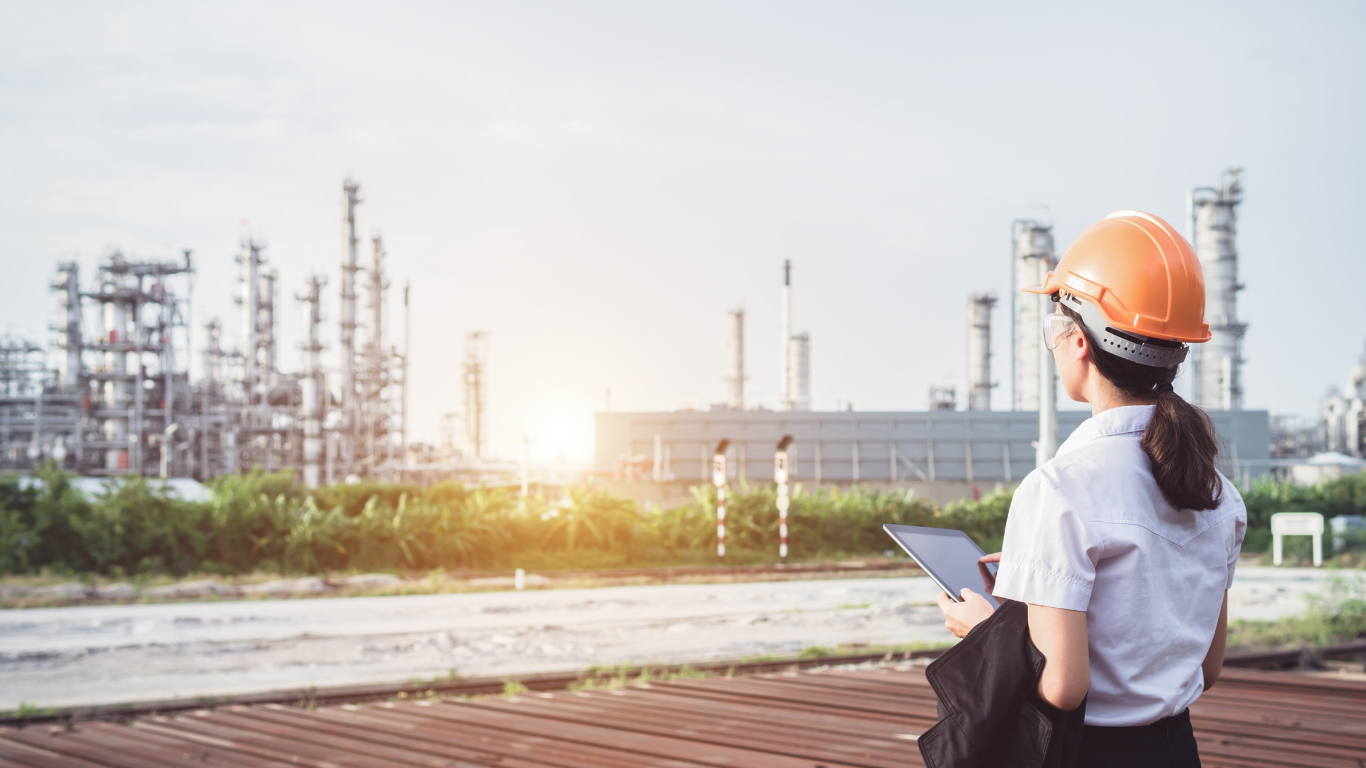
MCP Approach to
Equipment Criticality
Defining Criticality Criteria and Risk Factors
MCP works with organisations to develop customised criticality assessments based on a set of evaluation factors including safety, production impact, cost of failure and regulatory impact.
Failure Impact and Risk Assessment
We help businesses evaluate failure modes, downtime impact, and financial consequences, ensuring that maintenance priorities align with operational risks.
Integration with Preventive and Predictive Maintenance
Our consultants assist in aligning criticality rankings to support selection of preventive maintenance schedules, predictive analytics, and real-time condition monitoring.
CMMS and Asset Management System Integration
MCP supports the seamless integration of criticality rankings into CMMS platforms, ensuring automated maintenance prioritisation.
Strategic Maintenance and Continuous Review
We assist organisations in establishing periodic criticality reviews, ensuring that asset classifications remain up to date and relevant.
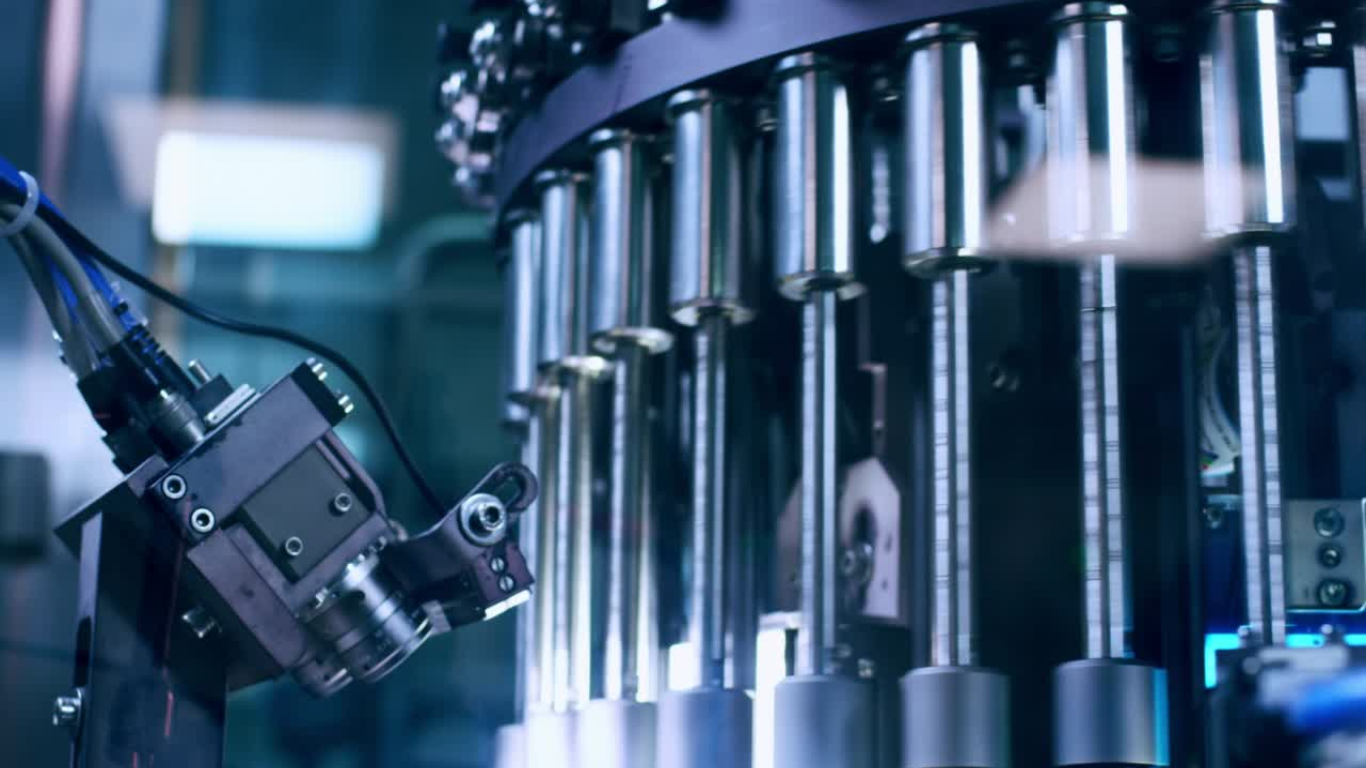
Maintenance Plans
Explore More
Speak to One of Our
Experienced Consultants
If you have any questions or would like to learn more about how MCP can support your organisation with Equipment Criticality Analysis, please get in touch with us.
Our team of consultants is ready to provide tailored solutions to optimise maintenance planning, improve resource allocation, and reduce operational risks. Contact us today to discuss your specific requirements.
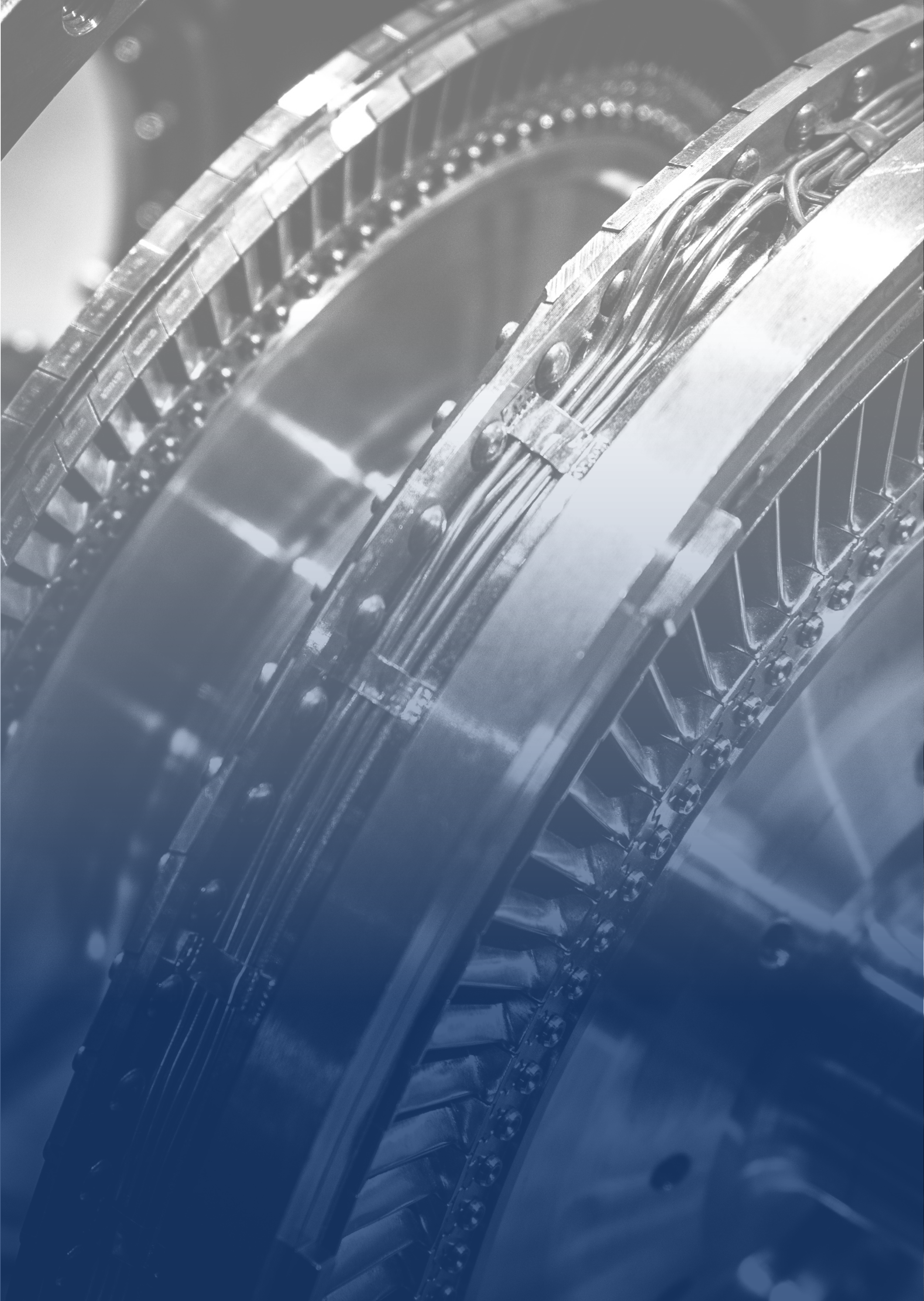
FAQs
-
It helps organisations focus maintenance efforts on high-risk assets, reducing failures and improving reliability.
-
Equipment criticality evaluates the impact of failure, while asset importance assesses strategic value within the business.
-
Criticality rankings help prioritise preventive maintenance, predictive analytics, work order planning and scheduling.
-
Yes, most CMMS platforms support criticality-based work prioritisation, asset tracking, and condition monitoring. Criticality also assists with loading of masterdata into new CMMS systems
-
It should be reviewed annually or when significant operational or regulatory changes occur.