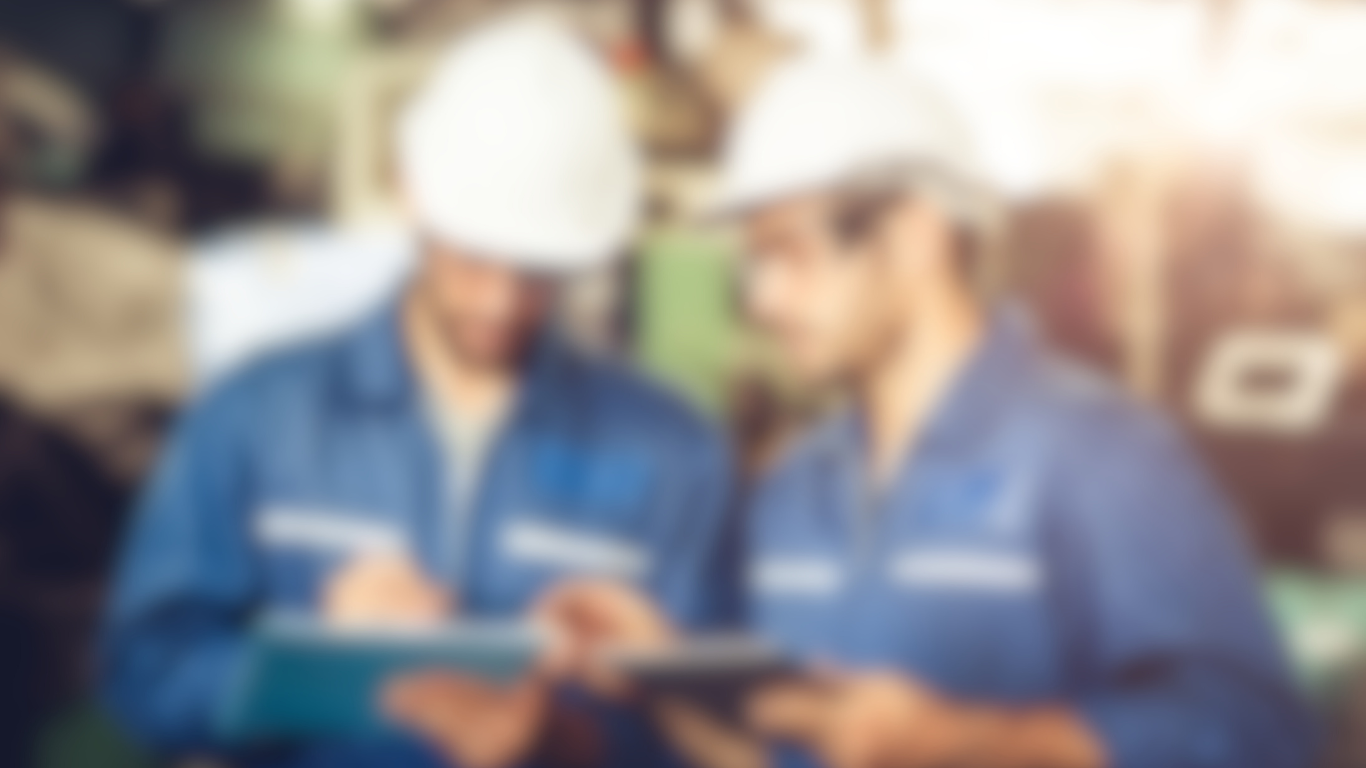
Total Productive Maintenance
Maximising asset performance while reducing downtime and maintenance costs is essential for any organisation. Total Productive Maintenance (TPM) is a proactive and systematic approach to improving equipment effectiveness through collaborative maintenance strategies.
At MCP Consulting Group, we provide consultancy services to help businesses implement, sustain, and optimise TPM programmes, enhancing operational efficiency and asset reliability.
TPM, AM and OAC SUB-CATEGORIES
What is
Total Productive Maintenance (TPM)
Total Productive Maintenance (TPM) is a company-wide maintenance approach that integrates maintenance activities into daily operations. TPM focuses on eliminating equipment-related losses, improving workplace efficiency, and empowering employees to take an active role in asset care.
TPM is built on eight key pillars that drive equipment reliability, reduce breakdowns, and improve workplace culture by fostering collaboration between maintenance and operations teams. At MCP, we help organisations implement these principles, ensuring that TPM initiatives deliver long-term performance improvements.
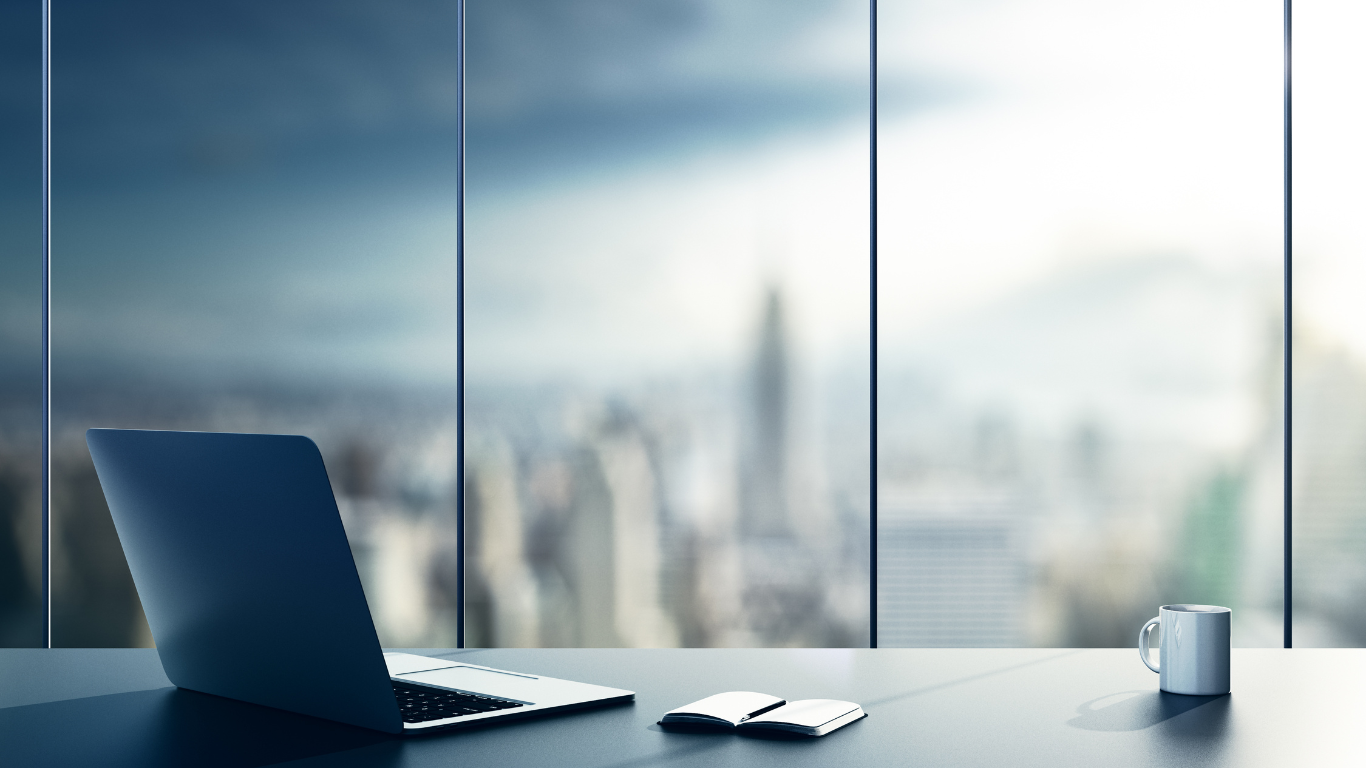
Key Objectives of
Total Productive Maintenance (TPM)
Implement structured preventive and autonomous maintenance practices to minimise unplanned breakdowns.
1
Reducing Equipment Downtime and Failures
Improving Overall Equipment Effectiveness (OEE)
2
Increase availability, performance, and quality to optimise equipment productivity.
Developing an Operator-Led Maintenance Culture
3
Equip frontline operators with basic maintenance skills to improve asset care and early fault detection.
Driving Continuous Improvement
Streamline maintenance activities to reduce waste, increase productivity, and improve workflow efficiency.
4
Enhancing Workplace Efficiency
5
Establish a culture of ongoing performance monitoring and optimisation through data-driven decision-making.
The
8 Pillars of TPM
Autonomous Maintenance (AM) – Operators take responsibility for basic maintenance tasks, e.g. cleaning, lubricating, and inspecting equipment.
1
Planned Maintenance – Scheduled preventive and predictive maintenance activities ensure equipment remains in optimal condition.
2
Focused Improvement – Cross-functional teams identify and eliminate root causes of inefficiencies and failures.
3
Early Equipment Management – Improve new equipment design and commissioning processes to enhance long-term reliability.
4
Quality Maintenance – Implement proactive strategies to reduce defects and improve product quality.
5
Education & Training – Provide technical and soft skills training to maintenance and operations teams to sustain TPM.
6
Safety, Health & Environment (SHE) – Ensure that TPM initiatives align with safety, environmental, and regulatory requirements.
7
TPM in Administration – Extend TPM principles beyond the shop floor to improve business and administrative processes.
8
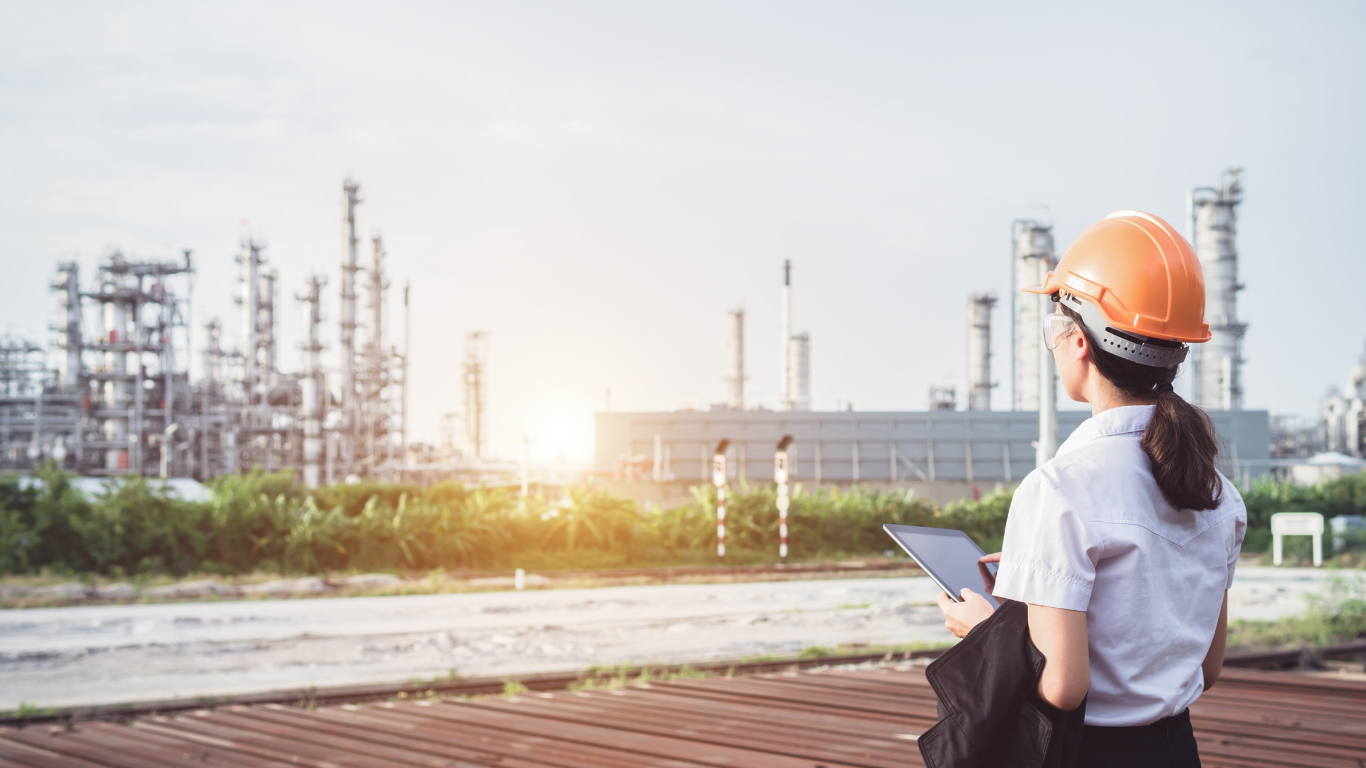
MCP Approach to
Total Productive Maintenance (TPM)
TPM Readiness Assessment
MCP assesses current maintenance practices, operational processes, and organisational culture to determine TPM implementation readiness.
Developing a Customised TPM Framework
We help organisations define their TPM vision, objectives, and roadmap, ensuring alignment with business goals and operational priorities.
Training & Workforce Engagement
Our consultants train operators, technicians, and managers to ensure successful TPM adoption and sustainment.
Establishing Autonomous and Planned Maintenance
We assist businesses in implementing structured maintenance programmes, combining operator-led maintenance and advanced predictive techniques.
Continuous Performance Monitoring and Improvement
MCP provides ongoing TPM assessments, measuring OEE improvements and refining maintenance strategies for long-term success.
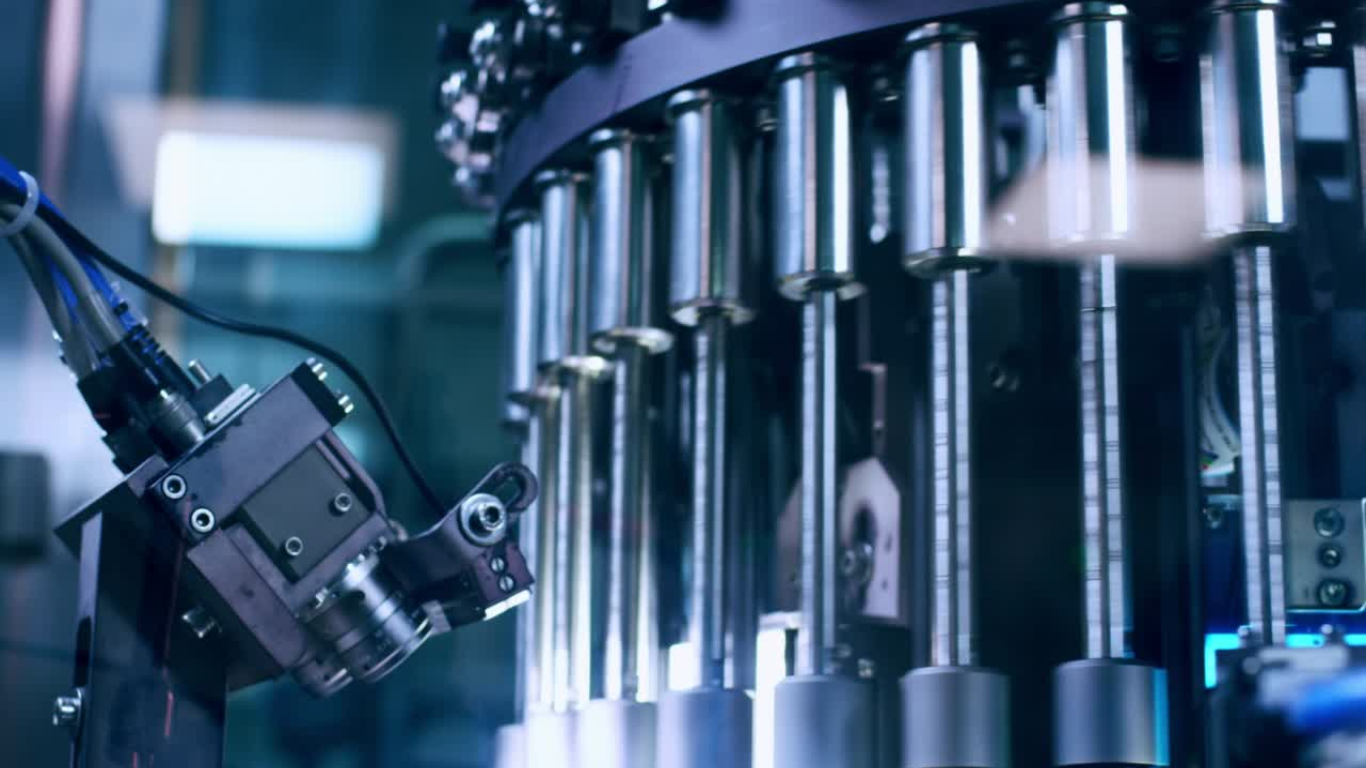
TPM, AM and OAC
Explore More
Speak to One of Our
Experienced Consultants
If you have any questions or would like to learn more about how MCP Consulting Group can support your organisation with Total Productive Maintenance, please get in touch with us.
Our team of consultants is ready to provide tailored solutions to optimise maintenance strategies, improve equipment reliability, and enhance workplace efficiency. Contact us today to discuss your specific requirements.
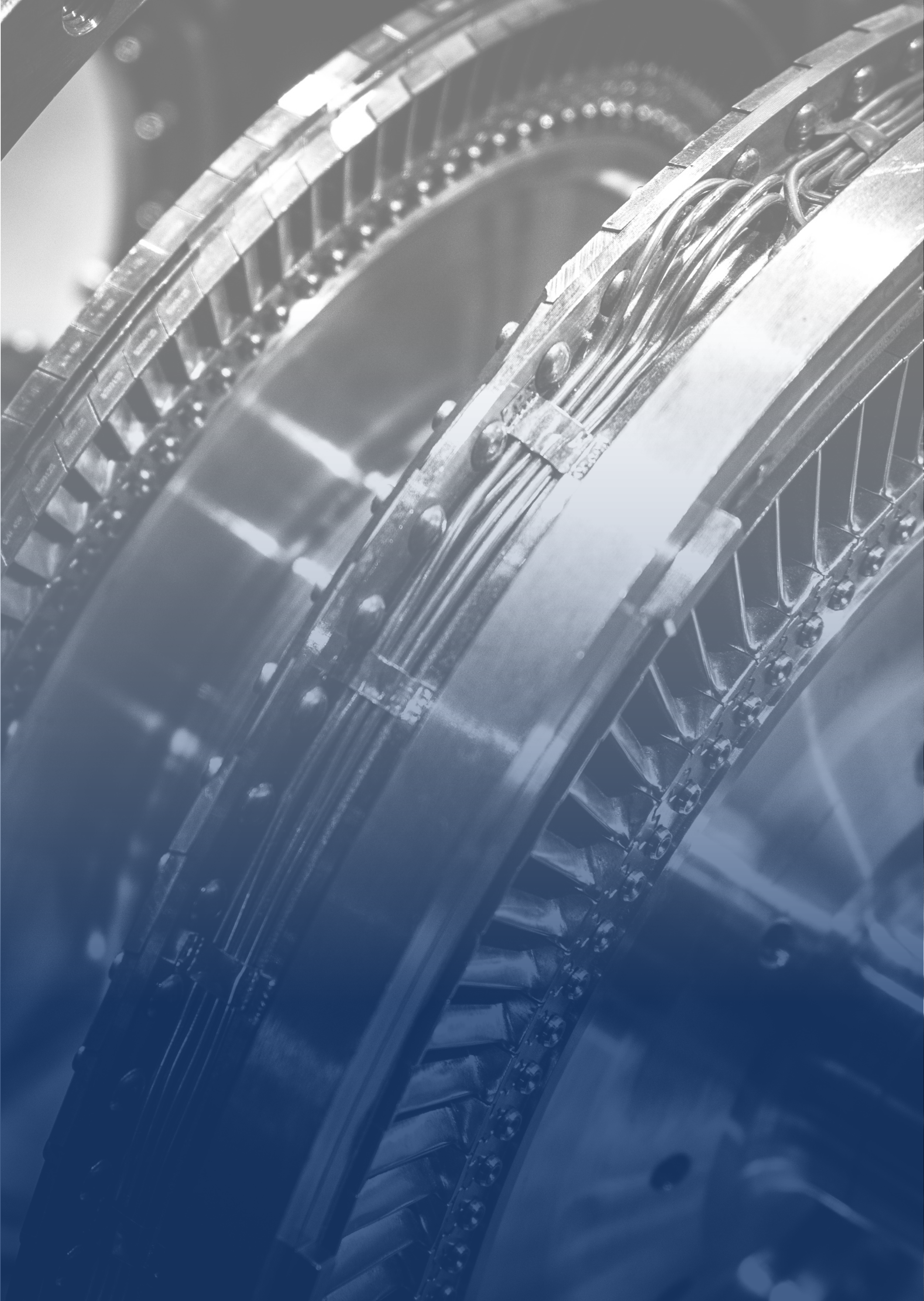
FAQs
-
TPM integrates maintenance into daily operations, focusing on proactive asset care, teamwork, and continuous improvement, unlike traditional maintenance, which often reacts to failures.
-
The timeframe depends on organisational size, readiness, and existing maintenance practices, but full TPM adoption typically takes several months to years.
-
Yes, TPM is beneficial in manufacturing, energy, healthcare, food processing, logistics, and other asset-intensive industries.
-
Operators take ownership of daily asset care, performing basic maintenance tasks to identify and prevent early-stage failures.
-
By reducing downtime, improving performance, and minimising defects, TPM directly enhances OEE and production efficiency.