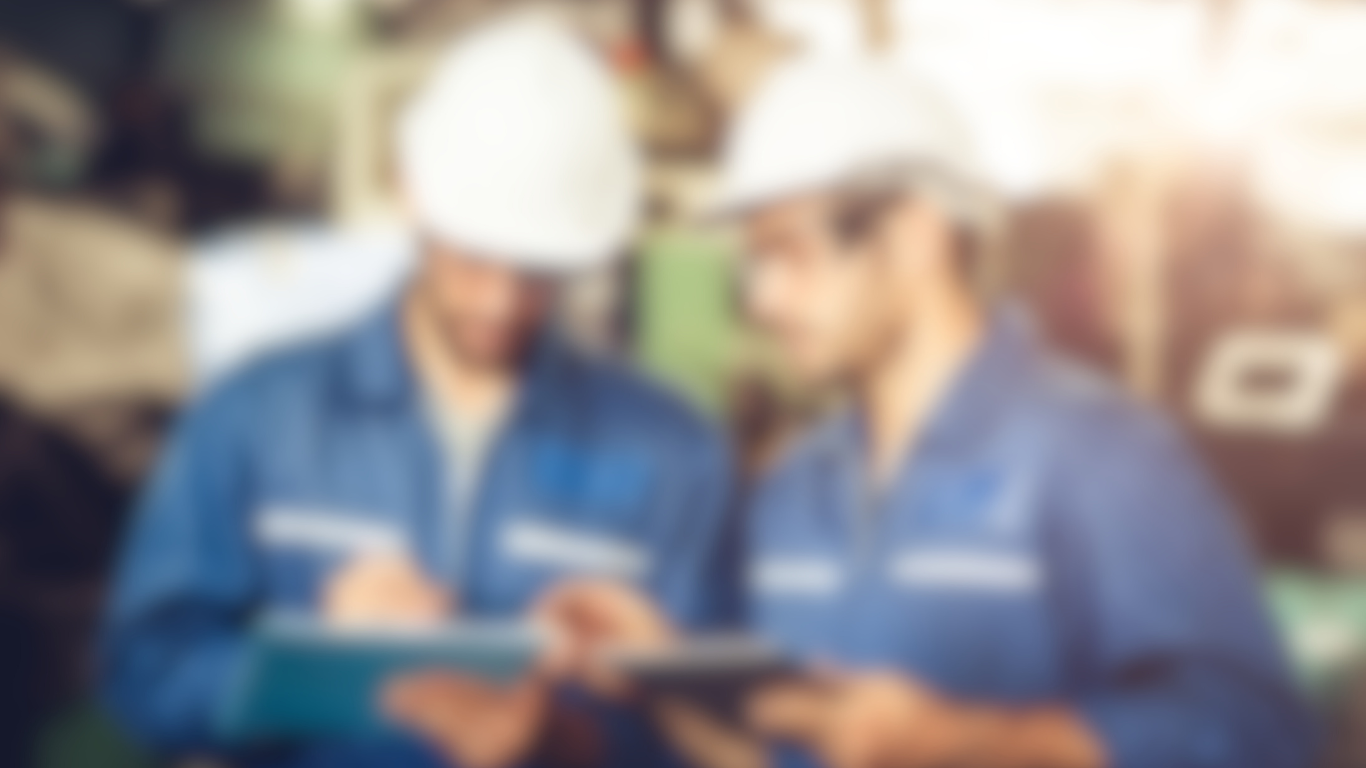
Autonomous Maintenance (AM)
Empowering operators to take an active role in equipment maintenance is a key pillar of Total Productive Maintenance (TPM). Autonomous Maintenance (AM) shifts routine maintenance tasks from technicians to operators, enabling a proactive, efficient, and collaborative approach to asset care whilst enriching the technicians job.
At MCP Consulting Group, we provide tailored consultancy services to help businesses implement and sustain Autonomous Maintenance programmes, enhancing reliability, reducing downtime, and fostering a culture of continuous improvement.
TPM, AM and OAC SUB-CATEGORIES
What is
Autonomous Maintenance
Autonomous Maintenance (AM) is a structured operator-driven maintenance approach where frontline staff take responsibility for basic equipment upkeep, such as cleaning, lubrication, and visual inspections. This strategy helps to identify and prevent early-stage failures, ensuring that equipment remains in peak condition and reducing the reliance on reactive maintenance.
By integrating Autonomous Maintenance into daily operations, businesses can increase asset uptime, enhance workforce engagement, and improve overall productivity. At MCP, we support organisations in developing AM frameworks, training employees, and embedding best practices into their maintenance culture.
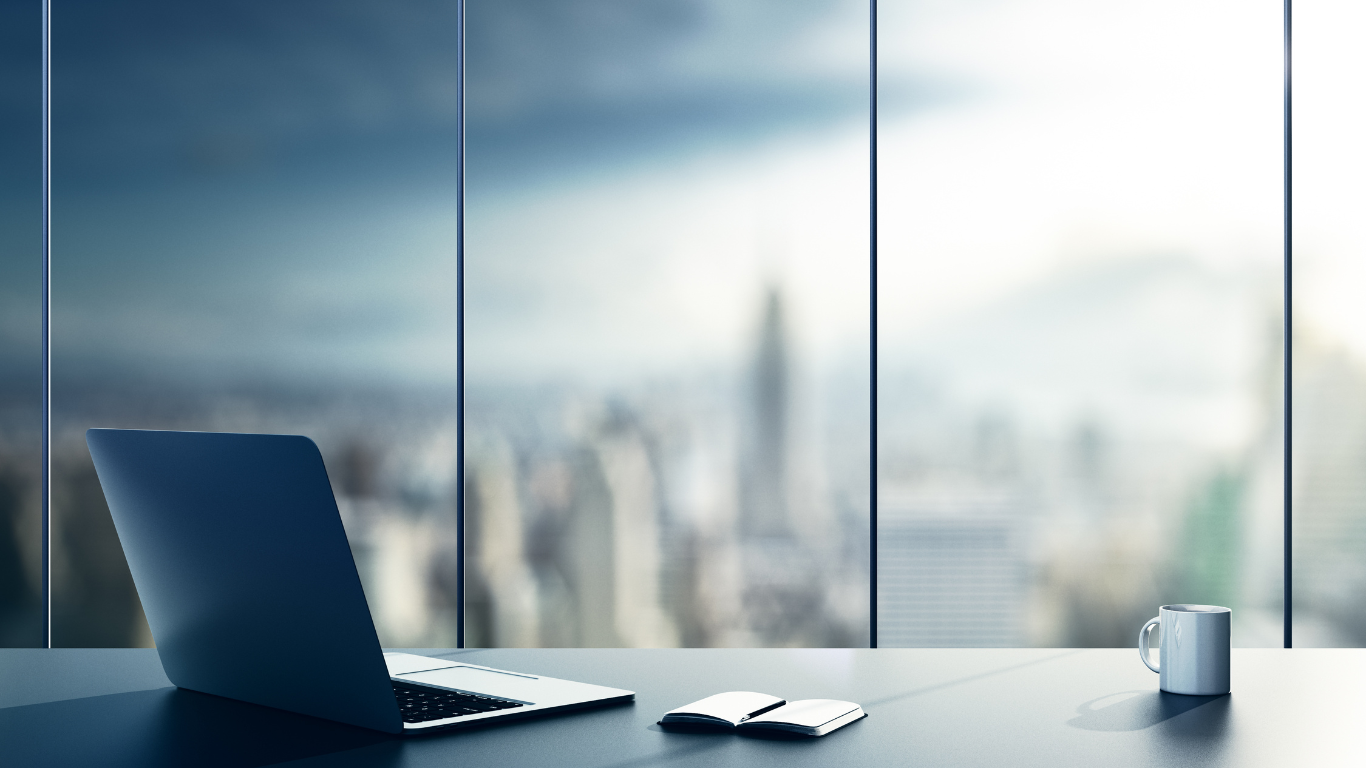
Key Objectives of
Autonomous Maintenance
Enable operators to identify and resolve minor issues before they escalate into failures.
1
Increasing Equipment Reliability
Reducing Downtime and Maintenance Costs
2
Minimise unplanned stoppages and emergency repairs through proactive operator-led maintenance.
Empowering Operators with Maintenance Responsibilities
3
Provide structured training and guidelines to help operators take ownership of routine maintenance tasks.
Driving Continuous Improvement
Improve communication between operators and maintenance personnel for faster issue resolution and greater efficiency.
4
Enhancing Collaboration Between Teams
5
Establish a culture of ongoing performance monitoring and process optimisation.
The
7 Steps of AM
Initial Cleaning – Operators perform thorough cleaning and inspections to identify potential failure points.
1
Eliminating Sources of Contamination – Reduce wear and tear by removing dirt, dust, and contaminants that affect machine performance.
2
Setting Standards for Cleaning & Lubrication – Define structured cleaning, lubrication, and inspection schedules.
3
General Inspections – Train operators to detect minor defects and early warning signs of failure.
4
Autonomous Inspection – Operators perform basic equipment inspections, reducing the workload on maintenance teams.
5
Standardisation – Establish repeatable maintenance routines to sustain Autonomous Maintenance practices.
6
Sustained Autonomous Maintenance – Integrate AM into daily operations, monitoring performance and driving continuous improvement.
7
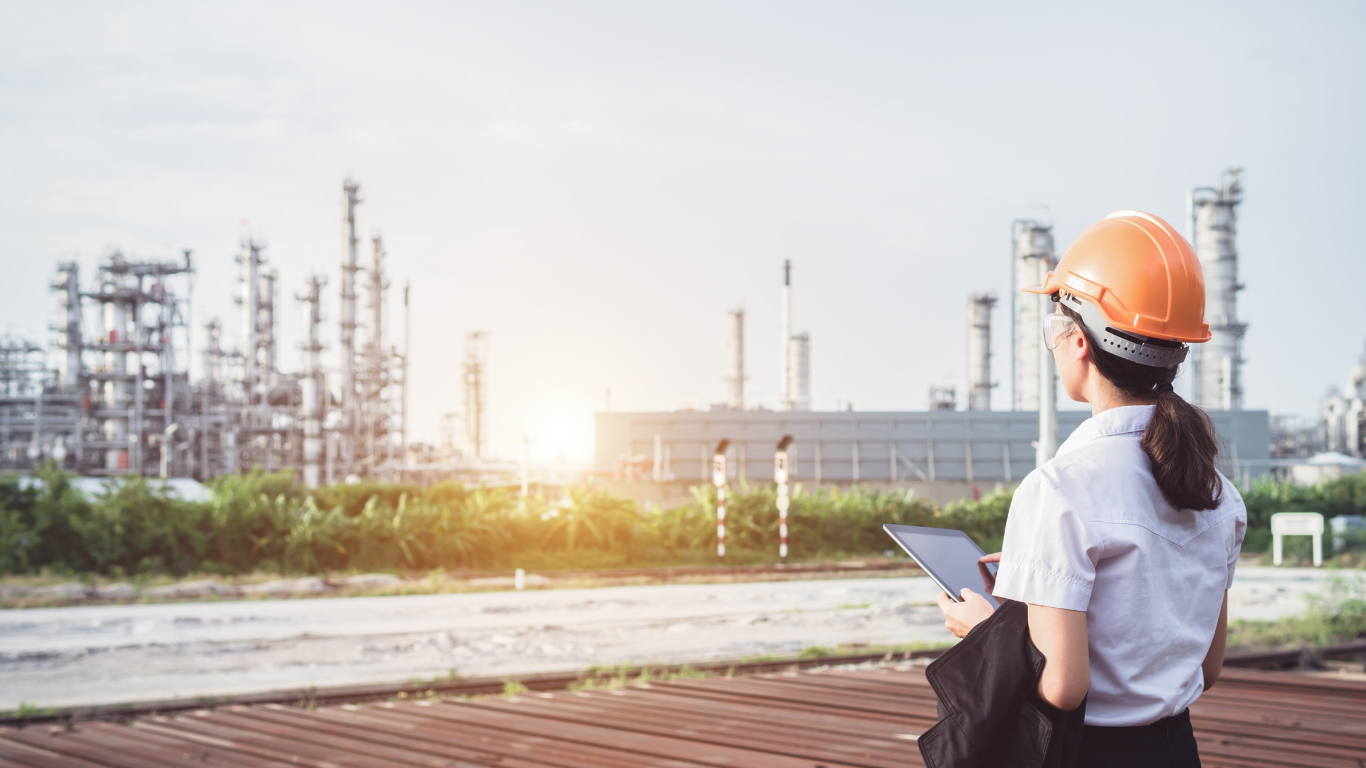
MCP Approach to
Autonomous Maintenance
Assessing Readiness and AM Implementation Strategy
MCP evaluates current maintenance processes, workforce skills, and organisational culture to determine AM readiness and implementation plans.
Developing a Customised AM Framework
We define AM objectives, structured workflows, and key performance indicators (KPIs) to align with business goals.
Training and Operator Engagement
Our consultants provide on-the-job training and coaching to equip operators with the skills and knowledge required to sustain AM initiatives.
Establishing AM Workflows and Responsibilities
We assist organisations in defining clear roles, maintenance tasks, and accountability structures to ensure seamless AM execution.
Continuous Improvement and Performance Monitoring
MCP supports ongoing AM reviews, KPI tracking, and refinement of Autonomous Maintenance processes for long-term success.
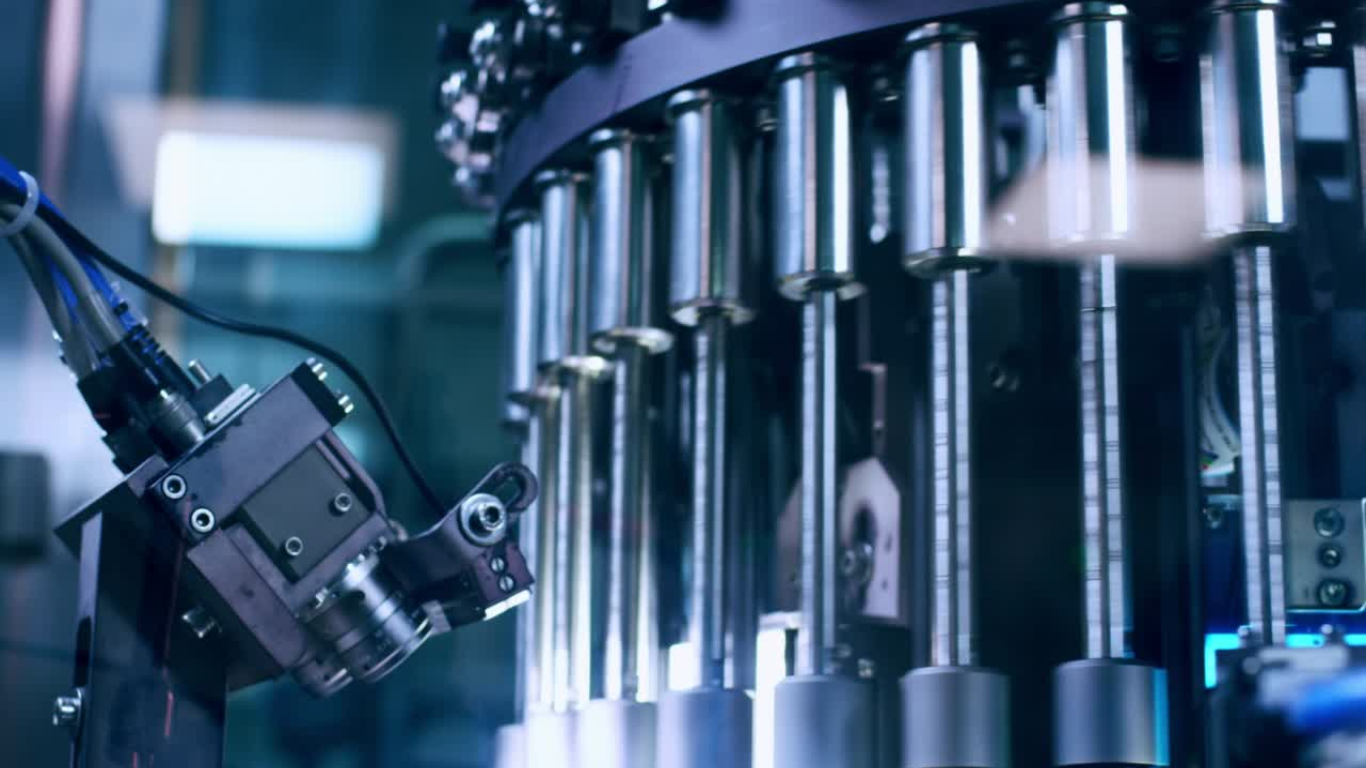
TPM, AM and OAC
Explore More
Speak to One of Our
Experienced Consultants
If you have any questions or would like to learn more about how MCP can support your organisation with Autonomous Maintenance, please get in touch with us.
Our team of consultants is ready to provide tailored solutions to optimise maintenance strategies, empower operators, and improve equipment reliability. Contact us today to discuss your specific requirements.
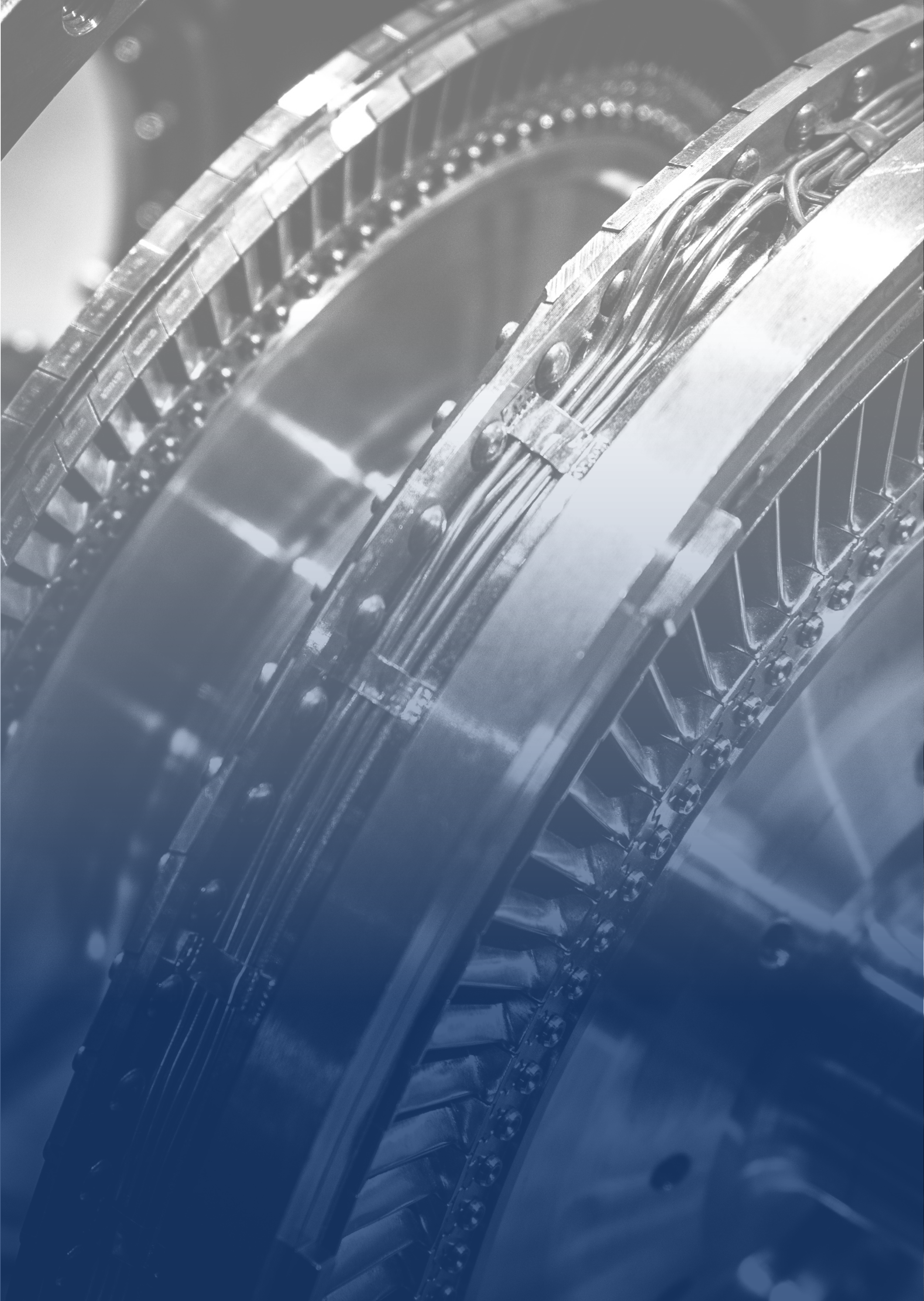
FAQs
-
AM increases equipment uptime, reduces failures, enhances operator skills, and fosters a culture of continuous improvement.
-
No, AM complements planned maintenance strategies by focusing on operator-driven tasks while technicians handle more complex/skilled maintenance activities.
-
The timeframe varies based on business size, workforce readiness, and existing maintenance culture, but implementation typically takes several months.
-
Manufacturing, food processing, energy, automotive, and pharmaceutical industries benefit significantly from AM due to high equipment utilisation demands.
-
By reducing minor stoppages, improving asset condition, and preventing early-stage failures, AM enhances OEE and production efficiency.