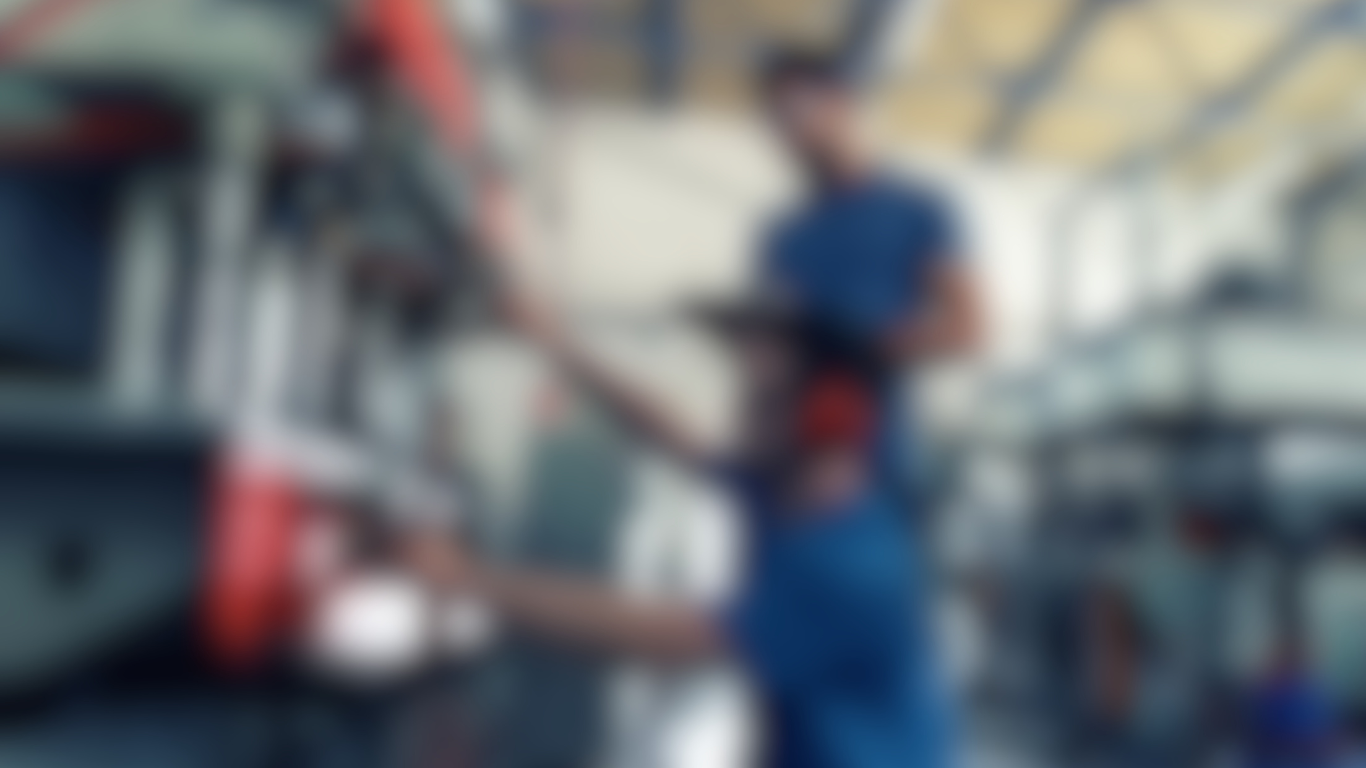
Root Cause Analysis Support
Root Cause Analysis (RCA) is a systematic approach to identifying the underlying causes of asset failures and operational inefficiencies. At MCP Consulting Group, we provide reliability experts to help organisations implement RCA methodologies that drive continuous improvement, reduce recurring issues, and enhance overall reliability.
RELIABILITY MANAGEMENT CATEGORIES
What is
Root Cause Analysis
Root Cause Analysis is a structured investigative process that determines the fundamental reasons behind failures or problems. By addressing the root cause rather than just symptoms, organisations can prevent repeat failures, improve maintenance strategies, and optimise asset performance.
At MCP, we support businesses in adopting RCA techniques to enhance decision-making, increase asset uptime, and reduce maintenance costs.
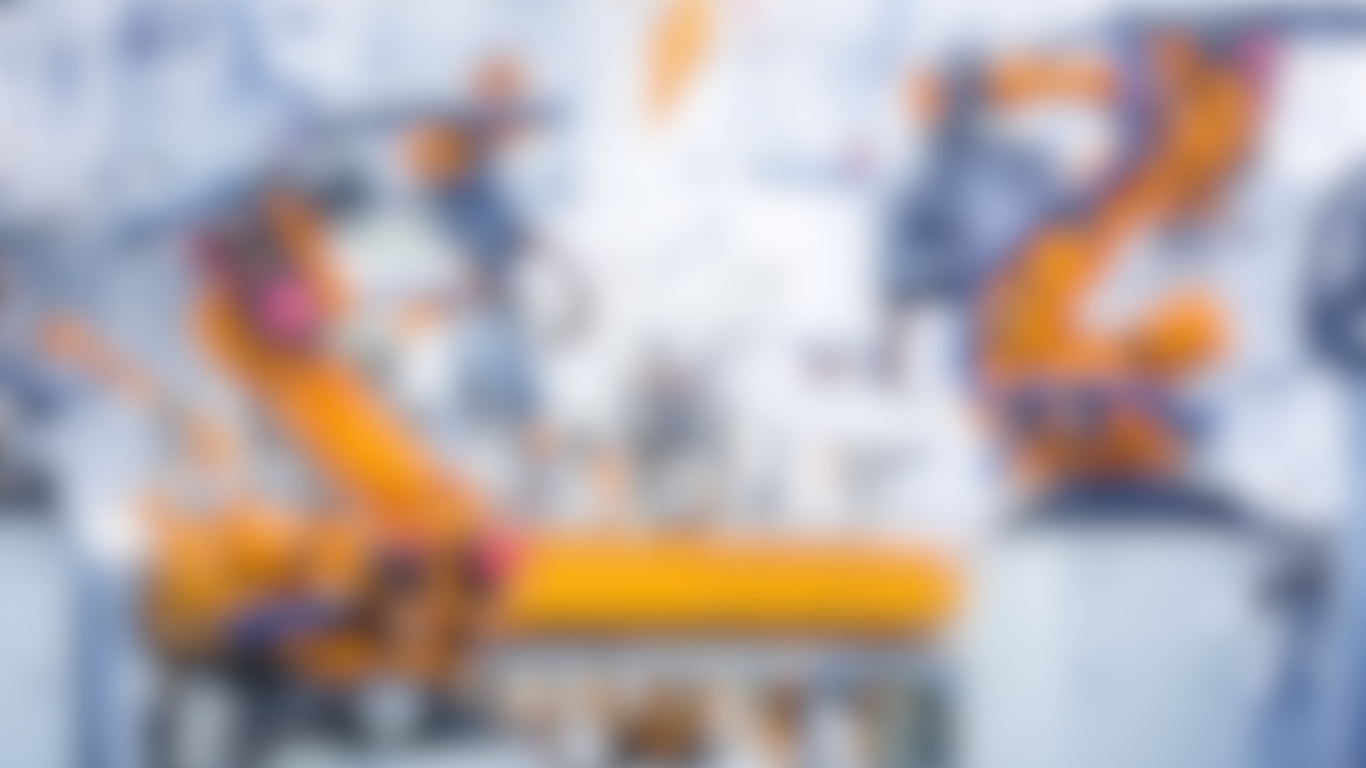
Key Objectives of
Root Cause Analysis
1
Identifying Systemic Issues
Discover underlying problems that contribute to asset failures and operational inefficiencies.
2
Preventing Recurring Failures
Implement corrective actions to eliminate repeat breakdowns and improve asset longevity.
Use data-driven insights to refine maintenance plans and optimise resource allocation.
3
Enhancing Maintenance Strategies
4
Reducing Costs and Downtime
Minimise unnecessary maintenance and unplanned shutdowns by resolving fundamental failure causes.
5
Improving Safety and Compliance
Address safety risks and ensure compliance with industry regulations by mitigating root causes of failures.
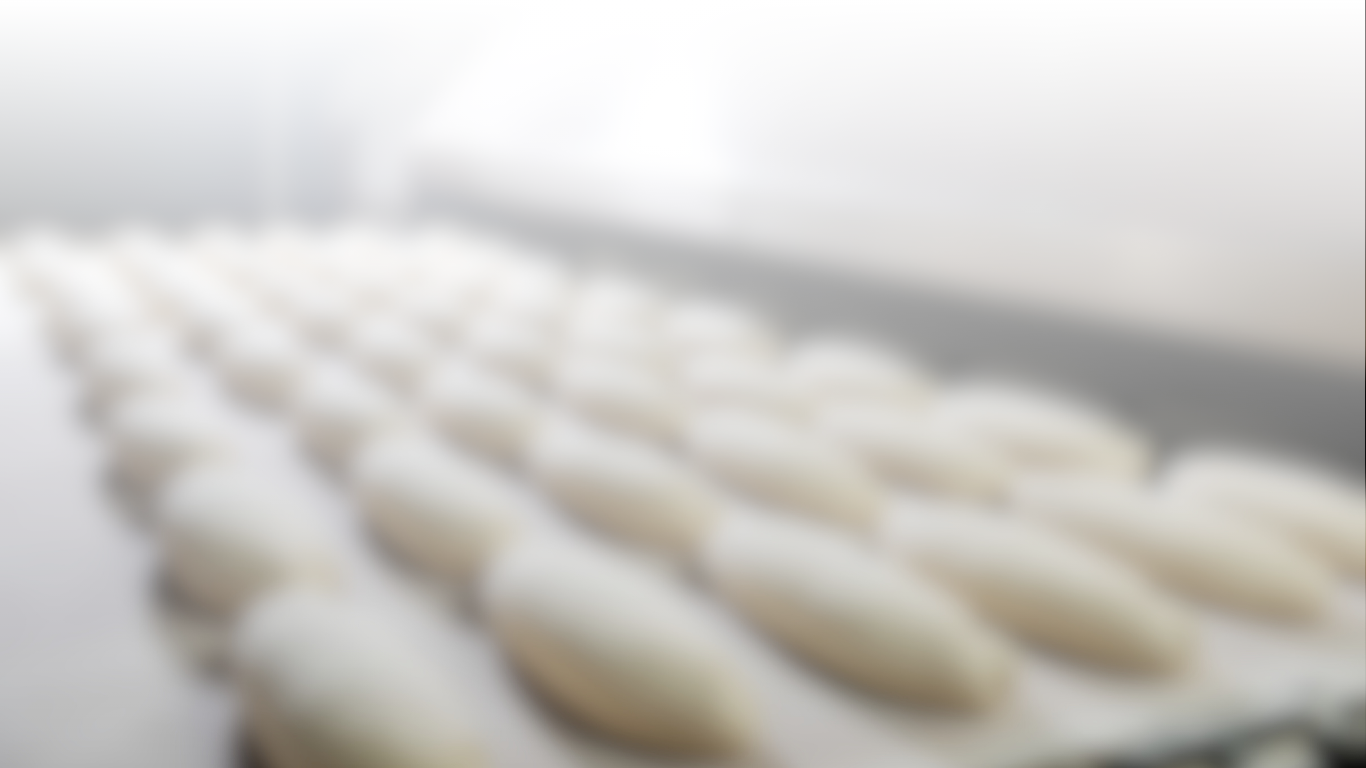
MCP Approach to
Root Cause Analysis
MCP helps businesses integrate RCA into their continuous improvement processes, ensuring that maintenance adjustments are tracked, measured, and refined for maximum impact.
Continuous Improvement & Monitoring
MCP works with organisations to conduct structured failure investigations, using historical data and real-time asset insights to identify underlying causes of operational issues and recommend courses of action.MCP works with organisations to conduct structured failure investigations, using historical data and real-time asset insights to identify underlying causes of operational issues and recommend courses of action.
Failure Investigation
We provide training and support in industry-standard RCA techniques such as 5 Whys, Fishbone Diagrams, and Fault Tree Analysis, enabling businesses to systematically diagnose root causes.
RCA Methodologies
Our experts assist in leveraging condition monitoring, predictive maintenance, and historical trends to pinpoint the true source of asset failures and inefficiencies.
Data Collection & Analysis
We work alongside organisations to implement long-term solutions that address root causes, reduce repeat failures, and optimise maintenance strategies.
Corrective Action Planning
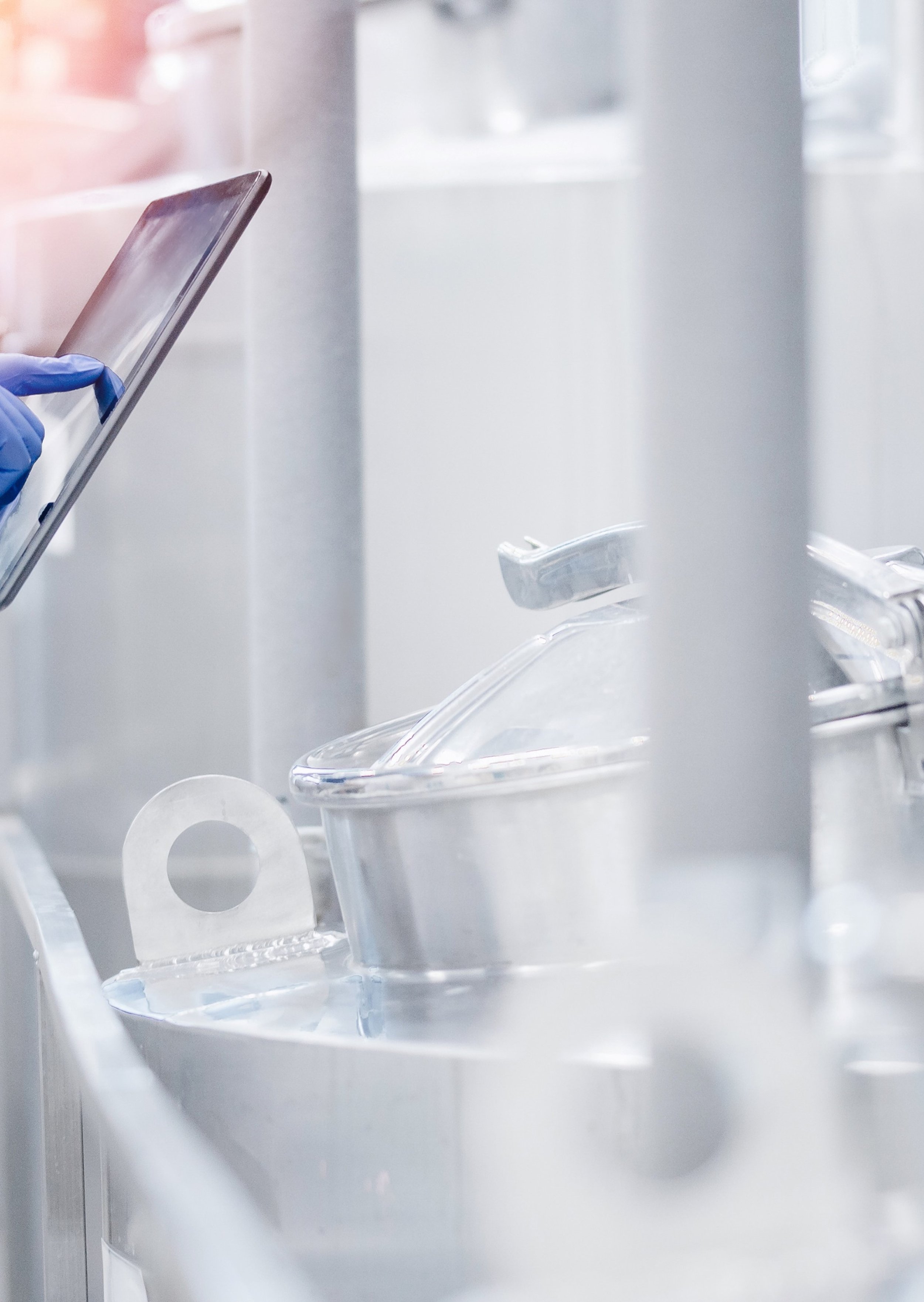
Reliability Management
Explore More
Speak to One of Our
Reliability Consultants
If you have any questions or would like to learn more about how MCP Consulting Group can support your organisation with Root Cause Analysis, please get in touch with us. Our team of consultants is ready to provide tailored solutions to enhance asset reliability and improve operational performance.
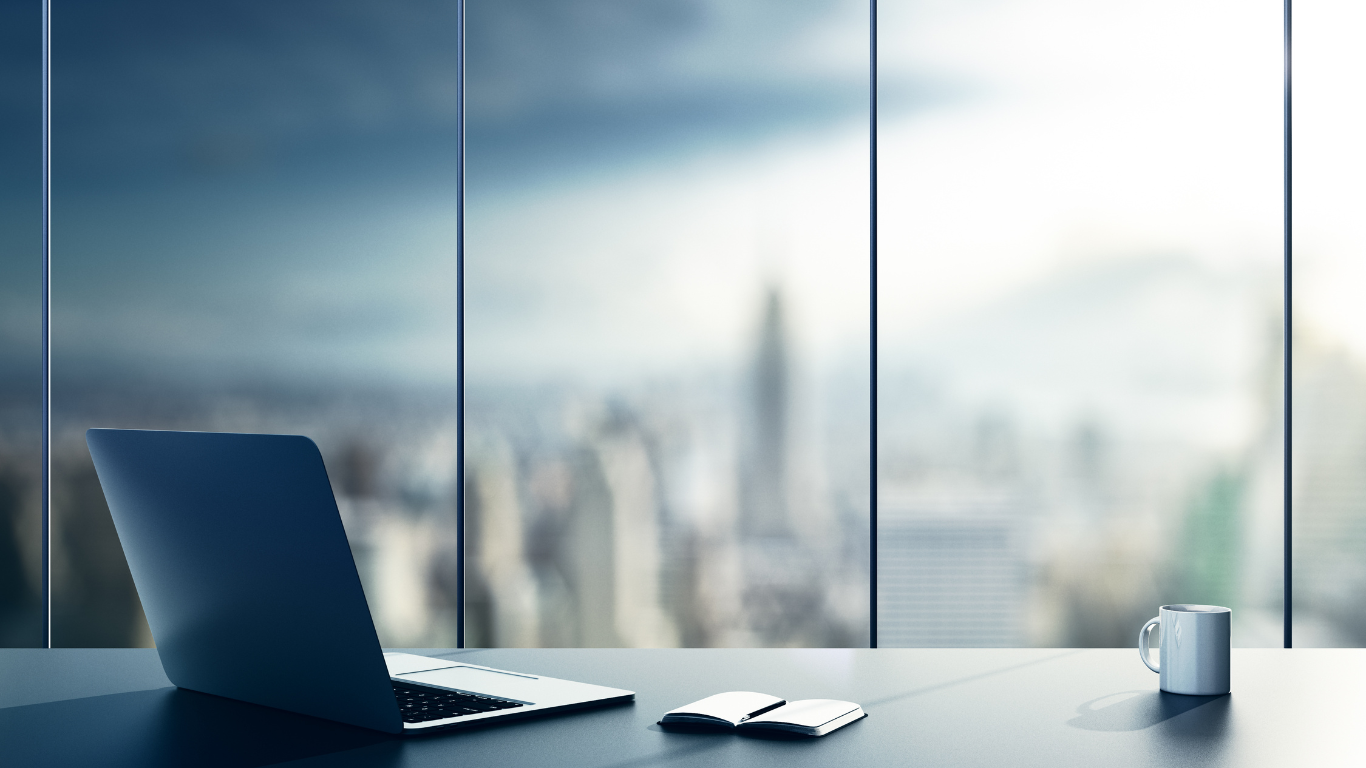
FAQs
-
RCA helps businesses identify and eliminate the fundamental causes of failures, preventing recurring issues and improving asset reliability.
-
Yes, the RCA process can be used to drill down and identify materials, process, maintenance or human error.
-
Popular methods include 5 Whys, Fishbone (Ishikawa) Diagrams, and Fault Tree Analysis, each of which provides a structured way to analyse failure causes.
-
RCA refines maintenance strategies by pinpointing true failure causes, allowing organisations to reduce reactive maintenance and optimise preventive measures.
-
RCA is essential for manufacturing, energy, transportation, healthcare, and other asset-intensive industries, where failure prevention is critical to operations.
-
RCA complements predictive maintenance by identifying failure trends and enabling proactive interventions before breakdowns occur.