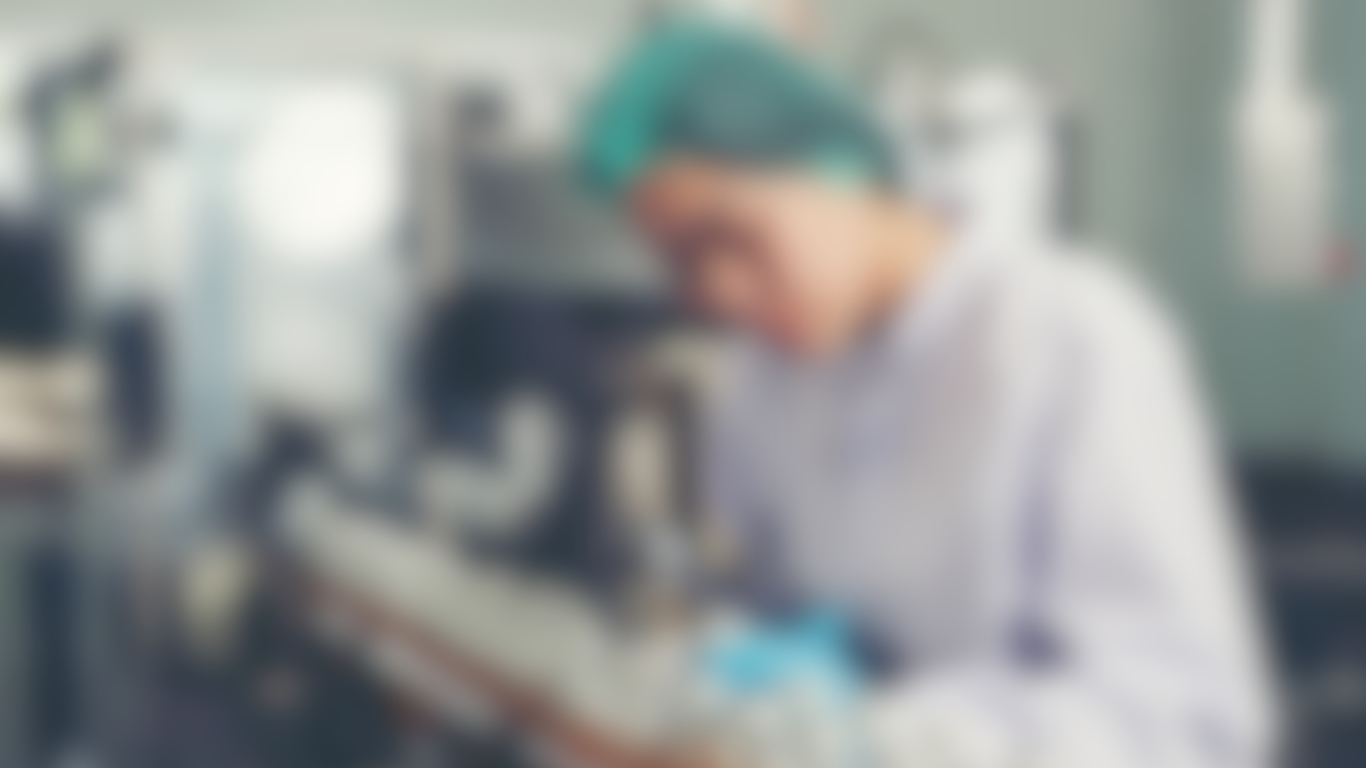
Predictive Maintenance (IIoT) Support
Predictive maintenance powered by Industrial Internet of Things (IIoT) technologies is transforming asset management by enabling real-time monitoring, advanced analytics, and AI-driven decision-making. At MCP Consulting Group, we provide consultancy services to help businesses implement predictive maintenance strategies that reduce downtime, optimise maintenance schedules, and improve asset performance.
RELIABILITY MANAGEMENT CATEGORIES
What is
Predictive Maintenance (IIoT)
Predictive Maintenance (PdM) uses IIoT sensors, machine learning algorithms, and data analytics to anticipate asset failures before they occur. By continuously monitoring equipment conditions and analysing performance trends, organisations can move from reactive and preventive maintenance to a truly predictive approach that minimises disruptions and maximises efficiency.
At MCP, we support organisations in selecting, integrating, and optimising predictive maintenance technologies to enhance their maintenance management frameworks.
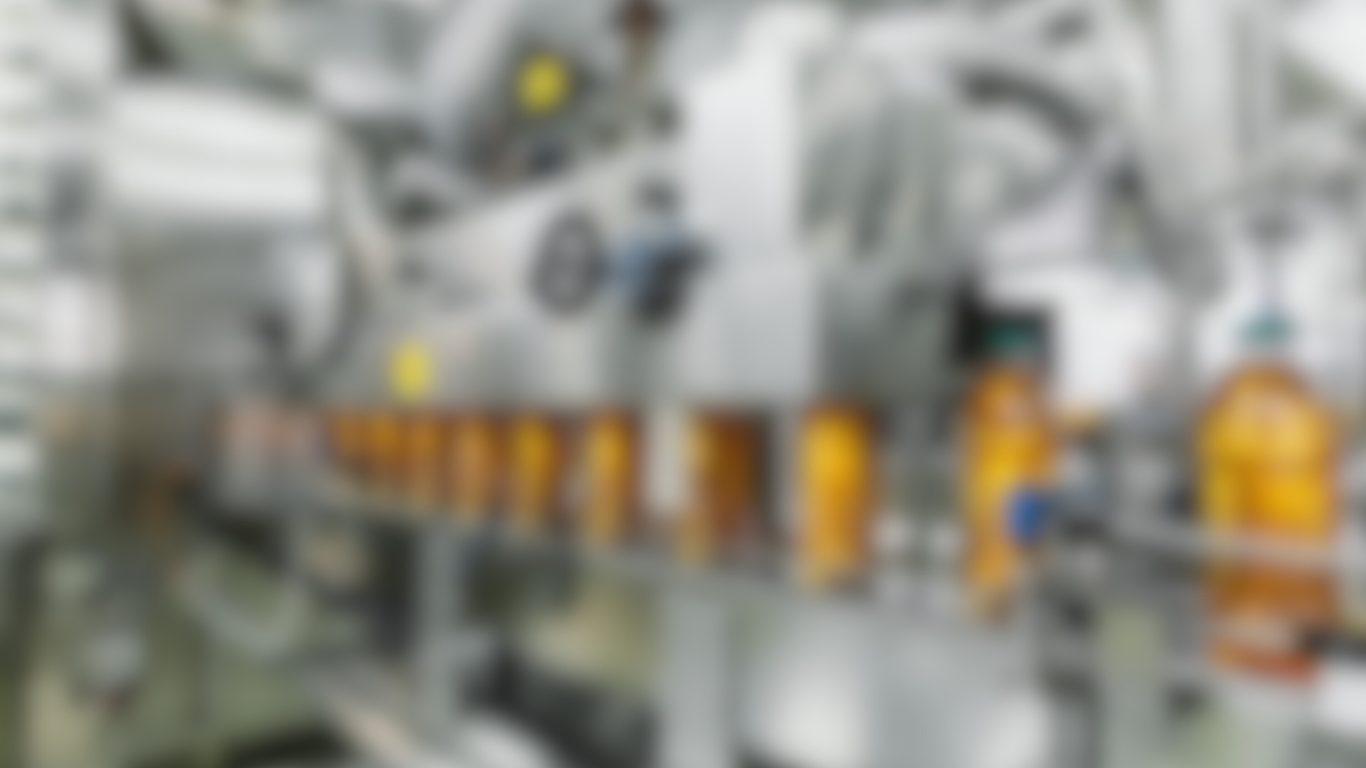
Key Objectives of
Predictive Maintenance (IIoT)
1
Real-Time Asset Monitoring
Use IIoT sensors to collect continuous data on critical asset parameters such as vibration, temperature, and pressure.
2
Early Fault Detection
Leverage AI-driven analytics to detect anomalies and predict potential failures before they escalate.
Move from calendar-based maintenance to condition-based scheduling, reducing unnecessary interventions.
3
Optimising Maintenance Intervals
4
Reducing Unplanned Downtime
Prevent costly breakdowns by identifying and addressing issues before they lead to failures.
5
Enhancing Operational Efficiency
Improve productivity by ensuring assets operate at peak performance with minimal disruption.
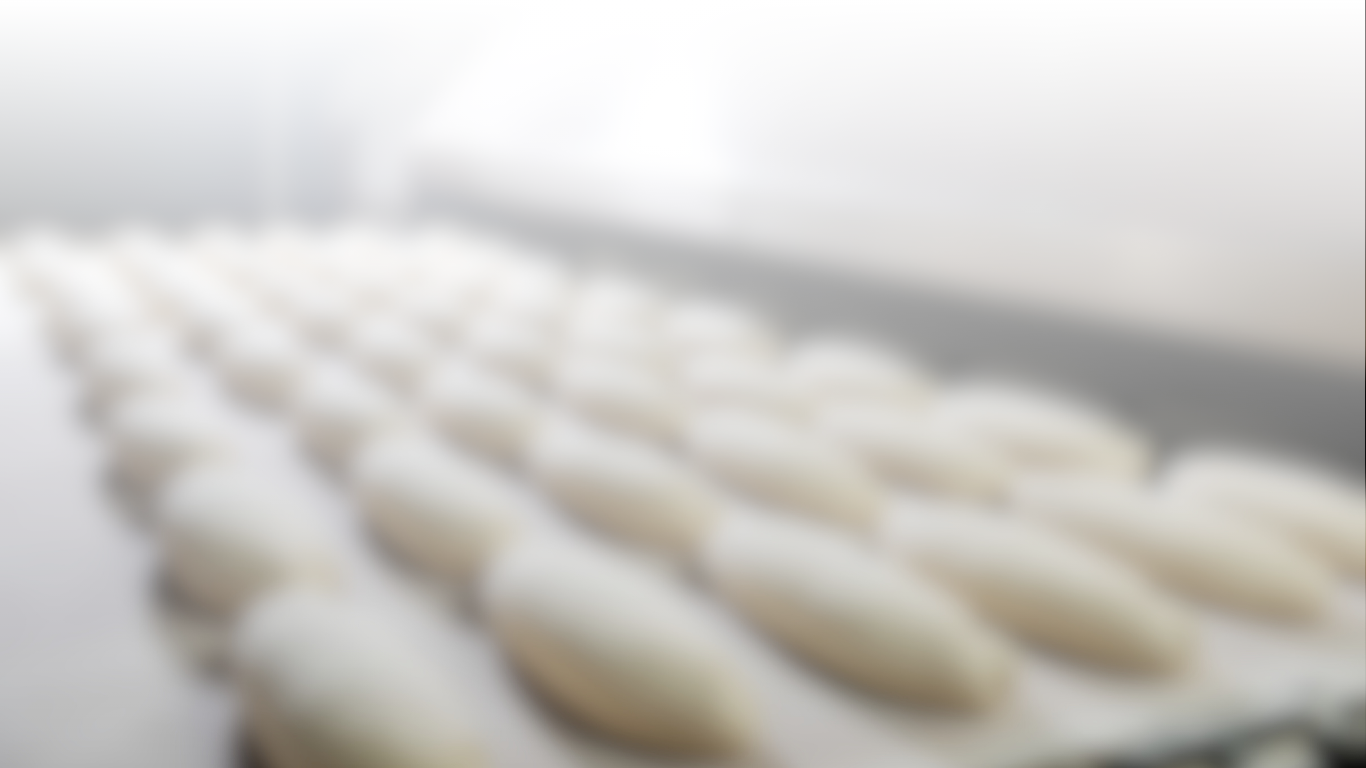
MCP Approach to
Predictive Maintenance (IIoT)
Continuous Improvement
We help businesses develop structured performance tracking and return-on-investment (ROI) measurement frameworks to refine predictive maintenance strategies and maximise long-term benefits.
MCP helps organisations identify and install the most suitable IIoT sensors for real-time asset monitoring. We ensure that businesses deploy the right technology to capture critical performance data and detect early signs of failure.
IIoT Sensor Deployment
We support businesses in leveraging cloud-based platforms and AI-driven tools to collect, analyse, and interpret asset data. Our approach enables organisations to transform raw data into actionable insights for predictive decision-making.
Data Integration & Analytics
Predictive Modelling & Alerts
Our consultants assist in implementing automated failure prediction models that use machine learning and historical trends to detect anomalies and trigger real-time alerts. This allows for proactive maintenance interventions before failures occur.
MCP works alongside organisations to integrate predictive maintenance insights with Computerised Maintenance Management Systems (CMMS) and Enterprise Asset Management (EAM) platforms, ensuring a seamless connection between predictive analytics and maintenance workflows.
CMMS/EAM Integration
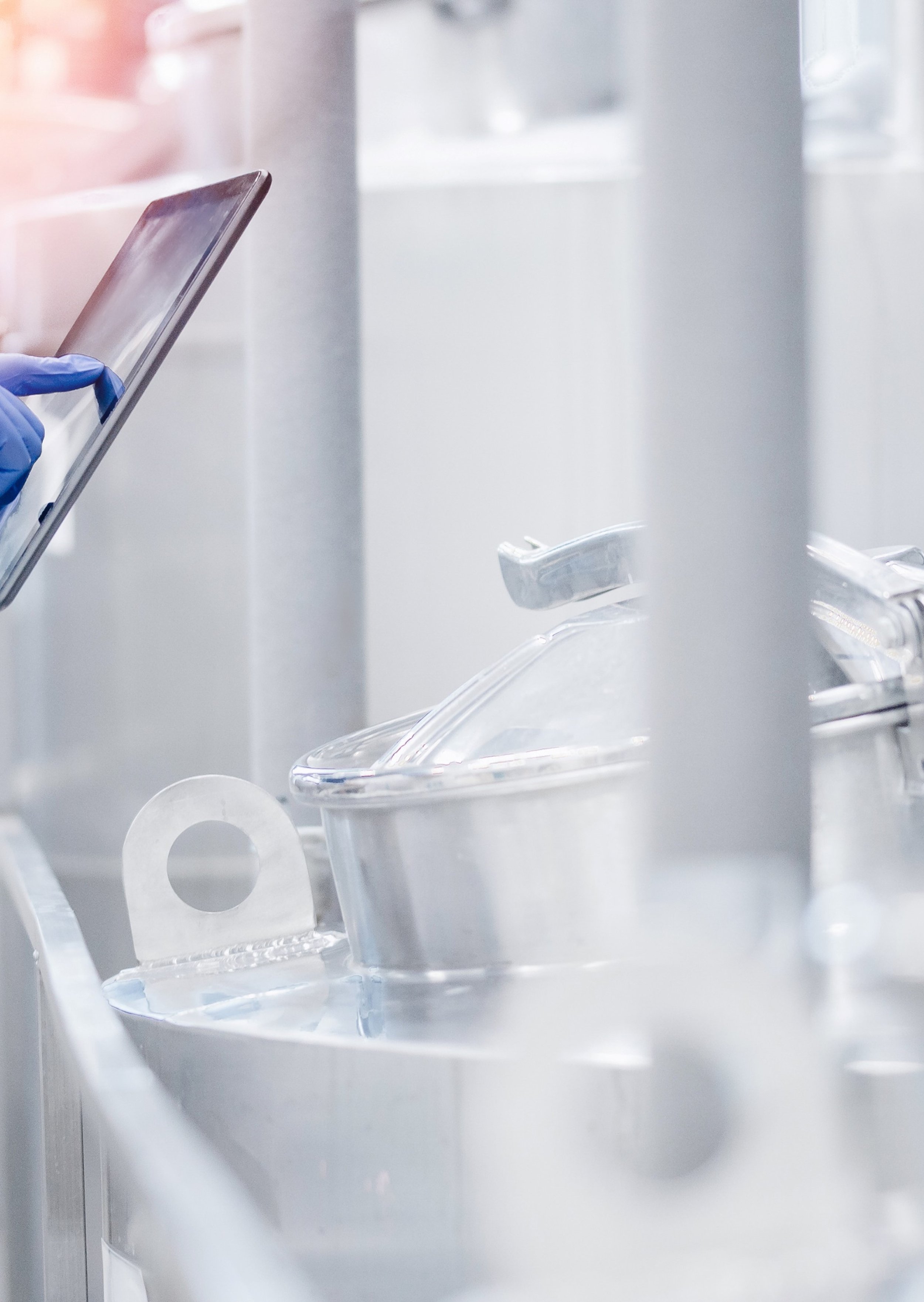
Reliability Management
Explore More
Speak to One of Our
Reliability Consultants
If you have any questions or would like to learn more about how MCP Consulting Group can support your organisation with Predictive Maintenance (IIoT), please get in touch with us. Our team of consultants is ready to provide tailored solutions to enhance asset reliability and improve operational performance.
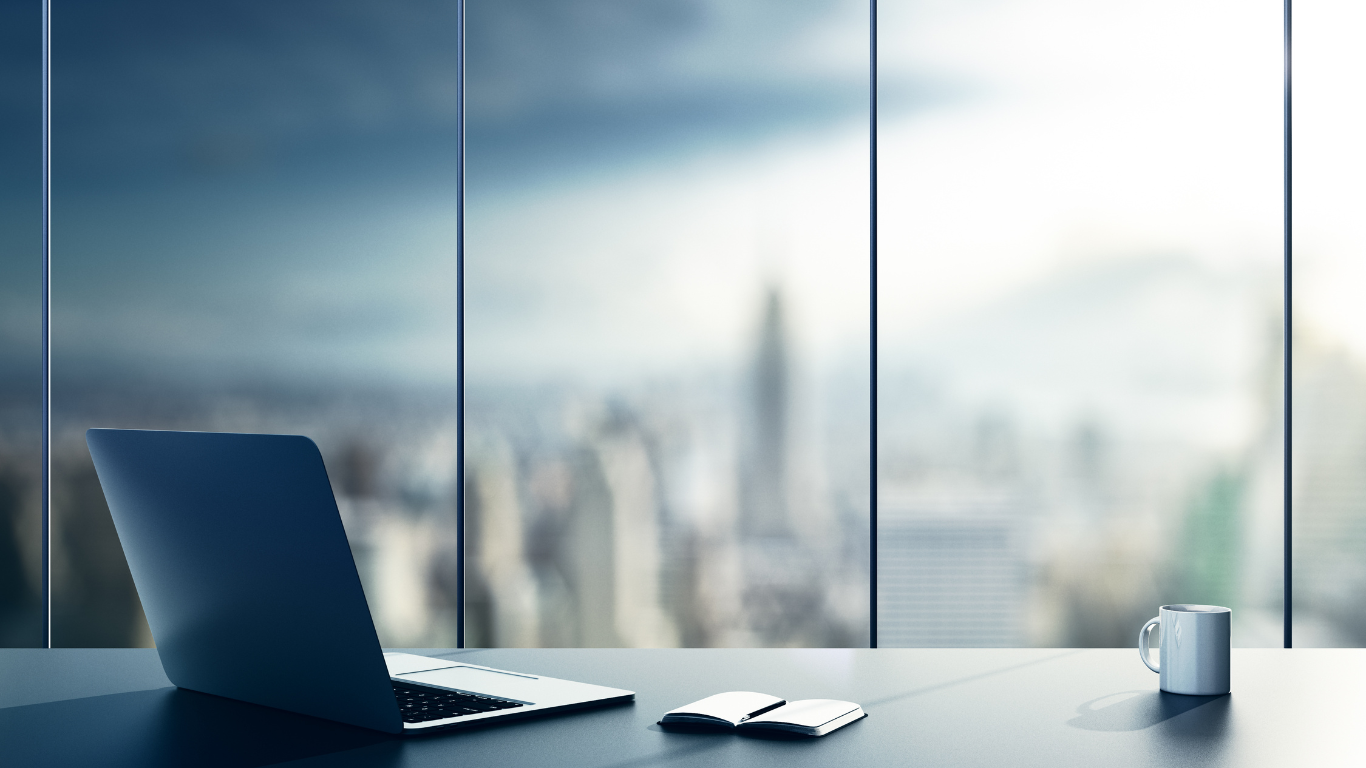
FAQs
-
Predictive Maintenance allows organisations to anticipate failures before they happen, reducing unplanned downtime and optimising maintenance schedules.
-
Condition Monitoring involves real-time tracking of asset health, while Predictive Maintenance uses AI and analytics to forecast future failures based on historical trends and sensor data.
-
Industries such as manufacturing, energy, utilities, transportation, and healthcare benefit from Predictive Maintenance due to its ability to reduce failures and increase efficiency.
-
Predictive Maintenance data can be automatically fed into CMMS/EAM systems, allowing maintenance teams to schedule interventions proactively rather than reactively.
-
Common sensors include vibration sensors, infrared thermography, ultrasound detectors, and oil analysis tools, all of which monitor asset health indicators.