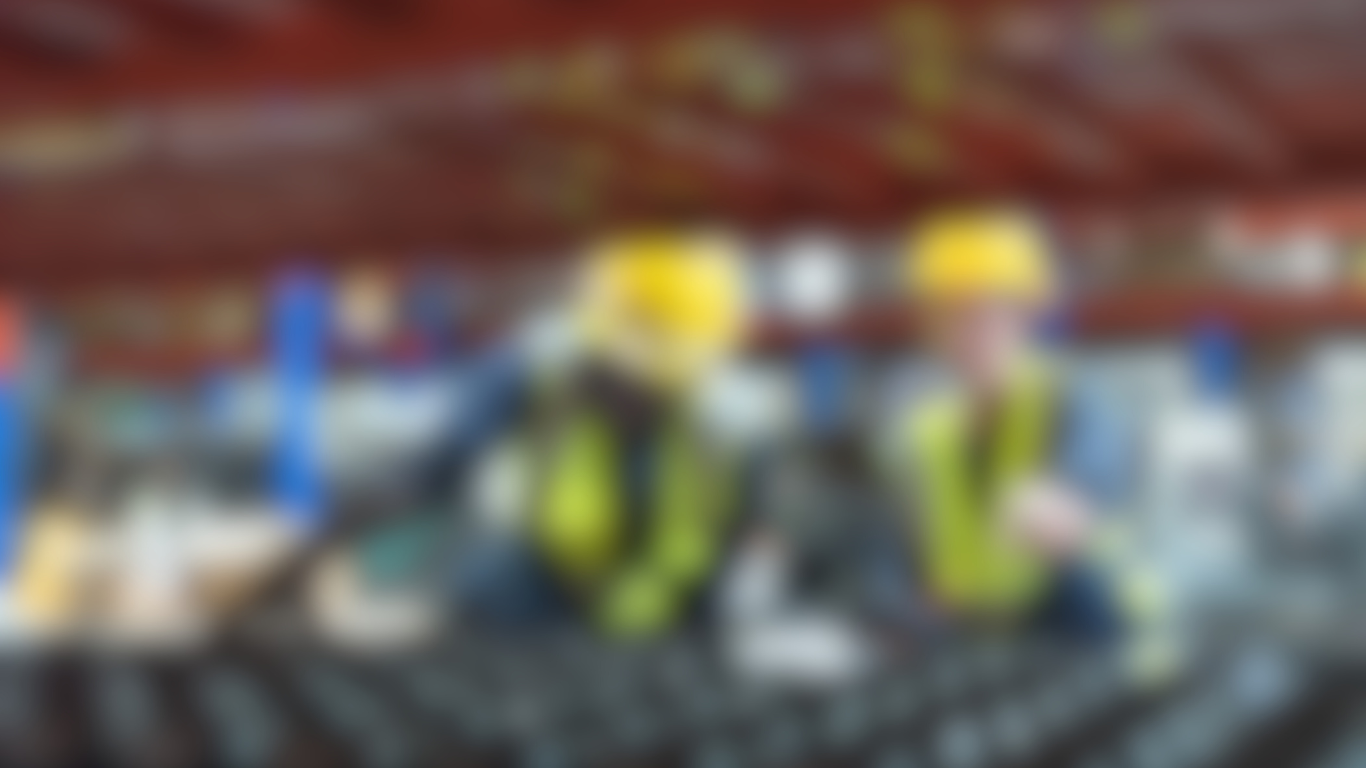
Spares Outsourcing
Managing spare parts inventory can be complex and resource-intensive, requiring significant investment in procurement, storage, and logistics. At MCP Consulting Group, we provide consultancy services to help organisations explore Spares Outsourcing, ensuring cost-effective spare parts availability while reducing stockholding risks and operational inefficiencies.
MRO SPARES MANAGEMENT CATEGORIES
What is
Spares Outsourcing
Spares Outsourcing is the process of partnering with third-party suppliers, vendors, or inventory management services to handle spare parts procurement, storage, and distribution. By outsourcing spare parts management, organisations can reduce inventory holding costs, streamline procurement, and improve asset reliability without the burden of maintaining extensive stock.
At MCP, we support businesses in evaluating, selecting, and implementing outsourcing strategies to enhance spare parts availability while improving cost efficiency and operational performance.
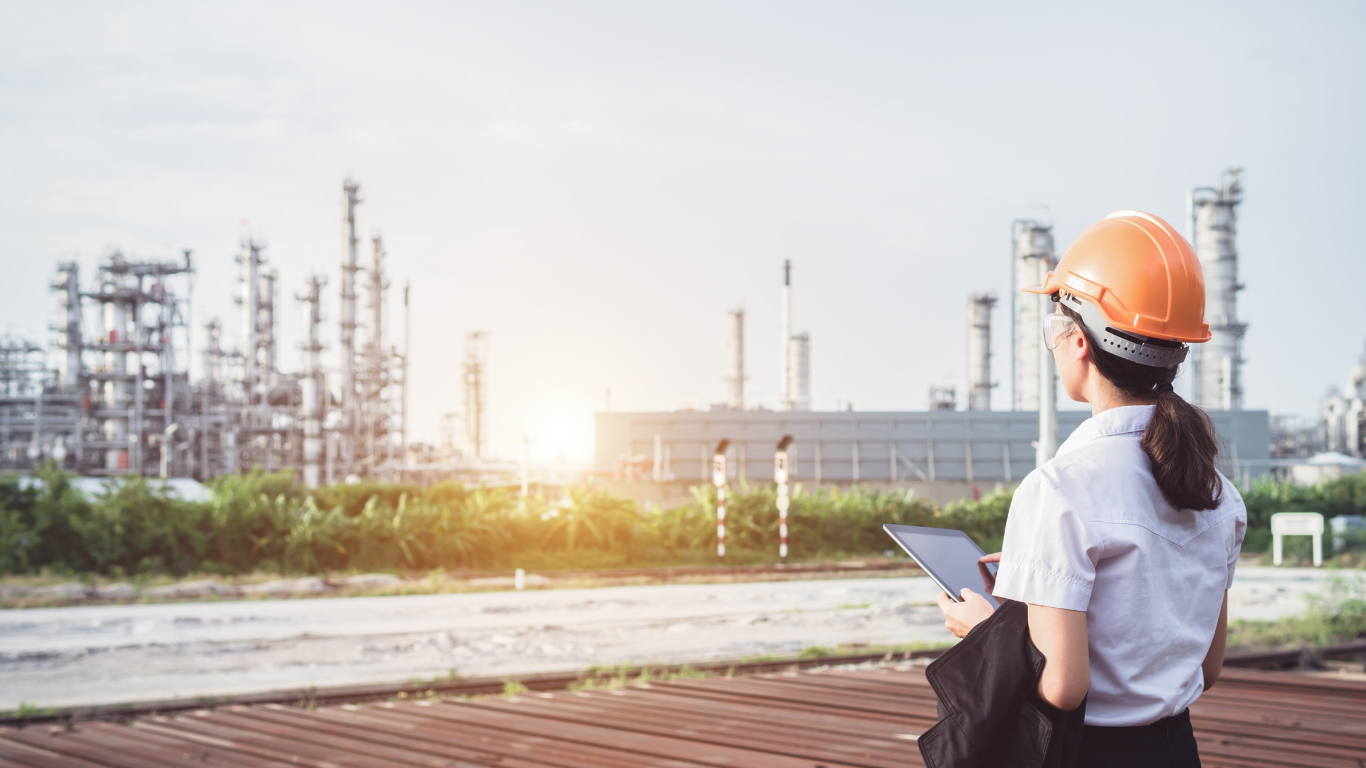
Key Objectives of
Spares Outsourcing
1
Reducing Inventory Holding Costs
Minimise capital tied up in spare parts stock while ensuring essential spares are available when needed.
2
Enhancing Spare Parts Availability
Work with reliable outsourcing partners to ensure just-in-time (JIT) delivery and reduce supply chain disruptions.
3
Improving Procurement Efficiency
Streamline sourcing processes and leverage supplier networks to access cost-effective spare parts solutions.
4
Mitigating Supply Chain Risks
Reduce dependency on internal stockholding and enhance resilience against supply chain disruptions.
5
Optimising Maintenance and Asset Performance
Ensure maintenance teams have timely access to critical spare parts, reducing downtime and improving operational efficiency.
6
Aligning Spares Management with Business Strategy
Develop long-term outsourcing partnerships that align with business goals, maintenance strategies, and cost-saving initiatives.
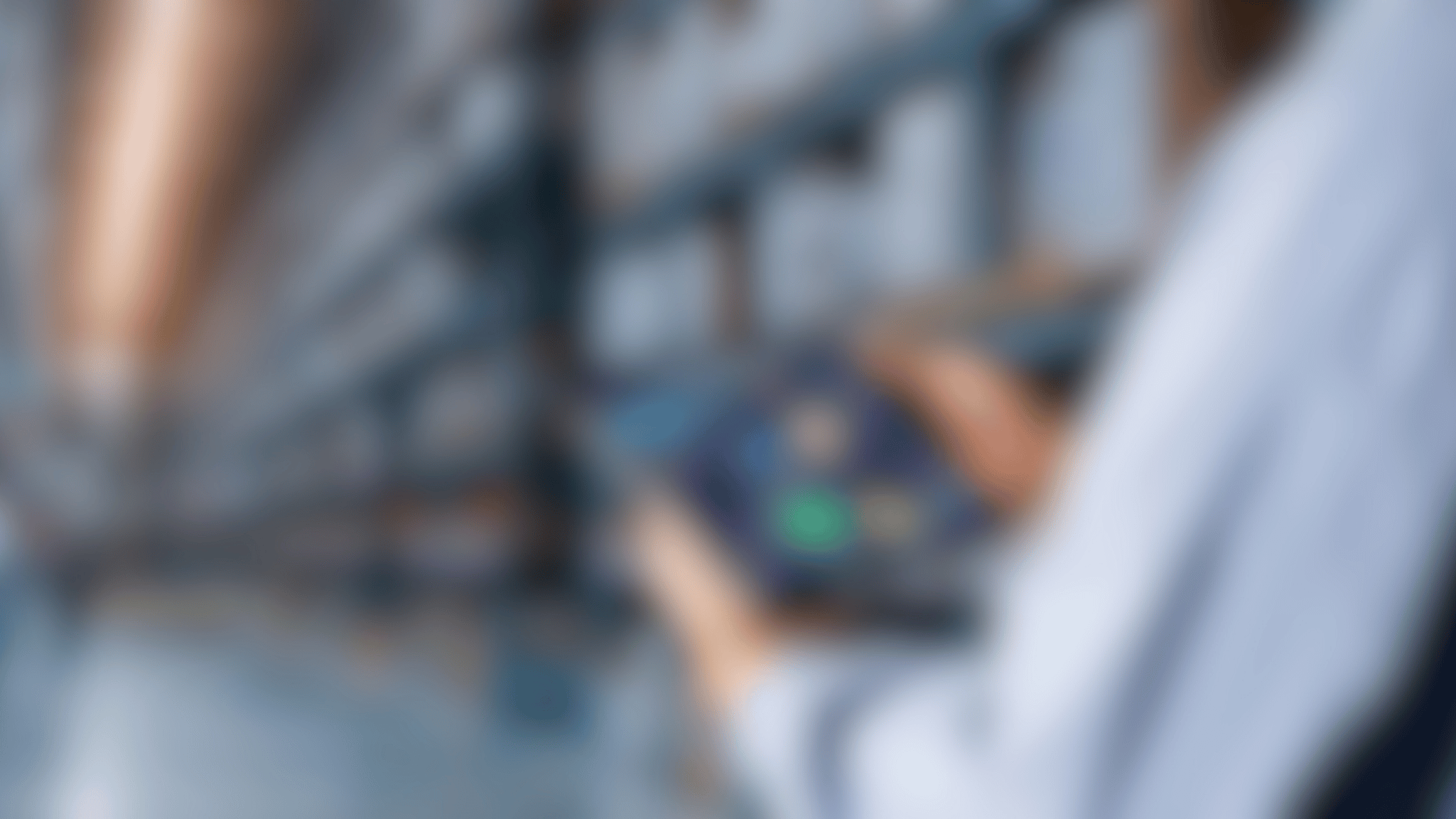
MCP Approach to
Spares Outsourcing
MCP works with organisations to assess the suitability of spares outsourcing, considering inventory needs, operational risks, and cost implications.
Outsourcing Feasibility Assessment
We support businesses in identifying and evaluating third-party suppliers, ensuring reliable and cost-effective spare parts outsourcing solutions.
Vendor Selection and Partnership Development
Our consultants assist in developing clear outsourcing agreements, defining performance expectations, delivery timelines, and cost structures.
Contract Negotiation and Service Level Agreements (SLAs)
We help businesses develop contingency plans to ensure spare parts availability, minimising risks associated with outsourcing.
Supply Chain and Risk Management
MCP supports CMMS/EAM integration, ensuring that outsourced spare parts are tracked, monitored, and available when required.
Integration with Maintenance Management Systems
We help organisations establish KPIs and review mechanisms to assess vendor performance and refine outsourcing strategies over time.
Continuous Performance Monitoring & Optimisation
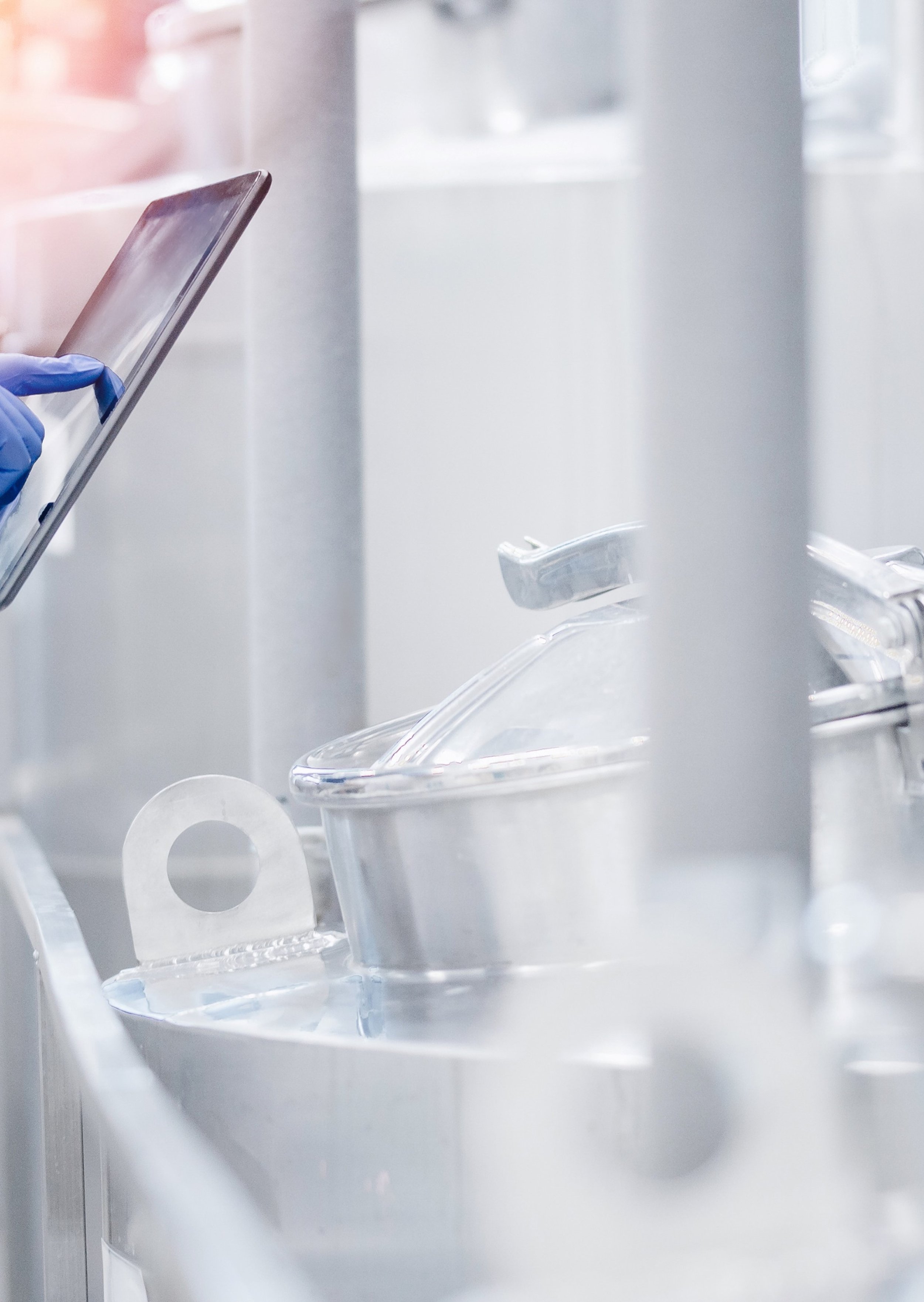
Spares Management
Explore More
Speak to One of Our
Spares Management Consultants
If you have any questions or would like to learn more about how MCP Consulting Group can support your organisation with Spares Outsourcing, please get in touch with us.
Our team of consultants is ready to provide tailored solutions to reduce inventory costs, improve spare parts availability, and enhance operational efficiency.
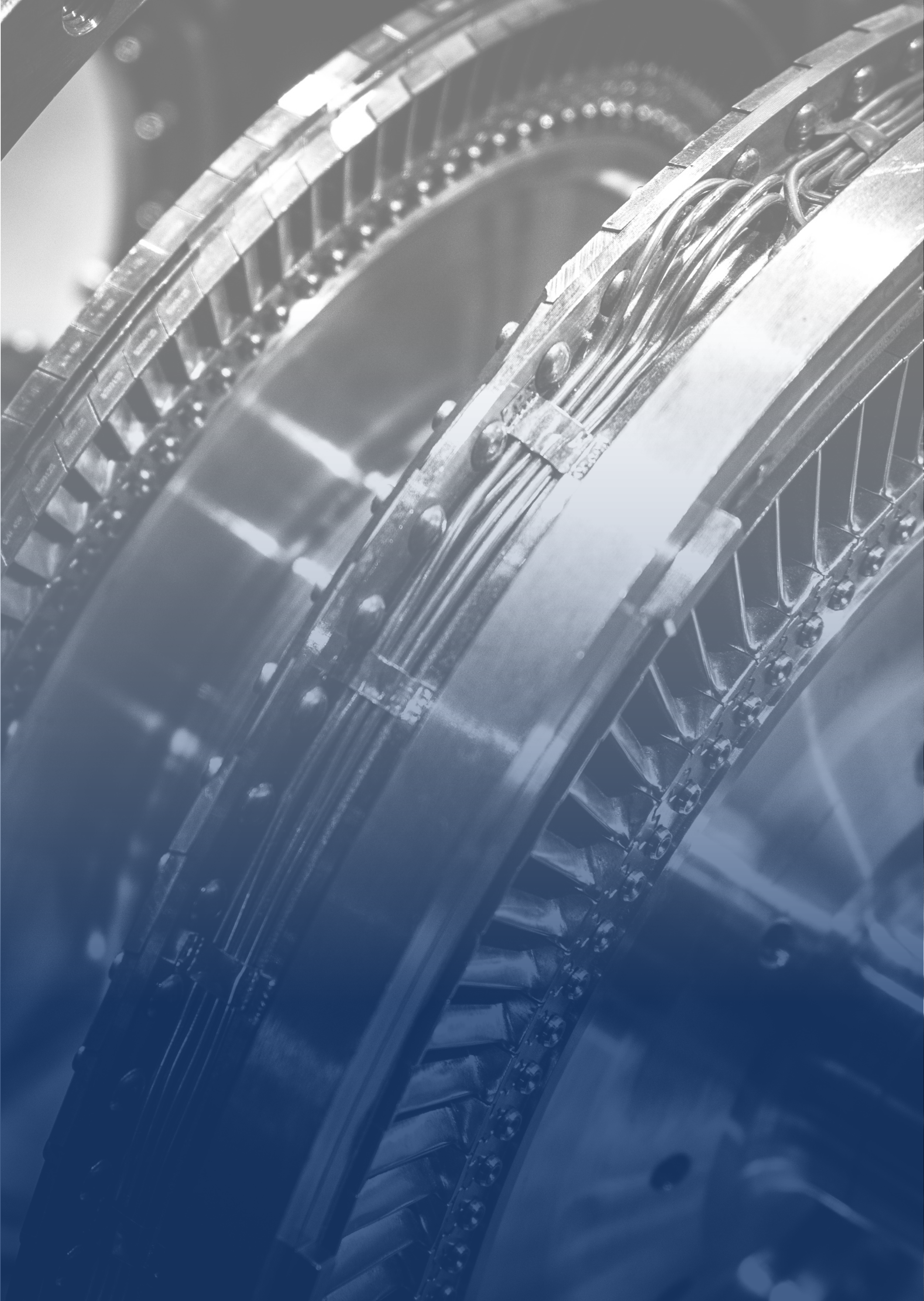
FAQs
-
Spares outsourcing reduces stockholding costs, improves spare parts availability, and enhances procurement efficiency by leveraging supplier expertise.
-
By ensuring timely spare parts delivery, outsourcing helps reduce downtime, improve asset performance, and support proactive maintenance planning.
-
Manufacturing, energy, utilities, transportation, and healthcare industries benefit from outsourcing as it reduces inventory costs and ensures critical parts availability.
-
Organisations should establish clear SLAs, conduct vendor assessments, and implement performance monitoring to ensure reliable outsourcing partnerships.
-
Risks include supplier reliability, lead time delays, and potential loss of inventory control, which can be mitigated through strong contracts and supplier performance tracking.