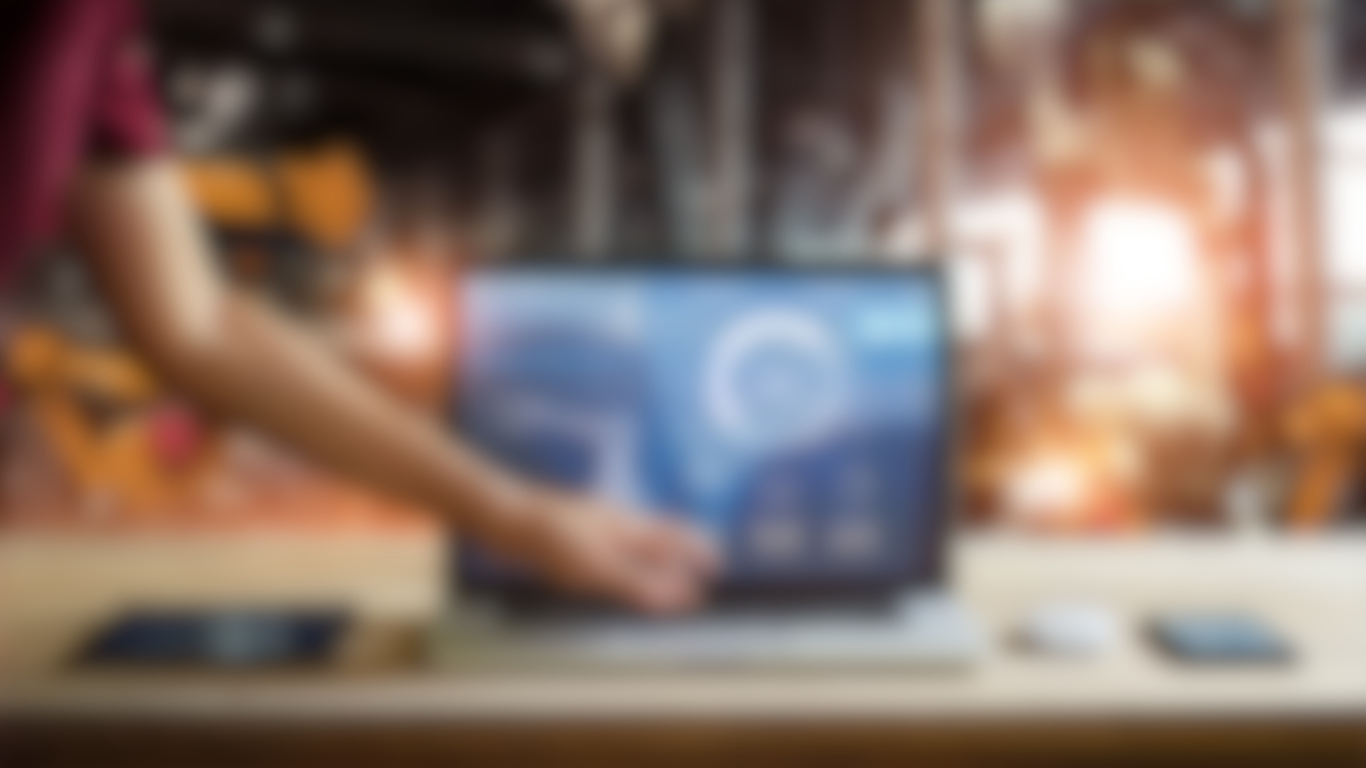
Spares Assessment
Effective spare parts management is crucial for maintaining operational efficiency, reducing downtime, and controlling inventory costs. Without a structured approach, organisations often struggle with excessive stock levels, poor availability of critical spares, and inefficiencies in procurement and storage.
The AMIS Spares & Materials Management Audit provides a comprehensive assessment of spares management practices, helping organisations benchmark their performance against industry best practices and identify opportunities for improvement. At MCP Consulting Group, we help businesses optimise their spares management strategies, ensuring they have the right parts available at the right time—without unnecessary stockholding costs.
BENCHMARKING & ASSESSMENTS SUB-CATEGORIES
What is a
Spares Assessment
A Spares Assessment is a structured evaluation designed to review and benchmark an organisation’s spare parts management against industry standards. It examines key areas such as inventory control, procurement processes, data quality, and stores management to identify inefficiencies and develop targeted improvement strategies.
At MCP, we conduct a detailed spares management review and assessment that analyses existing practices, highlights opportunities for cost savings, and develops a roadmap for achieving best-in-class spare parts management.
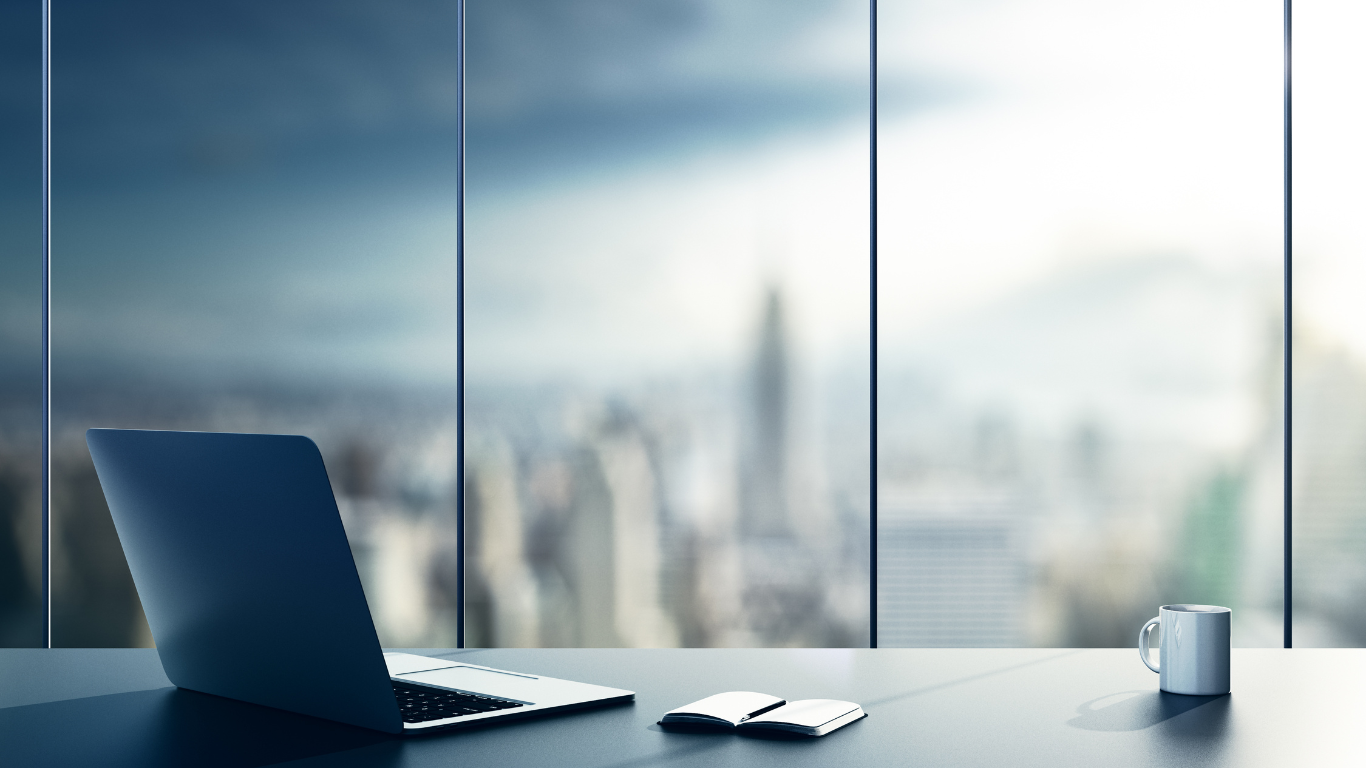
Key Objectives of a
Spares Assessment
Compare current practices with industry-leading standards and sector averages.
1
Benchmarking Spares Management Against Best Practices
Identifying Cost Reduction Opportunities
2
Highlight areas where inventory costs can be minimised without compromising availability.
Optimising Inventory Levels
3
Ensure that critical spares are available while reducing unnecessary stock.
Enhance purchasing efficiency to ensure cost-effective spare parts procurement.
4
Improving Procurement and Supplier Management
Enhancing Data Accuracy and Management Systems
5
Assess data quality and software integration to improve spare parts tracking and decision-making.
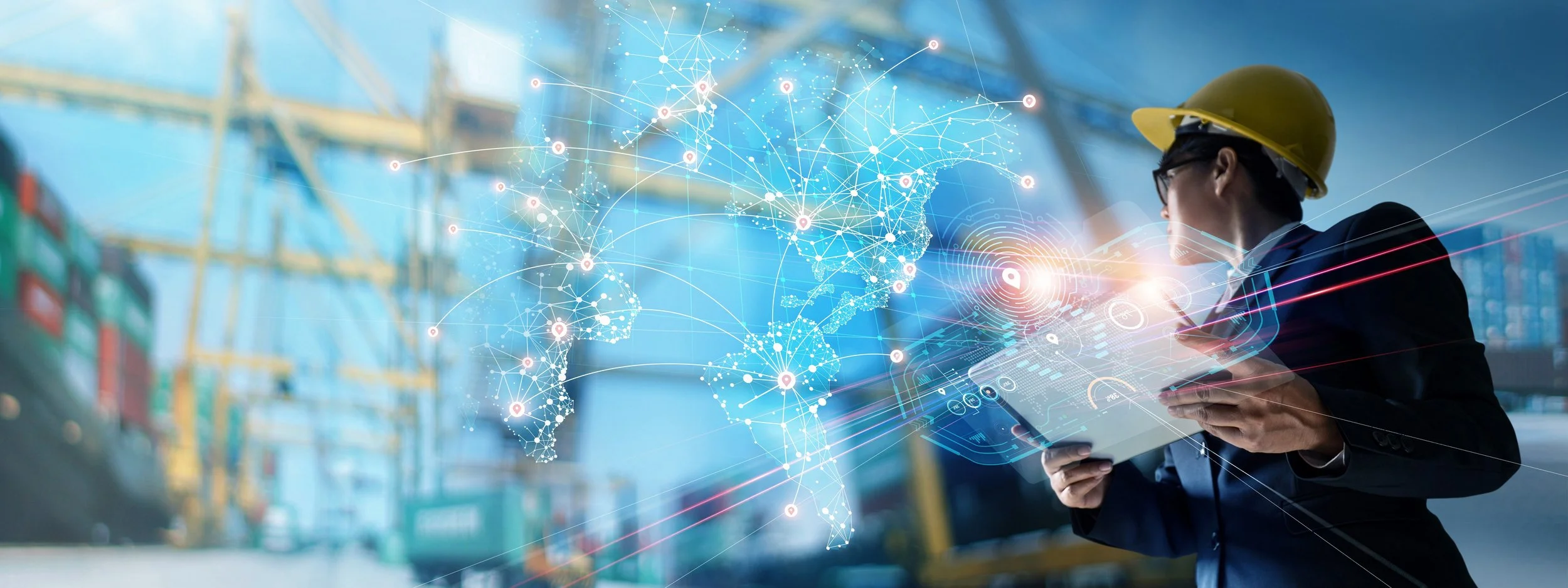
Key Areas Covered by a
Spares Assessment
The AMIS Spares & Materials Management Audit evaluates an organisation’s spare parts management across eight key areas:
ORGANISATION
Structure, roles, and responsibilities within the spares management team.
Standard operating procedures (SOPs) for spare parts handling and usage.
PROCEDURES
Best practices in spare parts storage, labelling, and accessibility.
SPARES MANAGEMENT
Stock control, reorder levels, and inventory turnover analysis.
INVENTORY MANAGEMENT
COST CONTROL
Strategies for minimising spare parts expenditure while maintaining availability.
Supplier management, procurement efficiency, and just-in-time (JIT) practices.
PURCHASING
Utilisation of CMMS, EAM, or ERP systems for spares tracking and management.
SOFTWARE SYSTEMS
Reporting, KPIs, and stakeholder engagement in spares management.
PERFORMANCE & COMMUNICATION
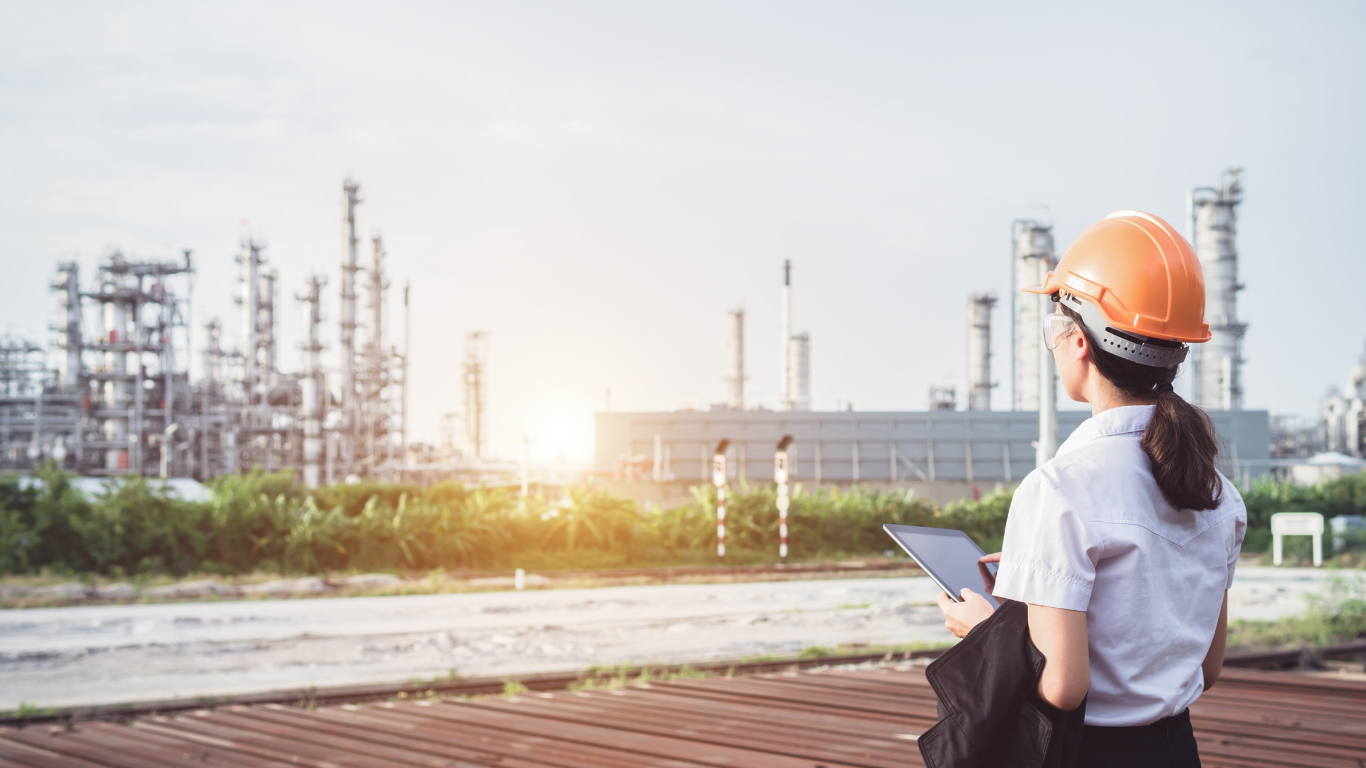
MCP Approach to
Spares Assessments
Review of Current Practices and Procedures
MCP conducts a detailed assessment of existing methods, processes, and data quality to establish a baseline for improvement.
Stakeholder Engagement and One-to-One Discussions
We engage with key personnel in maintenance, procurement, and stores management to gain insights into challenges and improvement opportunities.
Data Analysis and Key Ratio Calculation
Using benchmarking data and industry comparisons, we assess stock levels, procurement trends, and spare parts utilisation rates.
Review of Parts Data Quality and Approach
Initial review of a sample of the parts data base to identify the scope for improvement in terms of parts description, size of duplicate, obsolete and redundant items.
Scoring and Benchmarking Against AMIS Database
Each organisation is given performance scores in key areas, benchmarked against the AMIS database of industry best practices and sector averages.
Improvement Recommendations
We provide a detailed improvement and action plan that includes specific recommendations for optimising spares inventory, procurement efficiency, and stores management practices.
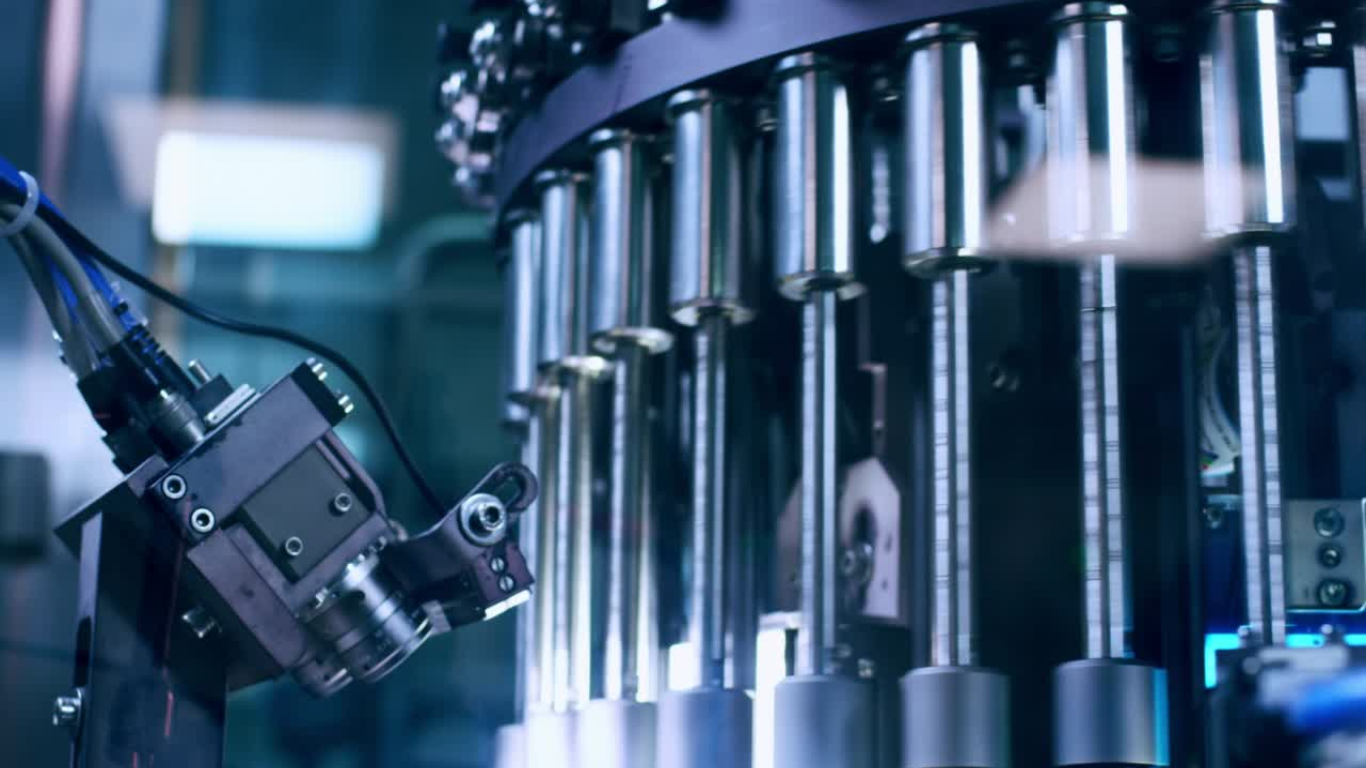
Benchmarking & Assessments
Explore More
Speak to One of Our
Experienced Consultants
If you have any questions or would like to learn more about how MCP Consulting Group can support your organisation with a Spares Assessment, please get in touch with us.
Our team of consultants is ready to provide tailored solutions to benchmark spares management performance, optimise inventory, and drive operational efficiency. Contact us today to discuss your specific requirements.
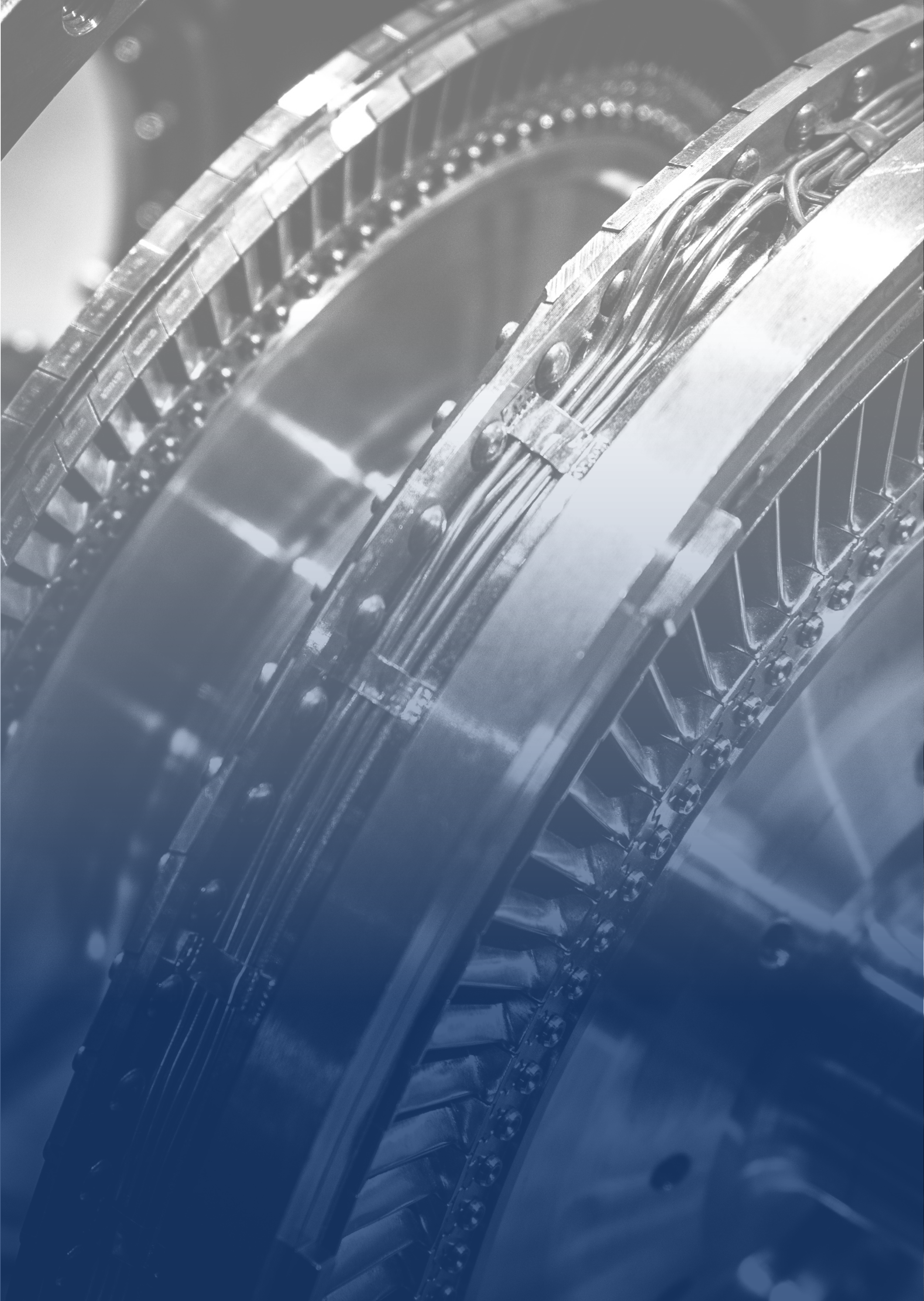
FAQs
-
The duration depends on site size and inventory complexity, but a typical manufacturing site requires at least three days on-site for a full assessment.
-
Yes, we assess current team structures, workload, and efficiency, providing recommendations for optimising resources.
-
Yes, each category is scored and benchmarked against the AMIS database and sector averages to highlight strengths and improvement areas.
-
Yes, we can include an optional data quality review to assess the accuracy and completeness of spare parts records.
-
Yes, our analysis identifies opportunities for cost reduction, stock level optimisation, and procurement efficiency improvements.