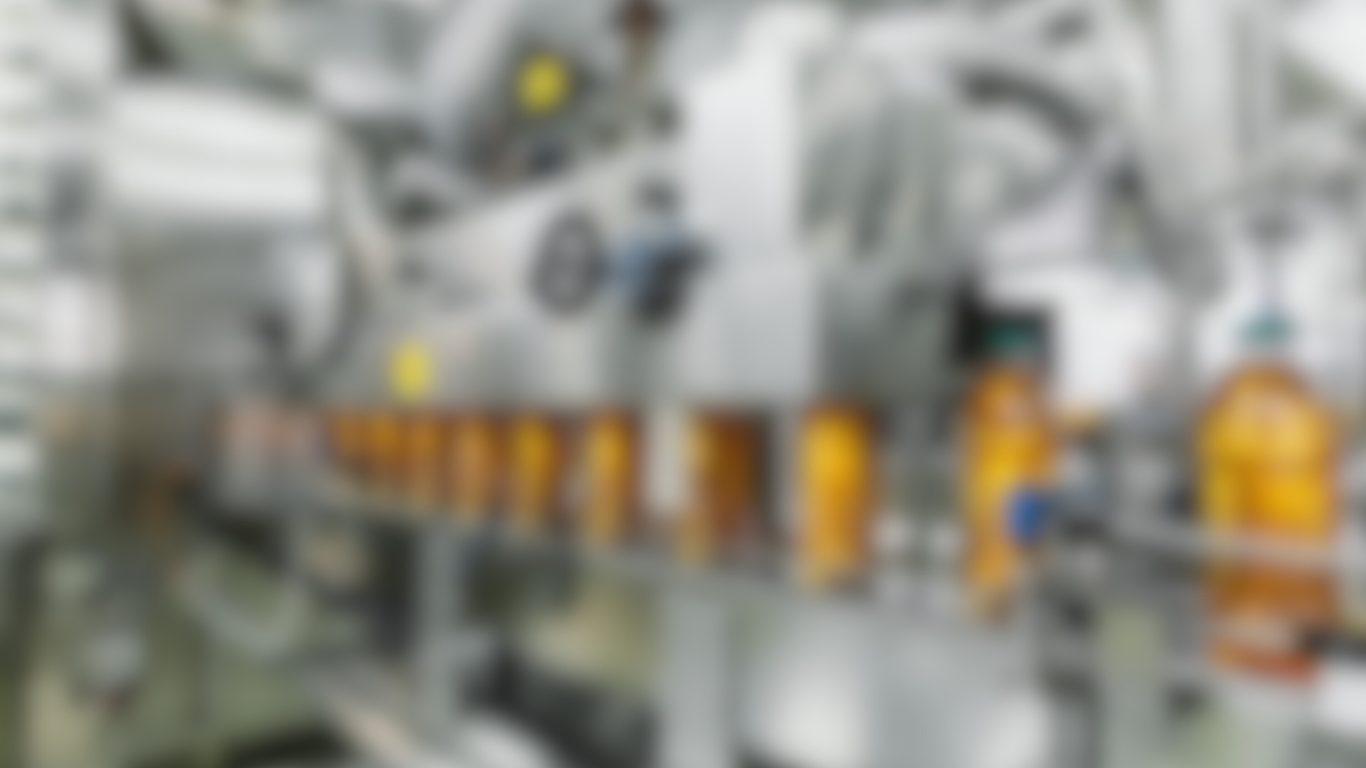
Key Performance Indicators
Measuring and improving maintenance performance is essential for maximising asset reliability, optimising costs, and driving continuous improvement. Key Performance Indicators (KPIs) provide organisations with measurable insights into the effectiveness of their maintenance strategies, work management, and operational efficiency.
At MCP Consulting Group, we help businesses define, implement, and monitor KPIs tailored to their maintenance and reliability objectives, ensuring data-driven decision-making and sustained operational improvements.
CONTINUOUS IMPROVEMENT
SUB-CATEGORIES
What are
Key Performance Indicators (KPIs)
Operator Asset Care (OAC) is a methodology that integrates equipment operators into the maintenance process, enabling them to perform routine tasks such as cleaning, lubrication, and basic inspections. This approach not only enhances the operators' understanding of their equipment but also facilitates early detection of potential issues, thereby preventing unexpected failures and promoting a collaborative maintenance environment.
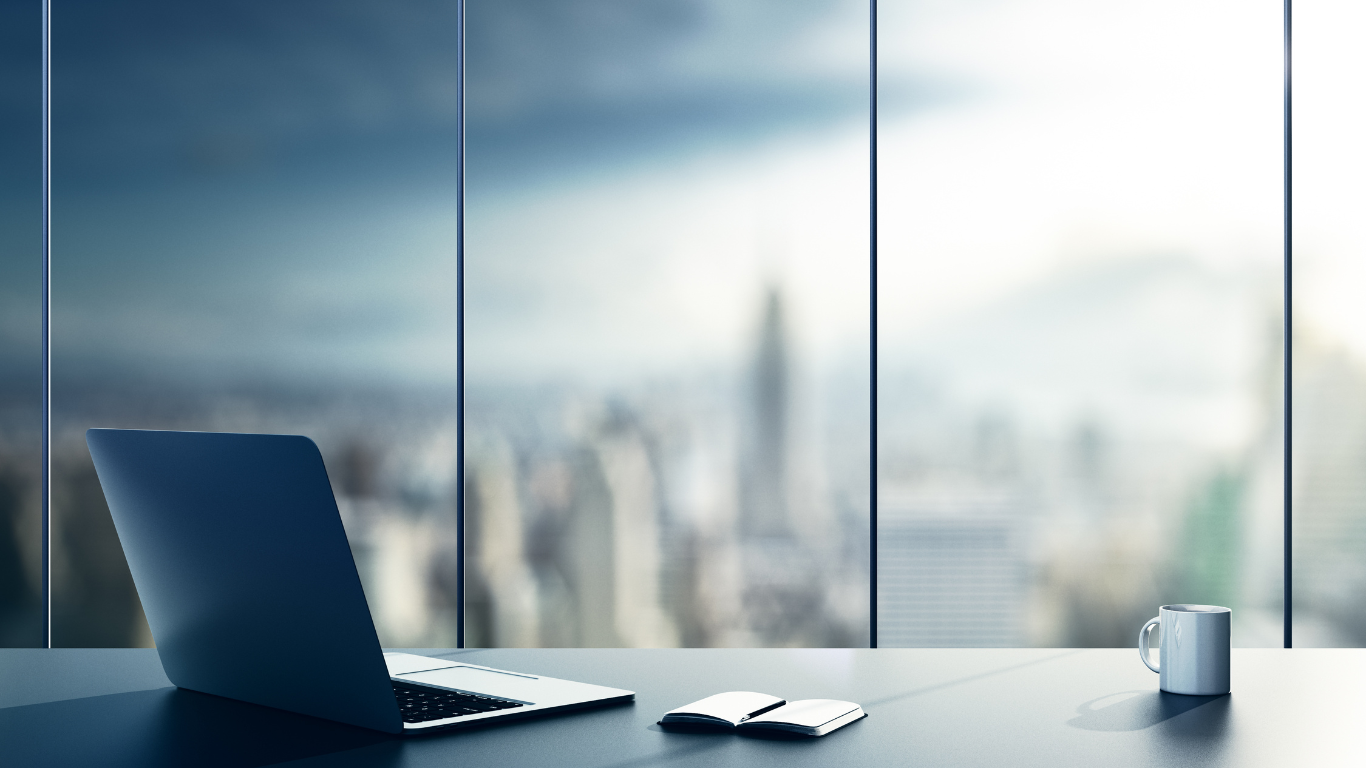
Key Objectives of
Maintenance KPIs
Track and improve maintenance work execution, ensuring timely and effective task completion.
1
Enhancing Maintenance Efficiency
Reducing Downtime and Failures
2
Measure asset reliability and performance trends to minimise unexpected breakdowns.
Optimising Maintenance Costs
3
Monitor budget allocations and cost drivers to maximise cost-efficiency.
Ensuring Compliance and Safety
Assess work scheduling, response times, and resource allocation for enhanced performance.
4
Improving Workforce Productivity
5
Track adherence to regulatory and industry standards for health, safety, and environmental compliance.
Common
Maintenance KPIs
Mean Time Between Failures (MTBF) - Measures the average time between asset failures, indicating reliability.
1
Mean Time to Repair (MTTR) - Evaluates how quickly assets are restored after a failure.
2
Planned vs. Unplanned Maintenance Ratio - Compares scheduled maintenance tasks against unexpected repairs, aiming for a higher ratio of proactive maintenance.
3
Maintenance Backlog - Assesses the amount of overdue maintenance work, ensuring that work orders are managed effectively.
4
Work Order Completion Rate - Measures the percentage of planned maintenance tasks completed within schedule.
5
First-Time Fix Rate - Determines how often maintenance issues are resolved correctly on the first attempt, reducing repeat work.
6
Overall Equipment Effectiveness (OEE) - Evaluates asset performance based on availability, performance efficiency, and quality output.
7
Maintenance Cost as a Percentage of Asset Value - Helps monitor maintenance spending relative to asset worth, ensuring cost control.
8
Health, Safety, and Environmental (HSE) Compliance Rate - Tracks adherence to safety and environmental regulations to prevent risks.
9
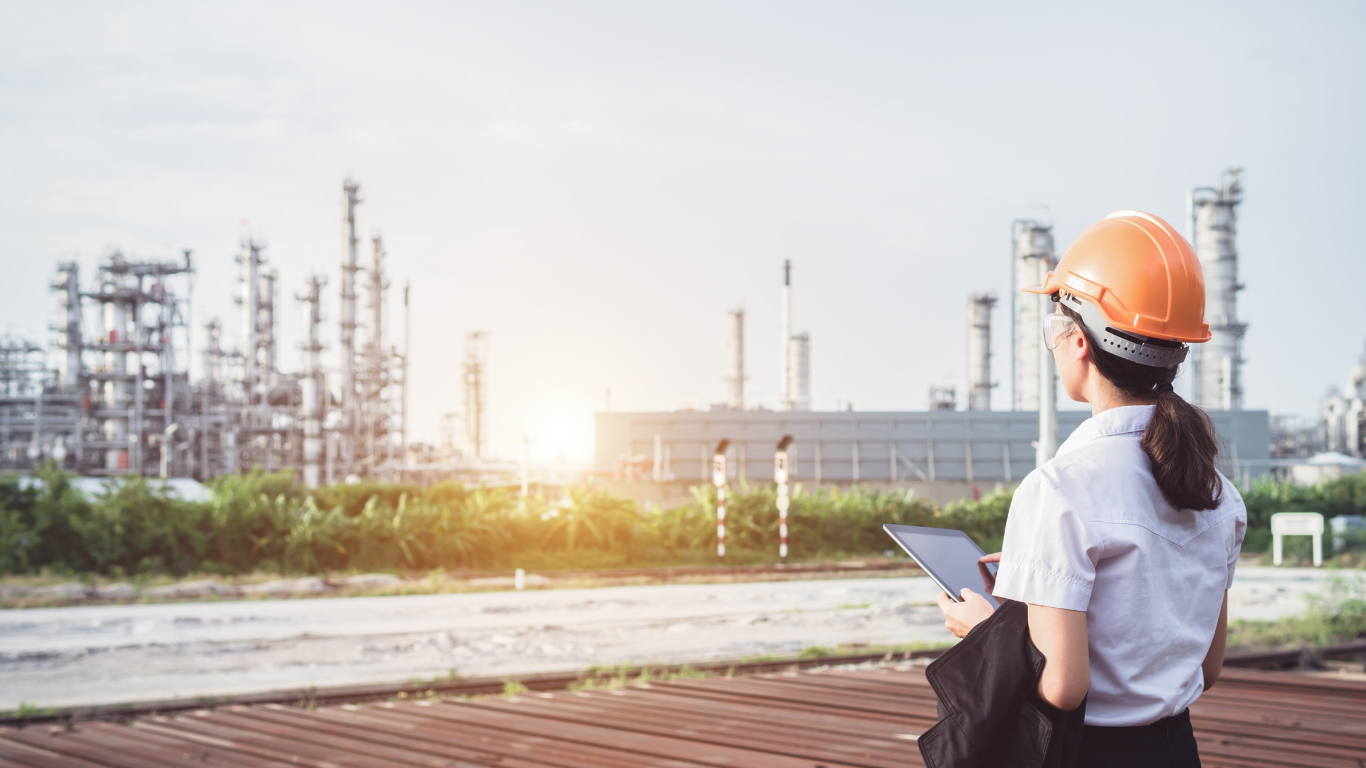
MCP Approach to
Implementing KPIs in Maintenance
Defining Business-Aligned KPIs
MCP works with organisations to identify maintenance KPIs aligned with business goals, industry standards, and operational priorities.
Integrating KPIs into Maintenance Systems
We support businesses in embedding KPI tracking into Computerised Maintenance Management Systems (CMMS) and Enterprise Asset Management (EAM) platforms.
Developing KPI Dashboards and Reporting Tools
Our consultants design real-time dashboards, visual reports, and trend analyses to enhance performance monitoring.
Training and Workforce Engagement
We provide training to maintenance teams, managers, and operators on KPI interpretation and data-driven decision-making.
Continuous Monitoring and Optimisation
MCP helps organisations review, refine, and optimise KPIs to adapt to changing operational conditions and industry benchmarks.
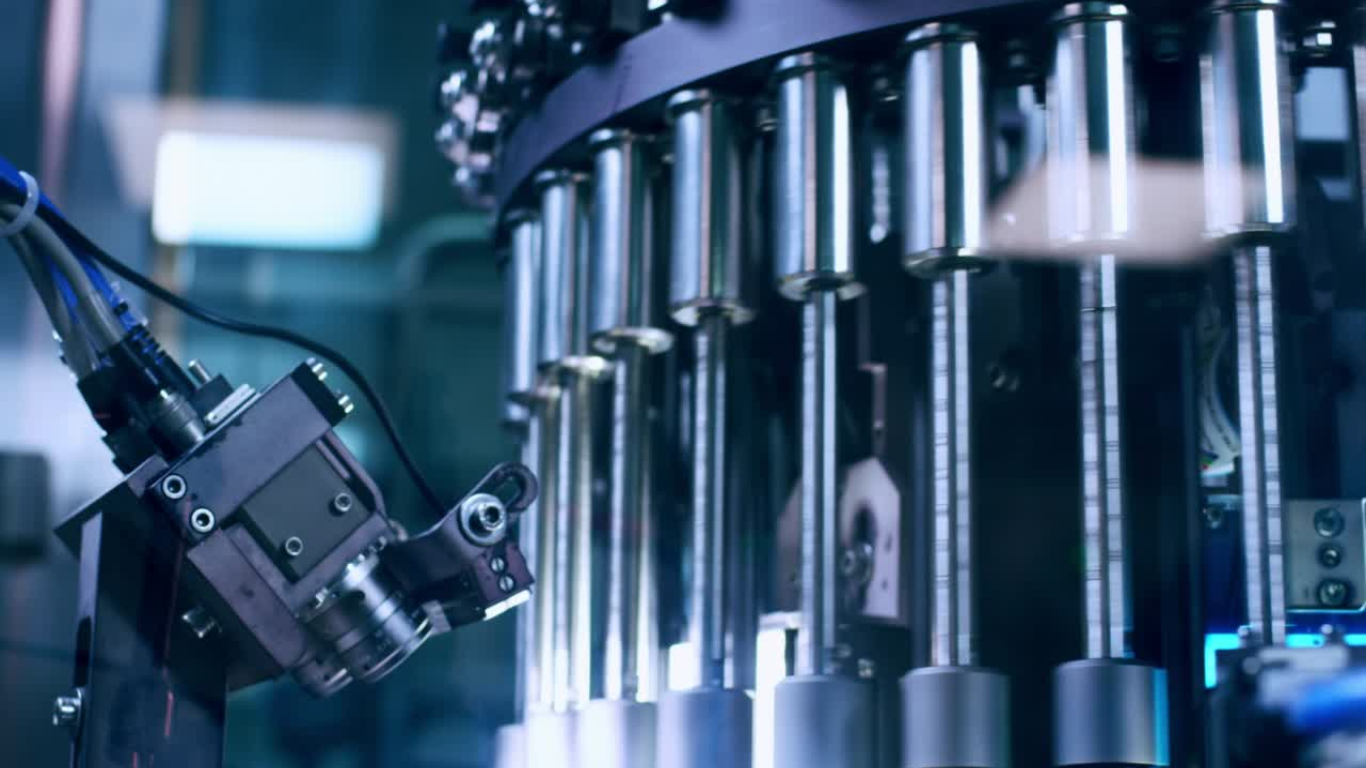
Continuous Improvement
Explore More
Speak to One of Our
Experienced Consultants
If you have any questions or would like to learn more about how MCP Consulting Group can support your organisation with maintenance KPIs, please get in touch with us.
Our team of consultants is ready to provide tailored solutions to enhance performance monitoring, optimise maintenance strategies, and improve asset reliability. Contact us today to discuss your specific requirements.
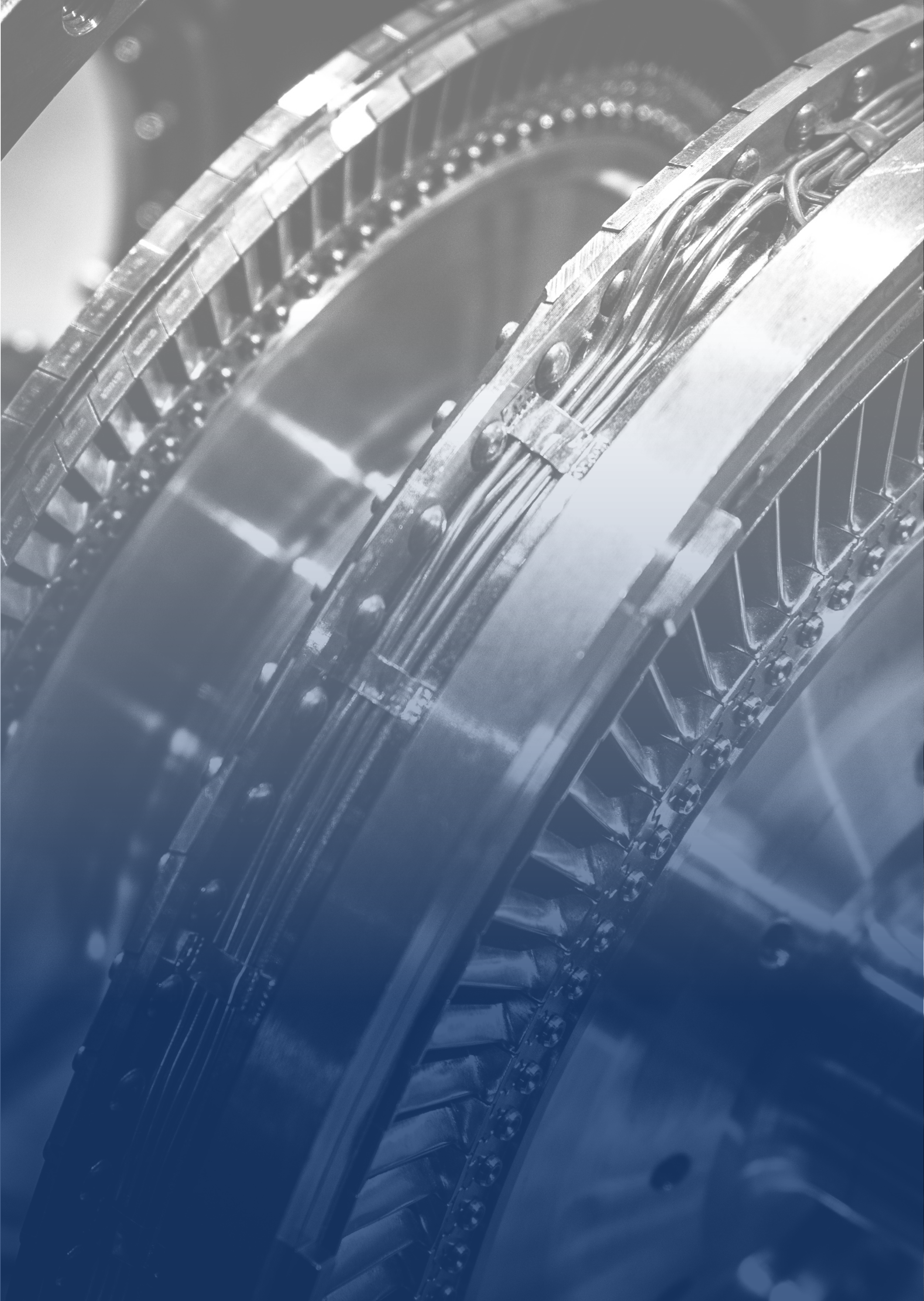
FAQs
-
KPIs help businesses track, measure, and improve maintenance performance, ensuring cost-effective asset management and reliability.
-
Maintenance KPIs should be reviewed monthly or quarterly, depending on business needs and asset criticality.
-
KPIs can be tracked using CMMS, EAM systems, real-time dashboards, and periodic maintenance reports.
-
Performance improvements come from optimised work planning, predictive maintenance, workforce training, and data-driven decision-making.
-
Asset-intensive industries such as manufacturing, energy, utilities, healthcare, and transportation rely on KPIs for efficient maintenance management.