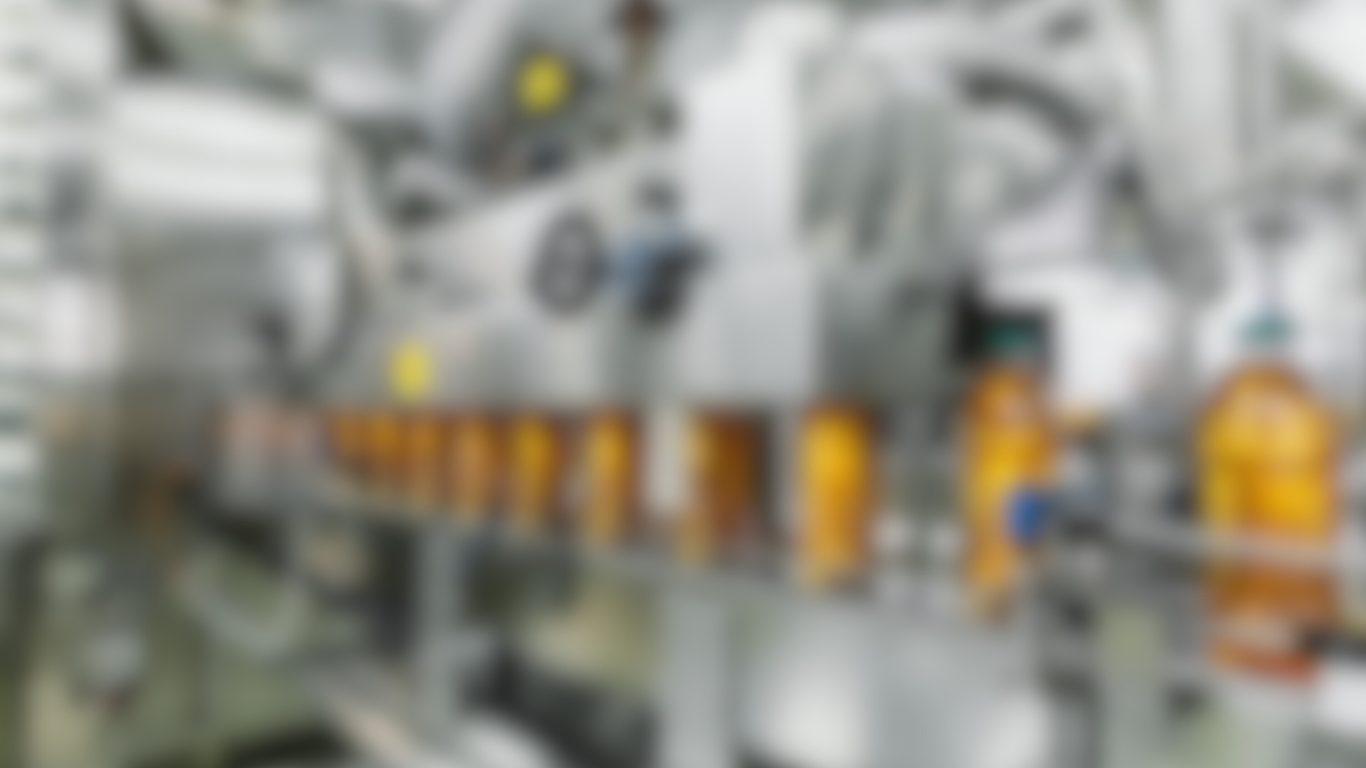
Continuous Improvement Support
Sustaining high levels of maintenance efficiency and asset reliability requires an ongoing commitment to continuous improvement. By leveraging structured methodologies such as 5S, Kaizen, and Lean principles, organisations can optimise processes, eliminate waste, and enhance productivity.
At MCP Consulting Group, we provide tailored consultancy services to help businesses implement continuous improvement frameworks that drive operational excellence and long-term maintenance efficiency.
CONTINUOUS IMPROVEMENT
SUB-CATEGORIES
What is
Continuous Improvement in Maintenance
Continuous Improvement (CI) is a structured, data-driven approach to identifying inefficiencies, implementing small yet impactful changes, and ensuring that maintenance processes evolve to meet business needs. This includes refining work management, optimising resource allocation, and embedding a culture of continuous learning and adaptation within maintenance teams.
At MCP, we support businesses in integrating continuous improvement principles into their maintenance strategies, ensuring sustainable performance enhancements and cost efficiency.
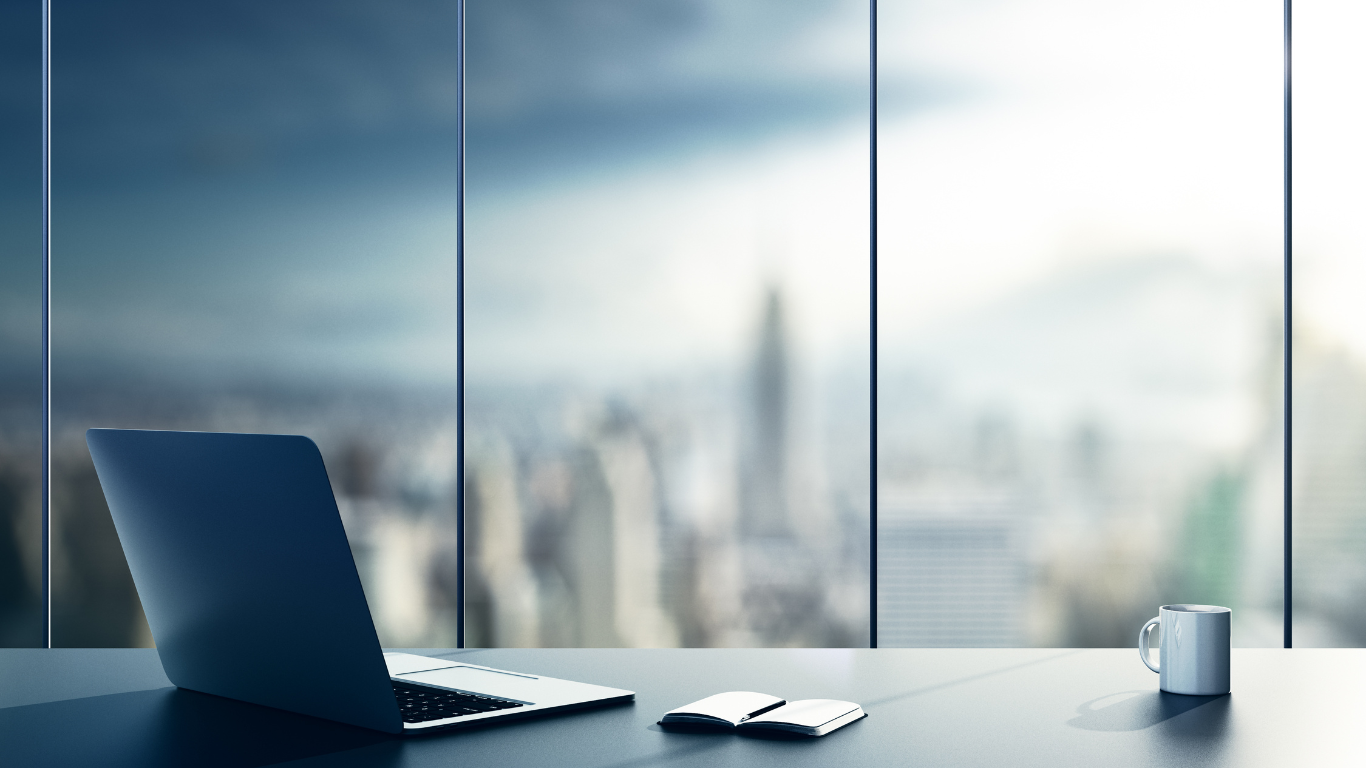
Key Objectives of
Continuous Improvement in Maintenance
Identify and eliminate waste in maintenance processes to improve productivity.
2
1
Enhancing Operational Efficiency
Reducing Maintenance Costs
Implement cost-saving strategies by streamlining workflows and reducing non-value-added activities.
Improving Equipment Reliability
3
Increase asset availability through proactive problem-solving and standardised maintenance practices.
Ensuring Sustainable Improvements
Encourage maintenance teams to actively participate in process improvement initiatives.
4
Fostering a Culture of Continuous Learning
5
Implement structured methodologies that deliver long-term benefits rather than short-term fixes.
Methodologies for
Continuous Improvement in Maintenance
5S Methodology – A structured workplace organisation system that enhances efficiency by improving sort, set in order, shine, standardise, and sustain principles.
1
2
Kaizen – A philosophy of continuous, incremental improvements driven by frontline employees to improve processes over time.
Lean Maintenance – Eliminating waste in maintenance processes by optimising work execution, resource utilisation, and asset management.
3
Root Cause Analysis (RCA) – Identifying and eliminating the underlying causes of asset failures to improve long-term reliability.
4
Failure Modes, Effects, and Criticality Analysis (FMECA) – A structured risk-based assessment to identify failure patterns and optimise preventive maintenance.
5
Plan-Do-Check-Act (PDCA) Cycle – A four-step problem-solving method used for process improvement and continuous maintenance optimisation.
6
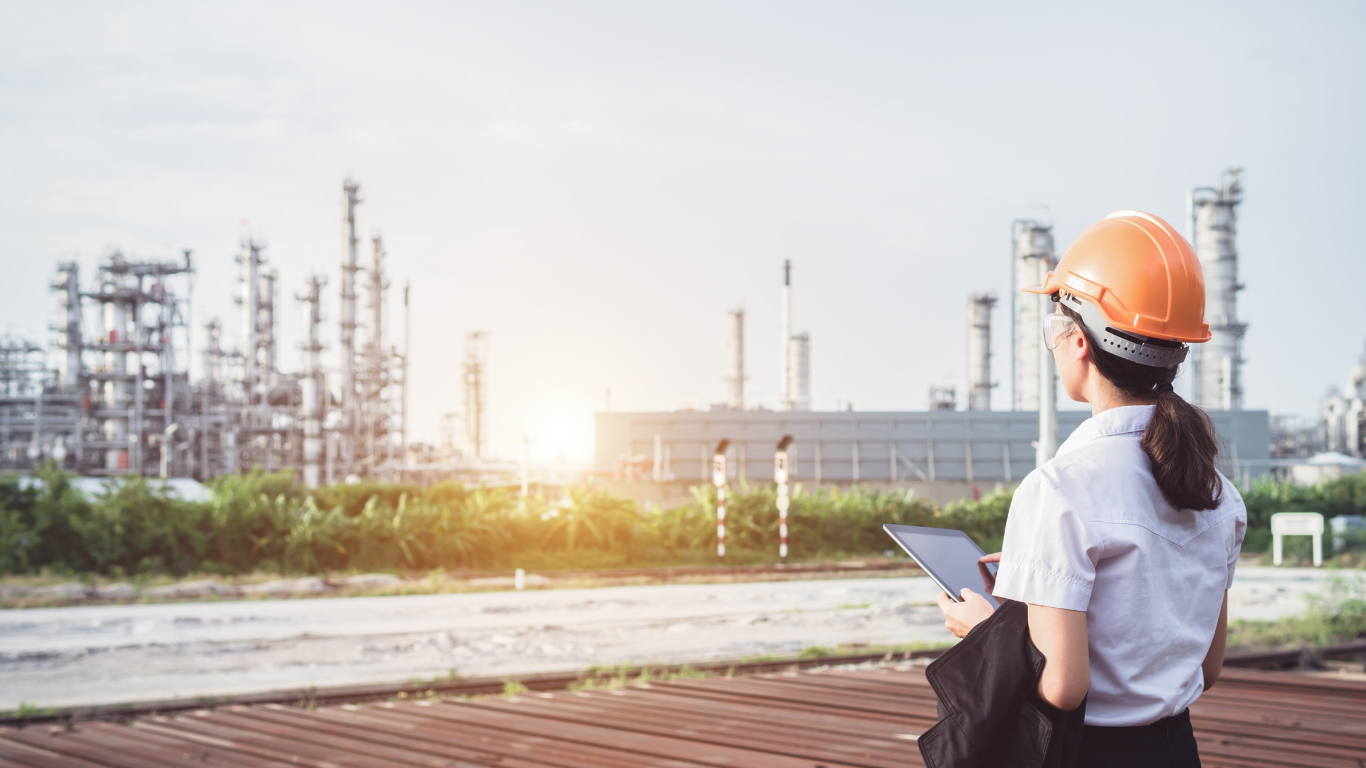
MCP Approach to
Continuous Improvement in Maintenance
Assessing Current Maintenance Processes
MCP evaluates existing maintenance strategies, work management practices, and resource allocation to identify areas for improvement.
Developing Tailored CI Programmes
We help businesses design and implement structured continuous improvement frameworks that align with their operational goals and industry best practices.
Integrating Lean and Kaizen Principles
Our consultants support organisations in embedding Lean, 5S, and Kaizen into their maintenance culture, fostering proactive problem-solving and efficiency gains.
Training and Workforce Engagement
We provide workshops and hands-on training to equip maintenance teams with the skills to identify inefficiencies and implement process improvements.
Performance Monitoring and Continuous Review
MCP assists in establishing KPIs, dashboards, and reporting tools to measure the impact of CI initiatives and drive ongoing enhancements.
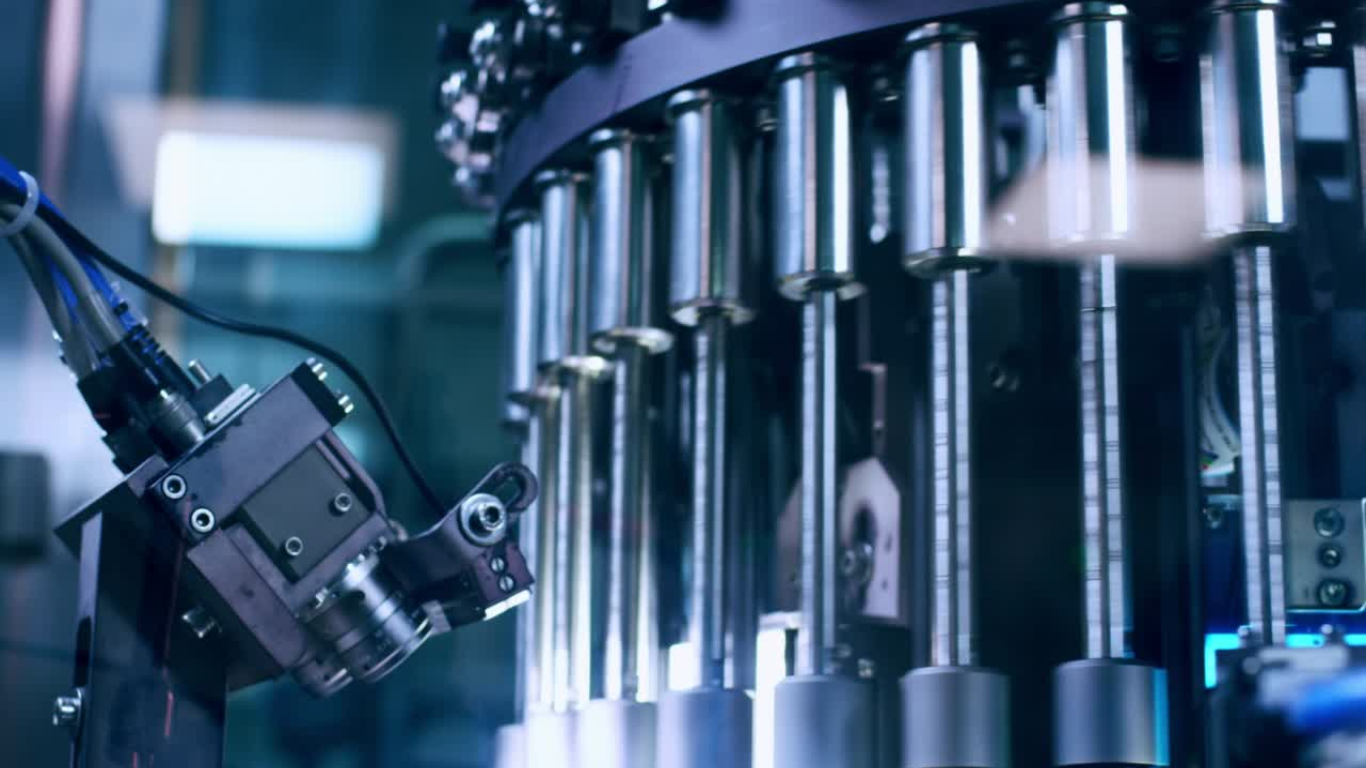
Continuous Improvement
Explore More
Speak to One of Our
Experienced Consultants
If you have any questions or would like to learn more about how MCP Consulting Group can support your organisation with Continuous Improvement, please get in touch with us.
Our team of consultants is ready to provide tailored solutions to optimise maintenance processes, improve efficiency, and enhance asset reliability. Contact us today to discuss your specific requirements.
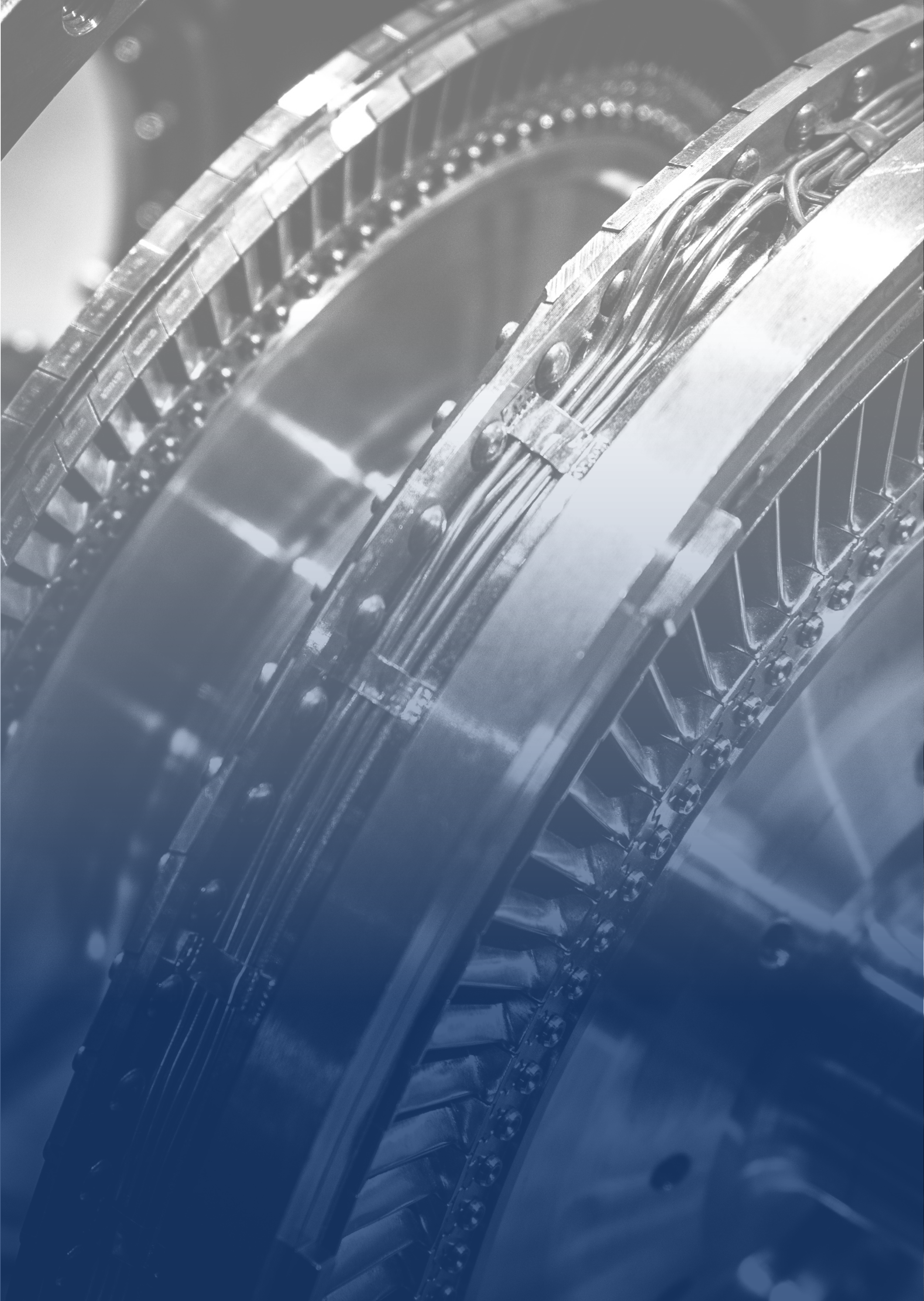
FAQs
-
Continuous improvement helps reduce downtime, improve resource efficiency, and enhance equipment reliability through structured problem-solving.
-
Lean focuses on eliminating waste and optimising efficiency, while Kaizen encourages incremental, ongoing improvements driven by employees.
-
The timeframe varies depending on company size, complexity, and organisational readiness, but initial improvements can often be seen within 3 to 6 months.
-
Yes, manufacturing, energy, healthcare, and transportation sectors benefit significantly from structured continuous improvement initiatives.
-
Success is measured through KPIs, reduction in downtime, cost savings, and overall asset performance improvements.