
Work Management Support
Effective work management is critical to ensuring maintenance activities are planned, scheduled, and executed efficiently. At MCP Consulting Group, we provide tailored consultancy services to help organisations optimise their work management processes, improve resource allocation, and enhance operational reliability.
WORK MANAGEMENT SUB-CATEGORIES
What Is
Work Management
Work management involves the structured planning, execution, and tracking of maintenance tasks to maximise productivity and asset performance. A well-implemented work management strategy ensures that maintenance activities are prioritised correctly, resources are allocated effectively, and downtime is minimised.
At MCP, we help organisations develop and refine their work management frameworks, incorporating best practices and digital solutions to drive efficiency and continuous improvement.

Key Objectives of
Work Management
1
Optimising Work Planning and Execution
Develop structured approaches to maintenance work, ensuring tasks are clearly defined and properly resourced.
2
Improving Work Scheduling Efficiency
Ensure maintenance activities are scheduled effectively to minimise operational disruptions and maximise technicians’ productivity.
3
Enhancing Resource Utilisation
Allocate labour, materials, and equipment efficiently to optimise maintenance service.
4
Implementing Digital Solutions
Leverage Computerised Maintenance Management Systems (CMMS) to streamline work management processes.
5
Ensuring Compliance and Continuous Improvement
Align maintenance activities with regulatory standards and industry best practices to drive long-term success.
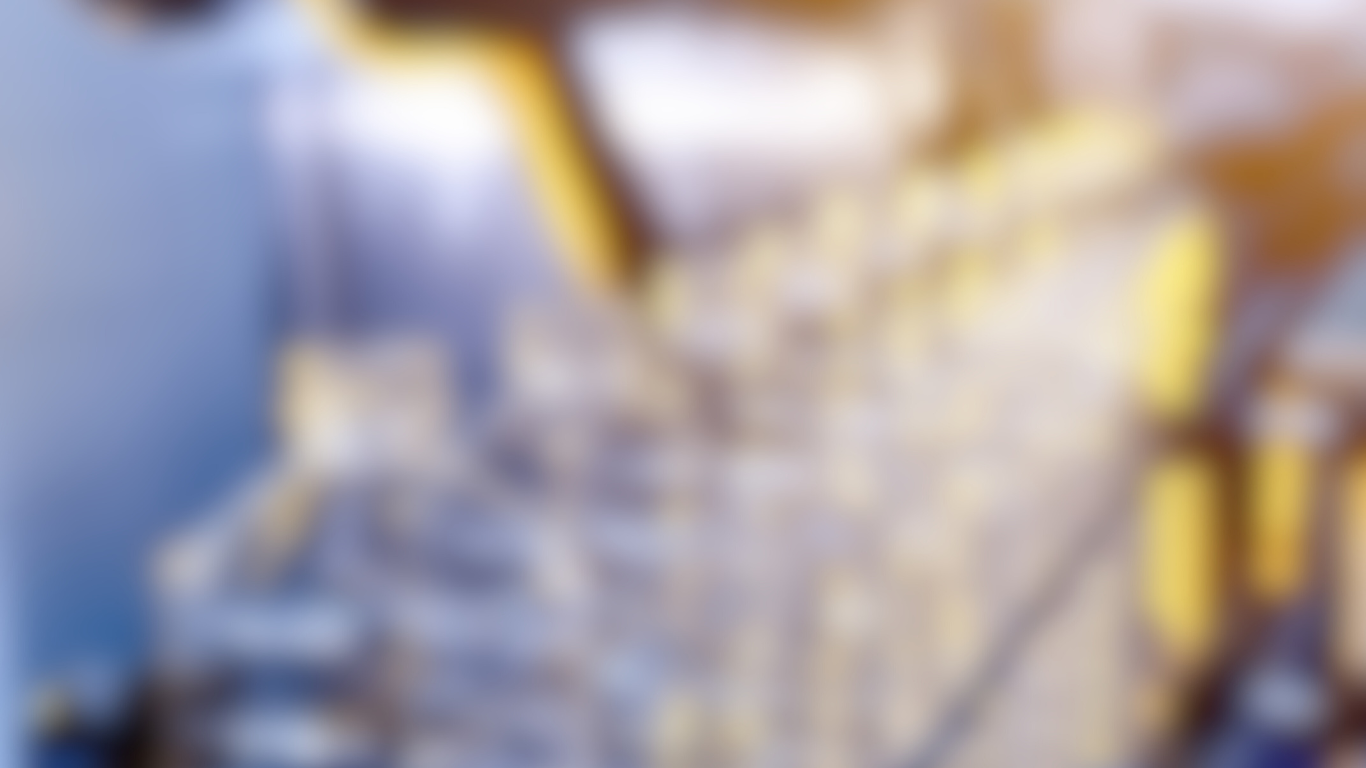
MCP Approach to
Work Management
Optimised Work Order Management with CMMS
MCP assists organisations in selecting and implementing CMMS to digitally manage, assign, and track work orders. Our solutions help businesses improve efficiency, reduce paperwork, and ensure real-time visibility into maintenance activities.
We help organisations transition from reactive to proactive maintenance by structuring work management around scheduled inspections, condition-based monitoring, and predictive analytics. This approach reduces unplanned downtime and extends asset lifespan.
Proactive Preventive and Predictive Maintenance Scheduling
An effective work management structure requires defined roles, responsibilities, and standardised procedures. MCP works with organisations to develop clear workflows, ensuring better coordination between maintenance teams and other departments.
Establishing Clear Workflows and Team Responsibilities
We support businesses in defining Key Performance Indicators (KPIs) to measure work completion rates, response times, backlog management, and workforce efficiency. By tracking these metrics, organisations can continuously improve their work management strategies.
Performance Monitoring Through KPIs
MCP provides regular assessments of work schedules and resource allocation. Through periodic reviews, we help organisations eliminate inefficiencies, balance workloads, and enhance overall maintenance productivity.
Continuous Review and Work Schedule Optimisation
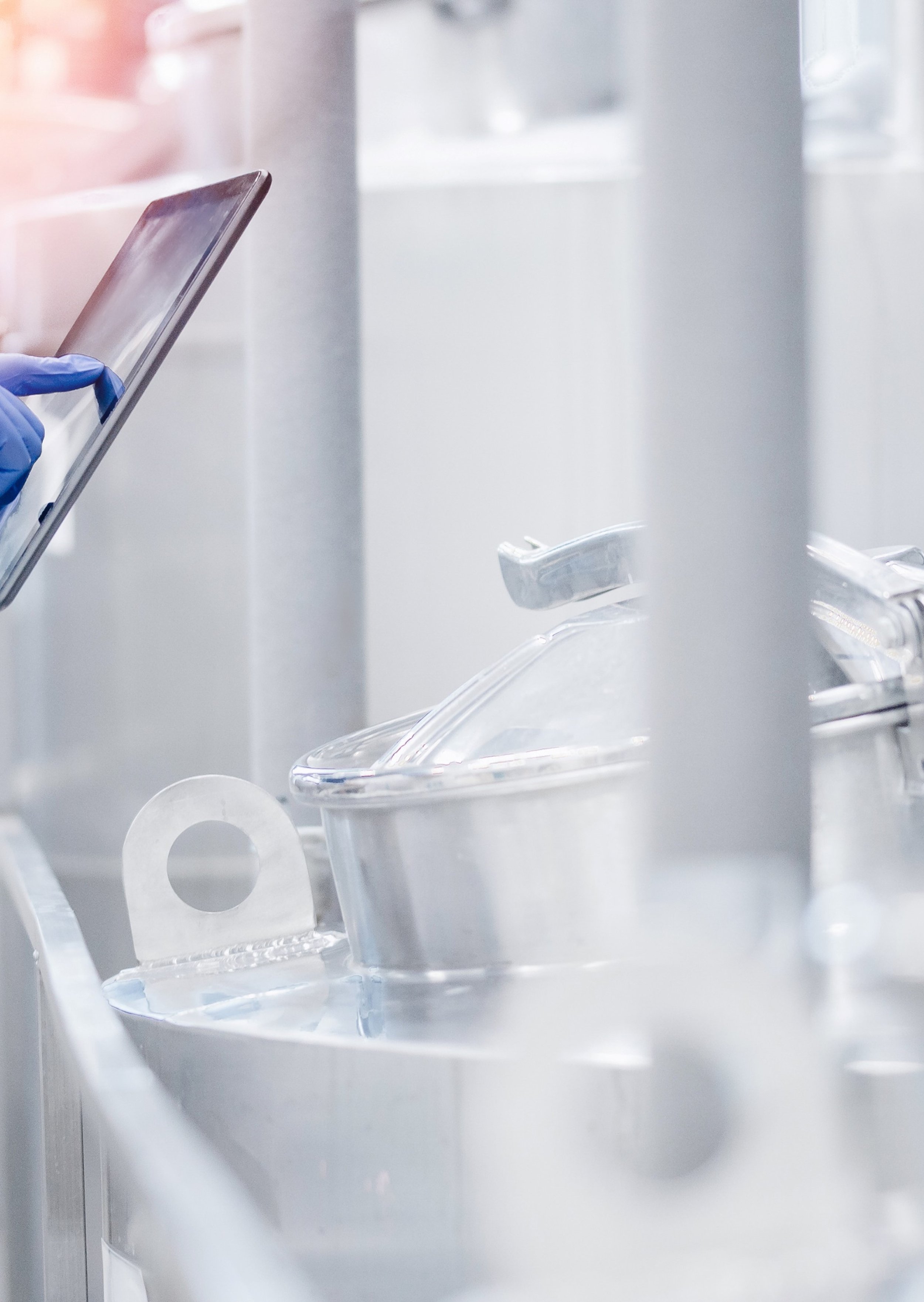
Work Management
Discover More
Speak to One of Our
If you have any questions or would like to learn more about how MCP Consulting Group can help your organisation implement an effective work management strategy, please get in touch with us.
Our team of consultants is ready to provide tailored solutions to optimise maintenance processes and improve overall efficiency. Contact us today to discuss your specific requirements.
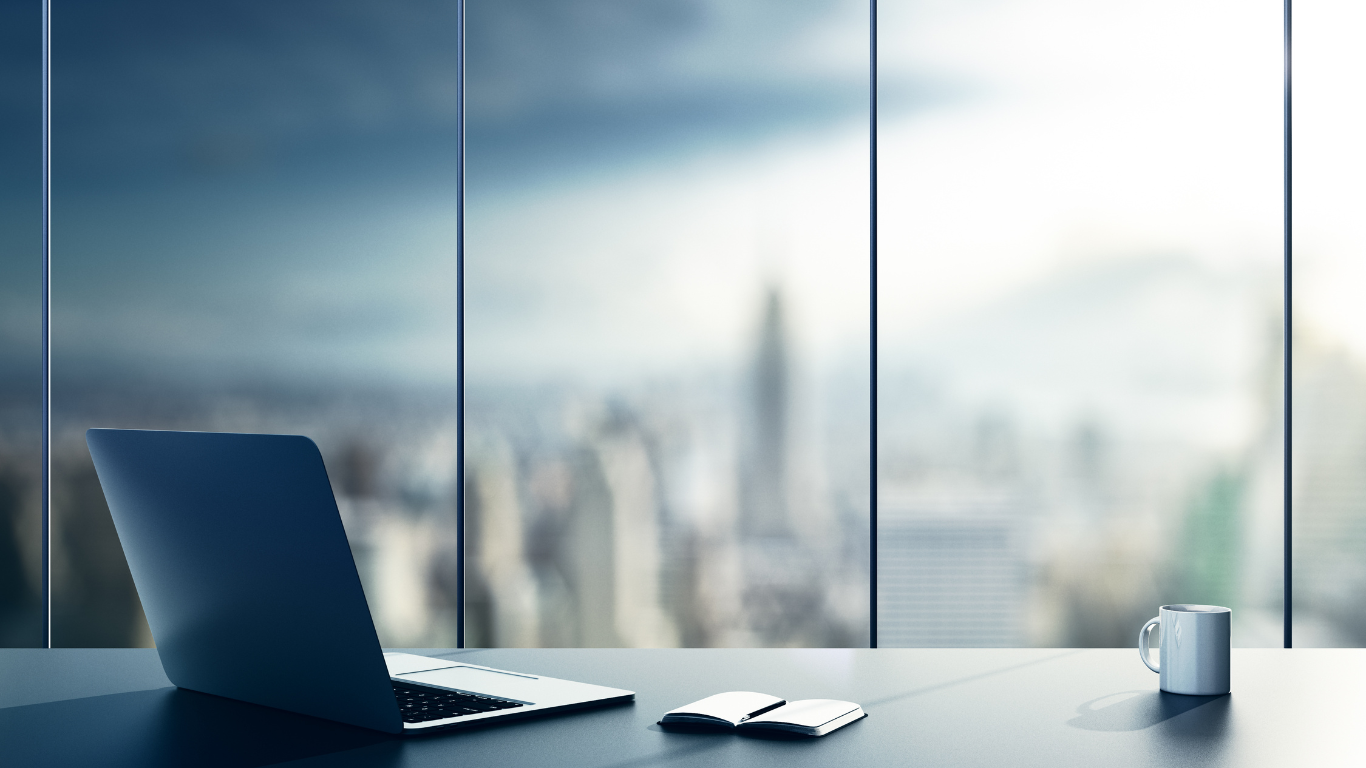
FAQs
-
Improved asset reliability, reduced maintenance costs, enhanced workforce productivity, and minimised downtime.
-
A CMMS supports work management by automating task assignments, tracking work orders, and maintaining maintenance records.
-
Proper scheduling ensures the right resources are available at the right time, reducing delays and improving productivity.
-
Industries where cost is a critical factor, such as manufacturing, energy, healthcare, and transportation will see the greatest benefit.