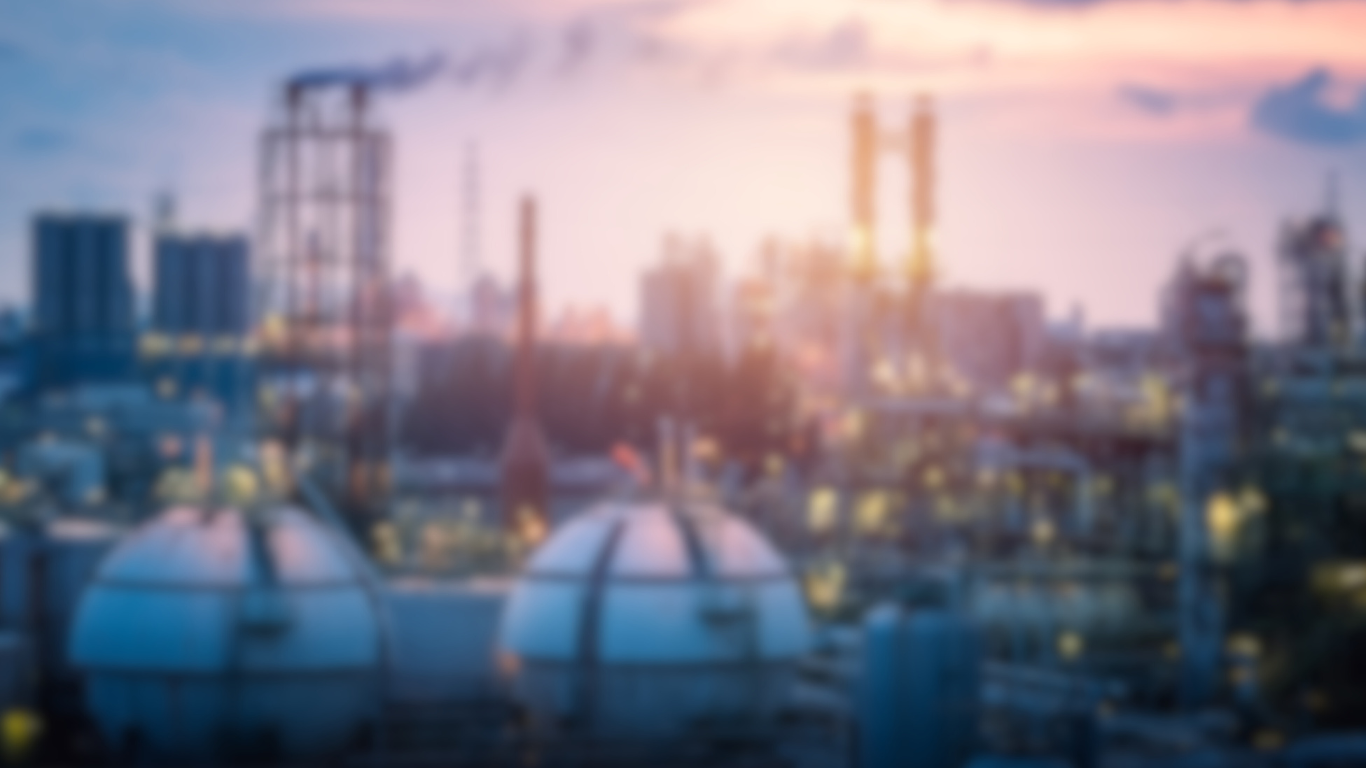
Our Experience
Our Experience in Industry
OPERATIONAL EXCELLENCE
-
A leading bakery wanted to improve performance across its 16 bakeries and bring a Single Company Way to operational organisation and implement a common Operational Excellence framework across each site.
-
The project involved developing an assessment tool and Operational Excellence handbook for the business and then by assessing each site, developing an individual improvement plan. We supported each site in implementing their plan through coaching and mentoring, by designing and delivering improvements, including a lean daily work system, Overall Equipment Effectiveness (OEE) framework, rapid changeover and 5S (Five S’s of Lean Manufacturing) activities as well as the development of risk-based maintenance activities.
-
Over the 4 years of the programme, the business improved:
plant efficiency and throughput by over 122%
reliability by 8%
made savings across the business in the region of £4 million
LEAN MANAGEMENT
-
A consumer products facility of a major pharmaceutical company based in South Africa wanted to improve the performance of its manufacturing and engineering operation, to increase productivity and reliability and to adopt the best practice approaches to manufacturing and engineering which its parent group was rolling out across the business.
-
A gap analysis was completed across both manufacturing and engineering to identify areas of focus during the one year project. During this project the operations department was restructured with new job roles and responsibilities. A lean programme was implemented covering daily management, 5S, OEE improvements and rapid changeover. This was supported through the development of a culture of performance and problem solving through the use of Root Cause and Six Sigma. This was supported by the coaching and mentoring of key staff to sustain the changes once the project was completed.
-
At the completion of this programme the site had:
improved its internal compliance score from 24% to 68%
increased the average OEE from 38% to 64%
virtually eliminated the number of failed and quarantine batches of product
achieved estimated savings in the region of £900,000 in the first year
ASSET MANAGEMENT
-
A world leading pharmaceutical company with 18 sites across the globe were looking to develop a Global Asset Care Excellence Programme across its sites, to bring both consistency of application and reduction in maintenance costs.
-
A Global Asset Care Excellence Programme was developed with our Global Pharma Engineering Team which included carrying out baseline assessments of asset care practices and developing improved processes and ways of working, to advance equipment output and productive capacity, whilst developing the capability and skill set of the site teams.
The project covered such topics as work planning and scheduling, reliability improvements as well as appropriate aspects of lean manufacturing and risk-based maintenance activities. The project objectives were achieved through the development of processes with the site teams and the coaching and mentoring of staff to in-still the new processes.
The project covered such topics as work planning and scheduling, reliability improvements as well as appropriate aspects of lean manufacturing and risk-based maintenance activities. The project objectives were achieved through the development of processes with the site teams and the coaching and mentoring of staff to in-still the new processes.
-
Over the 5 year duration of the programme, our client achieved:
cost savings across the 18 sites of over 24 million
cost avoidance in the order of £40 million
reductions in head count across all sites
increased productive capacity by over 10%
improved productivity and quality
MAINTENANCE IMPROVEMENT
-
A major UK based food company was suffering from reliability and capacity issues which resulted in high levels of overtime and frequent service failures.
-
A Gap Analysis was carried out which identified several key issues which needed to be addressed for performance to be improved in a sustainable manner. This included developing optimised maintenance plans using risk-based approaches, introducing a maintenance work planning and scheduling system, a daily lean production management process as well as a problem-solving process using Root Cause.
The project covered such topics as work planning and scheduling, reliability improvements as well as appropriate aspects of lean manufacturing and risk-based maintenance activities. The project objectives were achieved through the development of processes with the site teams and the coaching and mentoring of staff to in-still the new processes.
The project covered such topics as work planning and scheduling, reliability improvements as well as appropriate aspects of lean manufacturing and risk-based maintenance activities. The project objectives were achieved through the development of processes with the site teams and the coaching and mentoring of staff to in-still the new processes.
-
At the conclusion of the project:
the plant efficiency had increased by 25%
equipment failures had decreased by 10%
production scheduling and adherence had increased by 17%

Stay in Touch
Be the first to access expert-led webinars, exclusive resources, and maintenance improvement insights.