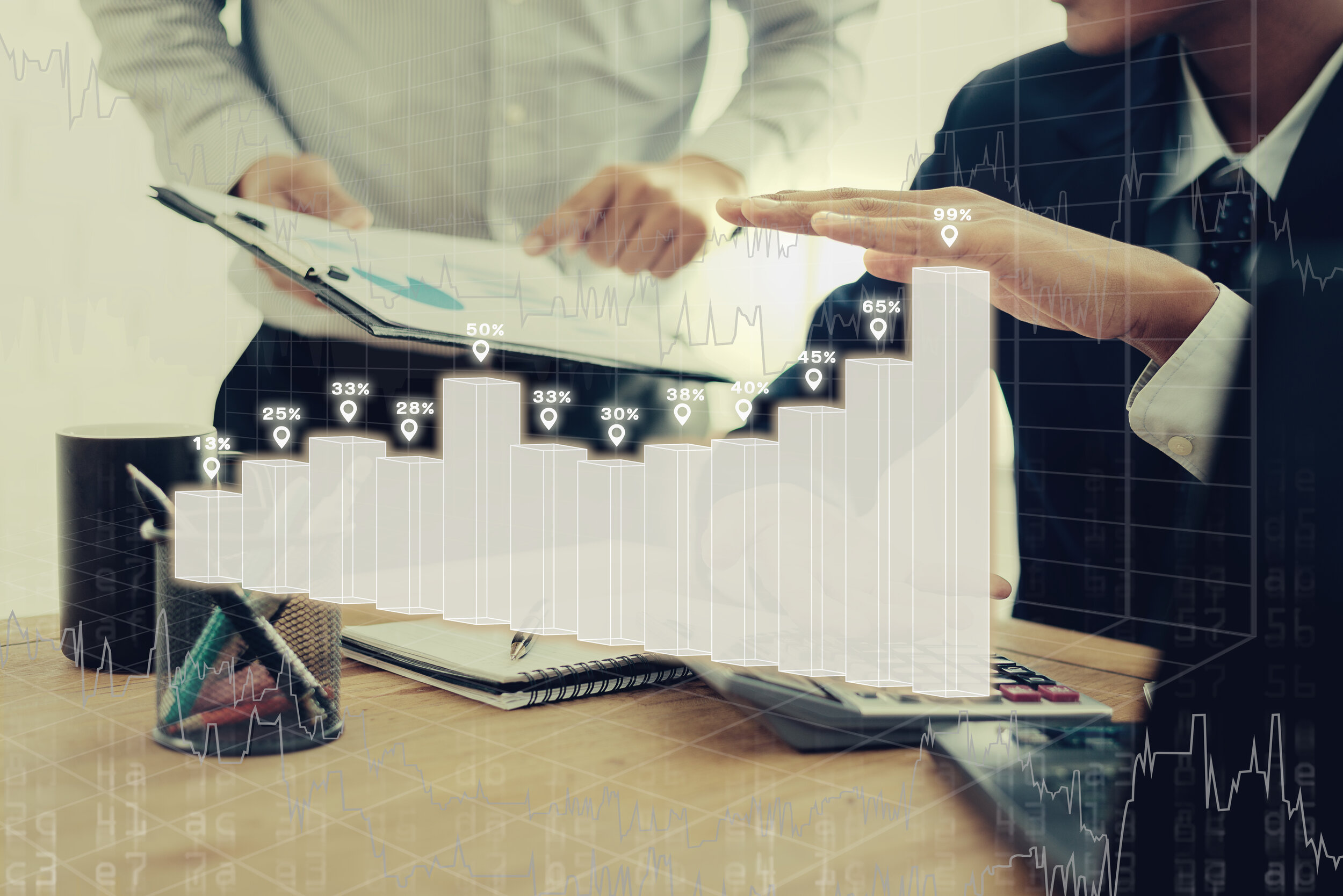
Lean Manufacturing
Driving Continuous Improvement
Lean Manufacturing Overview
Lean Manufacturing is our engine for driving Continuous Improvement across the whole business or whole supply chain. MCP can rapidly define an improvement programme tailored to generate the greatest and quickest benefits to any business through deployment of our ‘Lean CI Diagnostic’ that benchmarks your current state against industry best practice.
MCP will select an appropriate menu of lean tools and implement, support, and embed with management and staff through a highly visible project plan built around the DMAIC methodology (Define, Measure, Analyse, Improve, Control) and usually include performance and financial gains.
LEAN Continuous Improvement (CI) complements our core equipment and maintenance optimisation tools and programmes, and can be delivered either as independent interventions, or in-conjunction with the aforementioned. MCP can apply lean solutions for specific opportunities, or apply as business-wide total transformations of processes and ‘cultural change’.
Lean Manufacturing Approach
MCP employs key tools and techniques and devises an optimum combination to support individual consultancy services and products. Here are the key tools and techniques, although this is not exhaustive, as MCP Lean CI Consultants & Coaches are experienced in the total range of LEAN CI tools and techniques:
Overall Equipment Effectiveness (OEE)
Change-Over Reduction (SMED)
Workplace Organisation (5S/Standard Work)
Visual & Short Interval Management
Value Stream Mapping
Process Capability and SPC Continuous Flow
Kanban Kaizen/Kaizen Blitz
Fool Proofing/Poke Yoke
Root Cause Analysis
Gemba
MCP employs the Six Sigma methodology of ‘DMAIC’ to effectively manage the whole programme, gain client buy-in for those involved with the programme, and provide visual evidence of demonstrable programme progress through each stage.
MCP Consultants, Coaches, & Trainers are LEAN accredited, who have delivered major improvements in earlier corporate industrial roles, who now apply their proven experience across many industries.
Lean Manufacturing Benefits
MCP have a huge advantage; as experts in manufacturing services. As complementary core product offerings, we can maximise both LEAN CI and these product offerings as there are high synergy levels between them. In many cases, our Maintenance Programmes employ LEAN CI tools and Techniques, whilst our LEAN CI programmes often employ Overall Equipment Effectiveness (OEE -which optimises Availability, Performance, and Quality), Total Productive Maintenance (TPM), and our Asset Maintenance Improvement System (AMIS).
Changing processes invariably means a change in the way people work. Matching the organisation to the new environment demands experience in change management, process re-engineering, and cultural change – creating the enthusiasm for sustainable change, developing job profiles, raising people engagement, and creating new structures and whole new ‘ways of working’.
Team working is the foundation of successful organisations and the partner of LEAN CI. The identification of common goals and development of sound communication channels is self-evidently important and failures in internal co-ordination are frequently difficult to identify. MCP understands the environment in which your people work – we use their language and, through this common understanding, we can deliver highly effective team development training through our LEAN CI programme. The tools of Visual & Short Interval Management and Gemba (managing by walkabout and face-to-face communication) are key MCP enablers.
MCP can deploy a 20-step Diagnostic Tool to rapidly determine an organisations’ ‘current state’ against industry best practice. This can be delivered at operational level and in conjunction with a Management Commitment Assessment to establish how well Lean is supported and driven at the top-level. These diagnostics identify both quick wins and long-term needs on the journey to best practice.